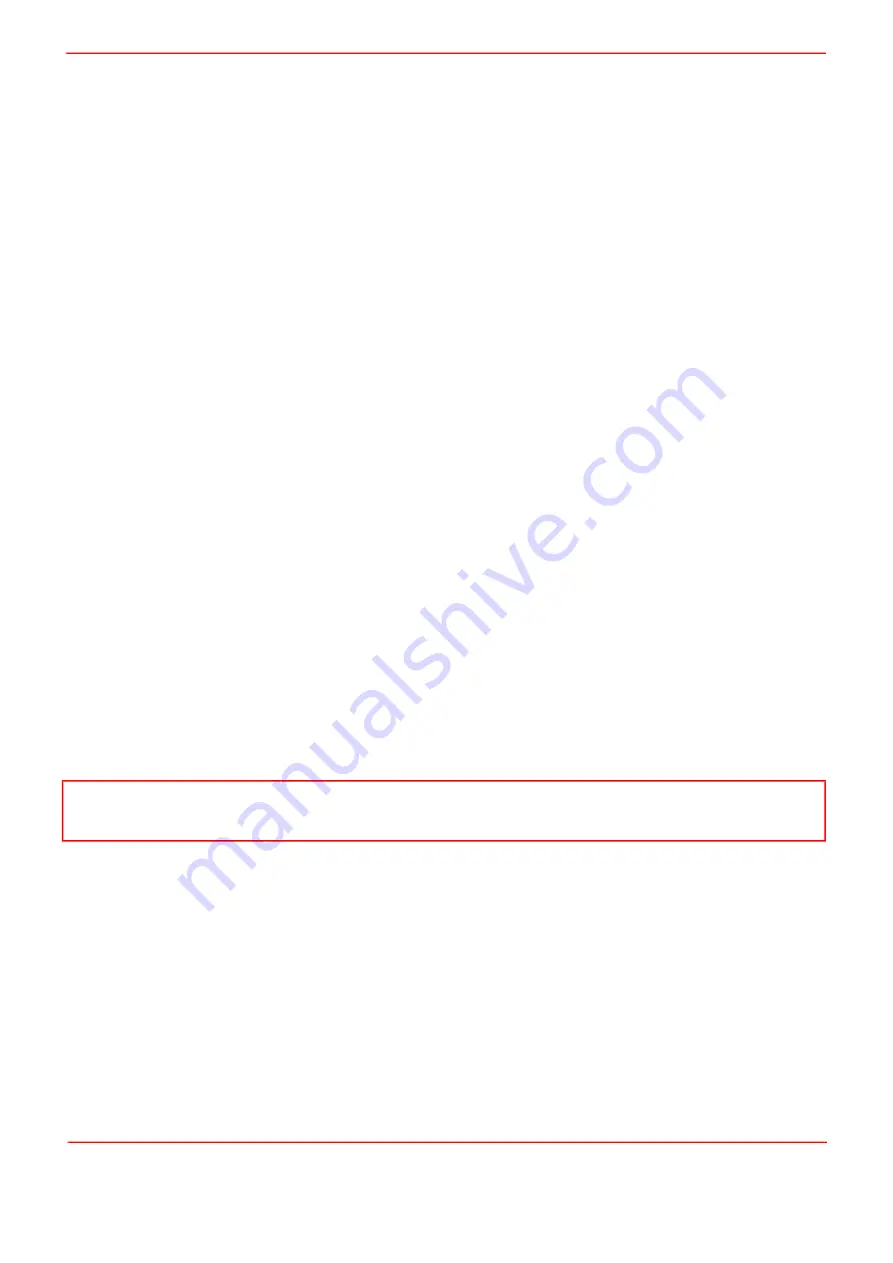
Rev B Sept 2020
Page 1
Chapter 1 Overview
Chapter 1 Overview
1.1 Introduction
The NanoTrak
®
Controller represents the latest developments in automated optical alignment technology. Its space-saving
design combines an active-feedback optical alignment system and a two-channel piezoelectric controller in a single unit,
allowing the user to align optical fibers and optimize the coupling of light into and out of photonic devices. Operator interaction
is via the top panel menu or an intuitive software interface. It is available in two wavelength ranges, 900 - 1700 nm (KNA-IR)
and 320 - 1000 nm (KNA-VIS).
