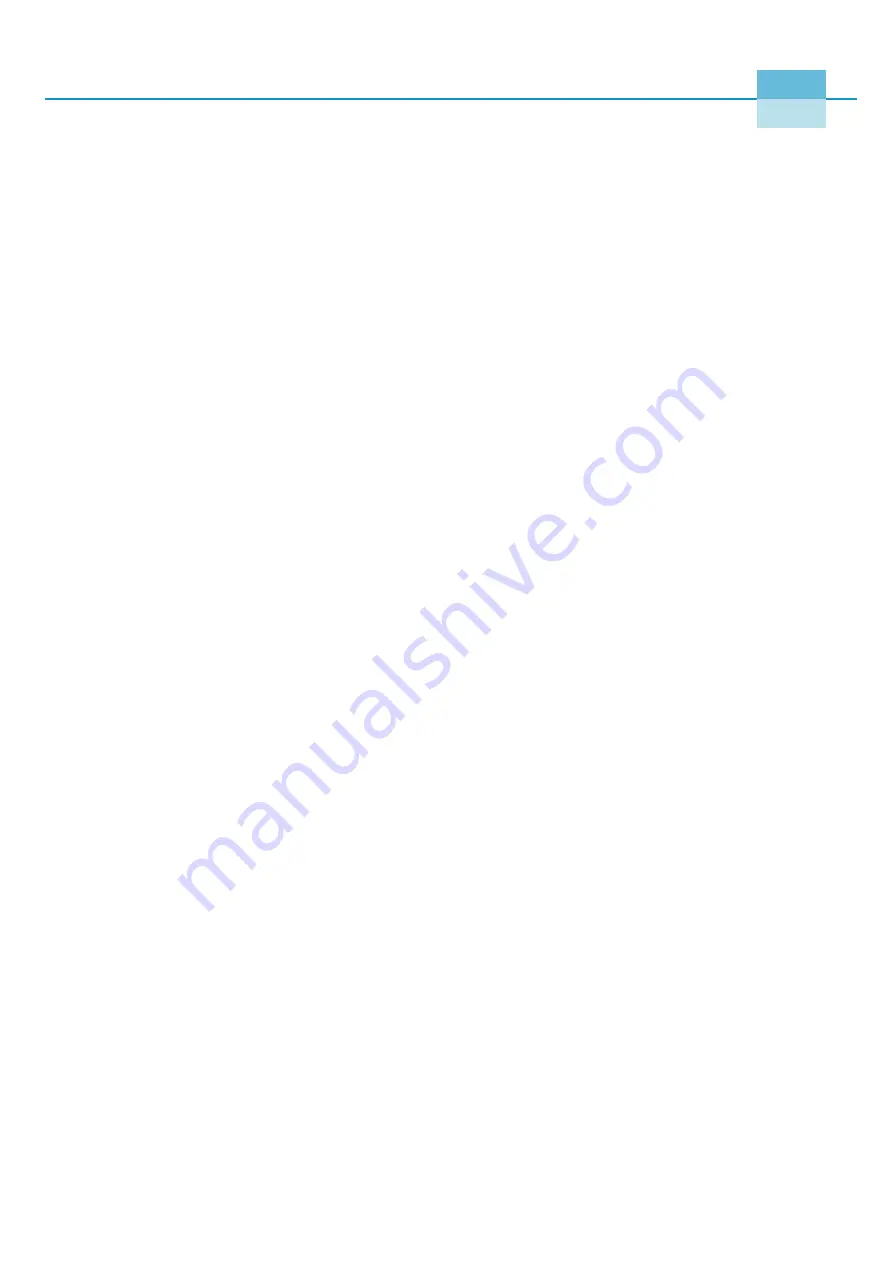
Thermo Scientific
Heratherm
i
L
Figure 3-1 Table-top oven units OGS 60 / OGS 100 / OGS 180, dimensions and required clearances ................. 3-5
Figure 3-2 Floor stand ovens OGS 400, dimensions and required clearances ......................................................... 3-6
Figure 3-3 Floor stand ovens OGS 750, dimensions and required clearances ......................................................... 3-7
Figure 3-4 Lift Points............................................................................................................................................. 3-8
Figure 4-1 Heratherm OGS 60 / OGS 100 / OGS 180 Series Front View ............................................................ 4-2
Figure 4-2 Heratherm OGS 60 / OGS 100 / OGS 180 Series Rear View .............................................................. 4-3
Figure 4-3 Heratherm OGS 400 Series Front View ............................................................................................... 4-4
Figure 4-4 Heratherm OGS 400 Series Rear View ................................................................................................. 4-5
Figure 4-5 Heratherm OGS 750 Series Front View ............................................................................................... 4-6
Figure 4-6 Heratherm OGS 750 Series Rear View ................................................................................................. 4-7
Figure 4-7 Heratherm OMS Series Front View...................................................................................................... 4-8
Figure 4-8 Heratherm OMS Series Rear View ....................................................................................................... 4-9
Figure 4-9 Sensor Mounting Location - OGS Series and OMS Series - Table-top units ........................................ 4-10
Figure 4-10 Sensor Mounting Location - OGS Series and OMS Series - Floor stand units .................................... 4-10
Figure 4-11 Signal Interfaces and Power Socket ..................................................................................................... 4-12
Figure 4-12 Back panel – 3P unit electronics ......................................................................................................... 4-12
Figure 4-13 Shelf System - OGS Series Oven - Table-top units ............................................................................. 4-13
Figure 4-14 Shelf System - OMS Series Oven - Table-top units............................................................................. 4-14
Figure 4-15 Tube Access Ports............................................................................................................................... 4-15
Figure 5-1 Sliding the Retaining Spring into the Support Rail ............................................................................... 5-1
