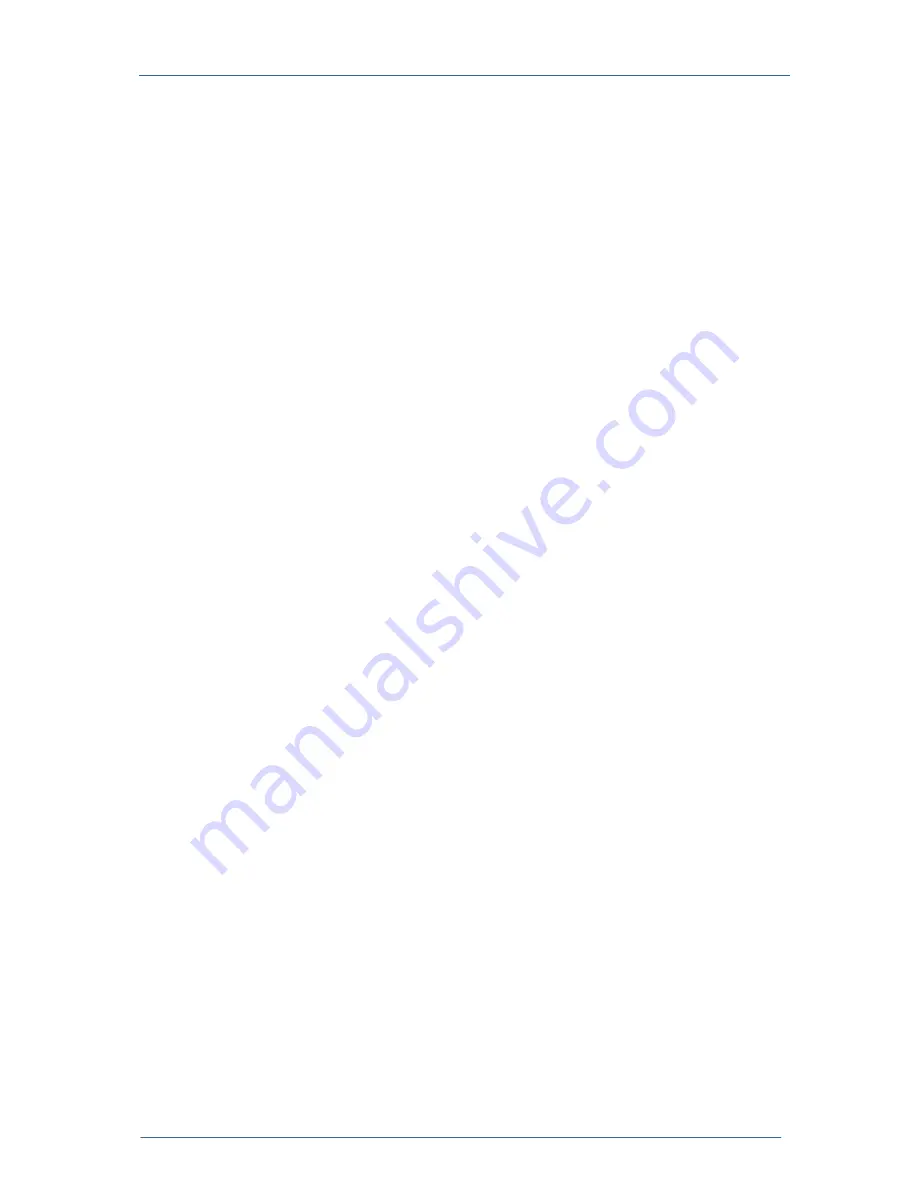
2.15 Setup and function of temperature controllers
ITC500 / page 43
So the temperature of the laser can be influenced with the TEC current. The
quantity of heat flowing from the laser into the copper bloc and the size of the
block effects the thermal settling time of the setup.
Usually very small components (laser diodes) are tempered with relatively extensive
cooling elements (TEC elements). Thus the thermal energy is lead away quickly and
the components are as far as possible kept at a constant temperature.
2.15.2 Demands to the ideal temperature control loop
1. Knowledge of the absolute laser temperature
2. Stability of the laser temperature under any influence
3. Immediate settling to a new laser temperature when changing the set value of the
temperature
2.15.3 Influences on the real temperature control loop
To 1: Offset and gain errors of the sensor will only allow a relative knowledge about
the laser temperature.
The sensor will never be fixed to the laser chip in such a way that it will
exclusively measure its temperature. So the temperature in the copper bloc
being inhomogeneous due to the heat flow will be measured as well. Even
within the laser chip the temperature will not be the same in all spots.
Possibility of optimization: calibration of sensor
To 2. If the internal power dissipation changes (e.g. the laser current is changed)
also the temperature gradient between laser and sensor will change. This
results in a measurement error depending on the mechanical setup
laser/sensor. Changes in the ambient temperature, however, will be
compensated well from the control loop since they will almost only have an
effect on the heat slope between TEC element and cooling element.
Possibility of optimization: best possible thermal design
Summary of Contents for ITC502
Page 2: ...Version 2 16 Date 25 07 2006 Copyright 2006 Thorlabs ...
Page 8: ......