The controller is supplied with a full suite of software support tools. An intuitive graphical instrument panel allows immediate
control and visualization of the operation of the NanoTrak controller, and any other controllers that are installed in the system.
See Section 1.3. for a full description of the software.
The unit operation is fully configurable (parameterized); key settings are adjustable through the graphical interface panel.
Track or Latch operating modes can be selected 'on the fly', and in both modes the display can be changed to show drive
voltage or position (in microns). In the FEEDBACK (closed loop) operation mode, both the P & I (proportional and integral)
components of the feedback control loop can be altered to adjust the servo loop response. For convenience and ease of use,
adjustment of many key parameters is possible through direct interaction with the graphical panel. For example, the output
drive voltage or position can be adjusted by rotating a "software-panel" control knob (see the tutorial in Chapter 4 for further
details). Note that all such settings and parameters are also accessible through the programmable interfaces which allow the
user to build automated alignment routines. See Section 1.3. for a full description of the APT software.
The key innovation of the Thorlabs range of controllers and associated mechanical products is the ease and speed with which
complete automated alignment systems can be engineered at both the hardware and software level. All controllers in the
range are equipped with USB connectivity. The 'multi-drop' USB bus allows multiple units to be connected to a single controller
PC using commerical USB hubs and cables. When planning an alignment application, simply add up the number and type of
drive channels required and connect together the associated number of controllers.
1.2 Power Options
A compact power supply unit (TPS002) is available from Thorlabs. This power supply unit is designed to take up minimal space
and can be mounted to the optical table in close proximity to the driver units, connected via short power leads. Although the
TPS002 has two outputs, it should not be used to drive another K-Cube as well as the KNA unit. Doing so could exceed its
current limits.
As a further level of convenience when using these controllers, Thorlabs also offers the new K-Cube Controller Hubs (KCH301
and KCH601). These products have been designed specifically with multiple K-Cube operation in mind in order to simplify
issues such as cable management, power supply routing and different optical table mounting scenarios. The KCH301 hub
provides power distribution for up to three K-Cubes, while the KCH601 hub provides power distribution for up to six K-Cubes.
Either hub requires only a single power connection.
The Controller Hub comprises a slim base-plate type carrier with electrical connections located on the upper surface: the
KCH301 measures 193.5 mm x 70.0 mm x 24.0 mm (7.62" x 2.76" x 0.94") and accepts up to three K-Cubes while the KCH601
measures 376.5 mm x 70.0 mm x 24.0 mm (14.82" x 2.76" x 0.94") and accepts up to six K-Cubes.
1.3 PC Software Overview
1.3.1 Introduction
As a member of the APT range of controllers, the KNA NanoTrak K-Cube shares many of the associated software benefits.
This includes USB connectivity (allowing multiple units to be used together on a single PC), fully featured Graphical User
Interface (GUI) panels, and extensive software function libraries for custom application development.
The APT software suite supplied with all APT controllers provides a flexible and powerful PC based control system both for
users of the equipment, and software programmers aiming to automate its operation.
For users, the APTUser (see Section 1.3.2.) and APTConfig (see Section 1.3.3.) utilities allow full control of all settings and
operating modes enabling complete ‘out-of-box’ operation without the need to develop any further custom software. Both
utilities are built on top of a sophisticated, multi-threaded ActiveX ‘engine’ (called the APT server) which provides all of the
necessary APT system software services such as generation of GUI panels, communications handling for multiple USB units,
and logging of all system activity to assist in hardware trouble shooting. It is this APT server ‘engine’ that is used by software
developers to allow the creation of advanced automated positioning applications very rapidly and with great ease. The APT
server is described in more detail in Section 1.3.4.
Note
A KCH series hub can only be used to provide power and USB connection to the host PC. A hub cannot be used to
communicate between a KNA-IR or KNA-VIS unit and other K-Cubes also fitted to the hub.
Summary of Contents for NanoTrak KNA-IR
Page 47: ...www thorlabs com ...