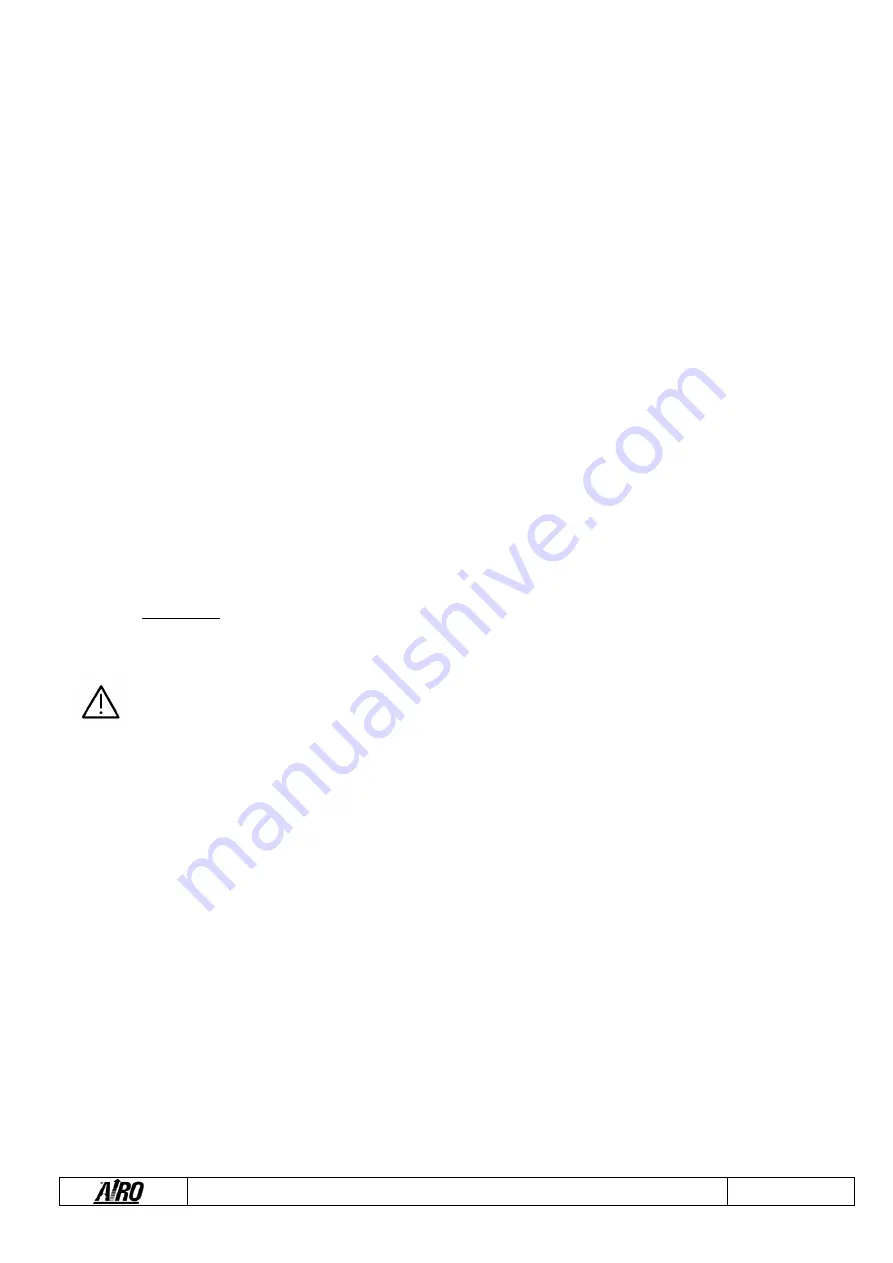
Use and Maintenance Manual - R13 R17 Series
Page 66
Copies of the analysis report must be kept in the check register. This is mandatory.
7.2.3.7
Mix
Mixtures with other biodegradable oils are not allowed.
The remaining amount of mineral oil must not exceed 5% of total filling quantity as long as the mineral oil is suitable for the same
use.
7.2.3.8
Micro-filtration
When making the conversion on second-hand machines, always take into account the high dirt dissolution power of biodegradable
oil.
After conversion, the dissolution of fault-causing deposits in the hydraulic system could occur. In extreme cases, washing the seal
housings can cause greater leaks.
To prevent faults as well as avoid any negative effect on oil quality, after the conversion, it is best to filter the hydraulic system
using a micro-filtration system.
7.2.3.9
Disposal
The biodegradable oil, inasmuch as saturated ester, is suitable for both thermal and material re-use.
It therefore provides the same disposal / re-use options as mineral based old oil.
Such oil can be incinerated whenever local laws allow.
Recycling the oil is preferable to disposal on dumps or incineration.
7.2.3.10
Topping up
The oil must
ONLY EVER
be topped up with the same product.
Note:
Max water contamination is 0.1%.
During oil change or topping up, do not discard the hydraulic oil in the environment.
Summary of Contents for AIRO R Series
Page 16: ...Use and Maintenance Manual R13 R17 Series Page 16 Fig 3...
Page 21: ...Use and Maintenance Manual R13 R17 Series Page 21 Fig 4...
Page 81: ...Use and Maintenance Manual R13 R17 Series Page 81...
Page 98: ...Use and Maintenance Manual R13 R17 Series Page 98...
Page 99: ...Use and Maintenance Manual R13 R17 Series Page 99 12 WIRING DIAGRAM 043 08 001...
Page 100: ...Use and Maintenance Manual R13 R17 Series Page 100 043 08 002...
Page 101: ...Use and Maintenance Manual R13 R17 Series Page 101...
Page 103: ...Use and Maintenance Manual R13 R17 Series Page 103 059 08 005 CA1...
Page 104: ...Use and Maintenance Manual R13 R17 Series Page 104 059 08 007 CR...
Page 105: ...Use and Maintenance Manual R13 R17 Series Page 105 059 08 001...
Page 106: ...Use and Maintenance Manual R13 R17 Series Page 106 059 08 006...
Page 107: ...Use and Maintenance Manual R13 R17 Series Page 107...
Page 108: ...Use and Maintenance Manual R13 R17 Series Page 108 043 08 017...
Page 109: ...Use and Maintenance Manual R13 R17 Series Page 109 059 08 012...