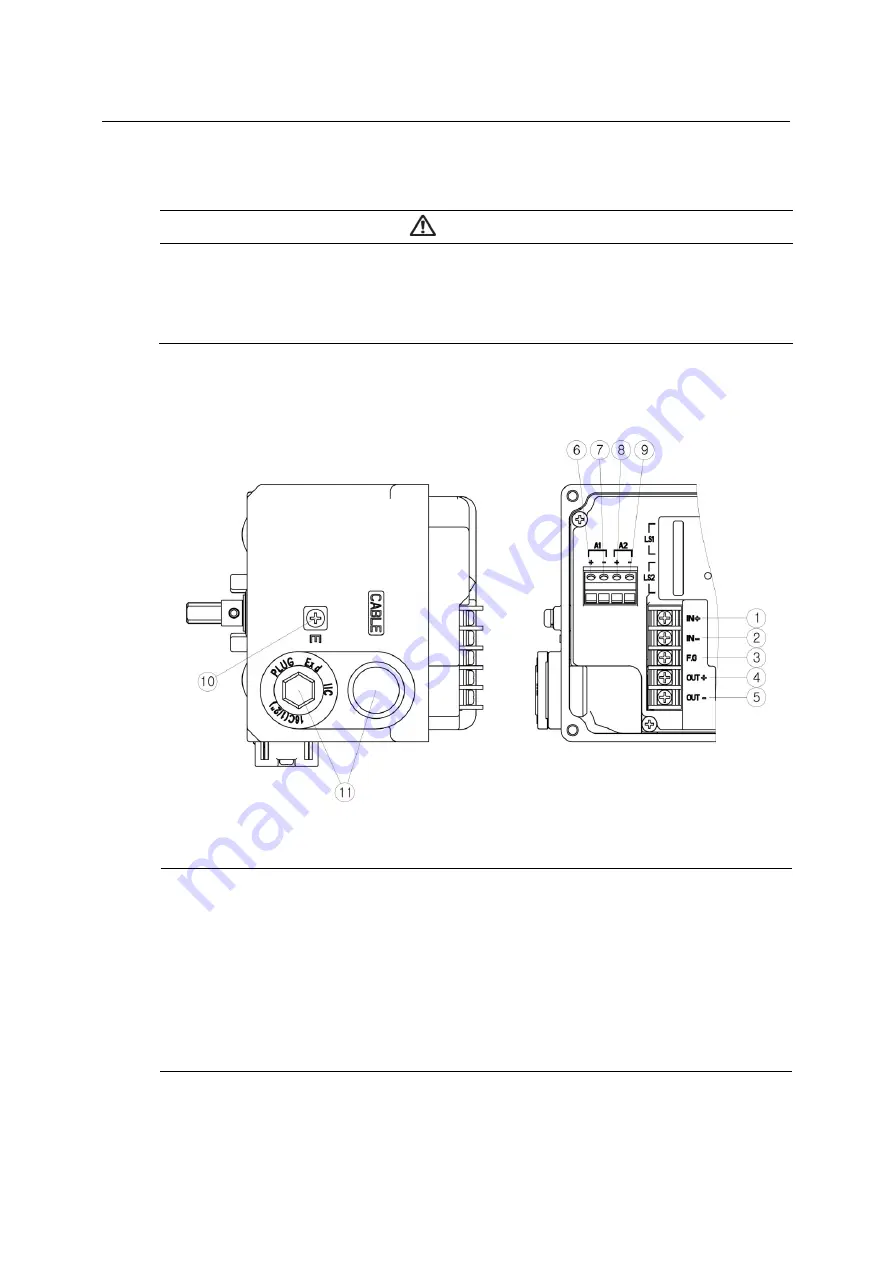
29
Smart valve positioner
TS800/TS805 Series
tissin
5 Electrical connection
5.1 Terminal description
①
Input signal (+)
②
Input signal (-)
③
Internal ground
④
Feedback signal (+)
⑤
Feedback signal (-)
⑥
Alarm1 signal (+)
⑦
Alarm1 signal (-)
⑧
Alarm2 signal (+)
⑨
Alarm2 signal (-)
⑩
External ground bolt
⑪
Conduit
WARNING
Be sure to always check that the electrical load is within the stated range on the label.
Exceeding the rating might cause a malfunction to circuit boards or burn out electrical
components.
Check polarity of + and – exactly and connect wires.