Figure 5-2 OGS Series - Installing the Shelving ..................................................................................................... 5-2
Figure 5-3 OMS Series - Installing the Shelving..................................................................................................... 5-2
Figure 5-4 Support Rail Installation....................................................................................................................... 5-3
Figure 5-5 Installing the Rear Air Baffle................................................................................................................. 5-4
Figure 5-6 Removing the Bottom Panel................................................................................................................. 5-5
Figure 5-7 Bottom Panel Removed ........................................................................................................................ 5-5
Figure 5-8 Removing the Lateral Air Baffle............................................................................................................ 5-6
Figure 5-9 Removing the bottom plate .................................................................................................................. 5-7
Figure 5-10 Removing the left and right support profiles....................................................................................... 5-7
Figure 5-11 Removing the rear air baffle OGS 400/750 ........................................................................................ 5-7
Figure 5-12 Shelf Support Bracket Installation ...................................................................................................... 5-8
Figure 5-13 Wire-mesh shelf.................................................................................................................................. 5-9
Figure 5-14 AC Power Supply Socket .................................................................................................................... 5-10
Figure 5-15 Power supply connection for 3P units................................................................................................. 5-11
Figure 7-1 Control panel for Heratherm OGS Series and OMS Series Ovens........................................................ 7-1
List of Figures
Summary of Contents for OGS 100
Page 1: ......
Page 6: ...Contents iv Heratherm Thermo Scientific...
Page 46: ...Product Description Tube Access Ports 4 16 Heratherm Thermo Scientific...
Page 60: ...Start up Connecting the RS 232 Interface 5 14 Heratherm Thermo Scientific...
Page 76: ...Handling and Control Switching the Oven Off Powering Down 7 14 Heratherm Thermo Scientific...
Page 78: ...Shut down Shutting the Oven Down 8 2 Heratherm Thermo Scientific...
Page 82: ...Cleaning and Disinfection Wipe Spray Disinfection 9 4 Heratherm Thermo Scientific...
Page 88: ...Maintenance Returns for Repair 10 6 Heratherm Thermo Scientific...
Page 104: ...Spare Parts and Accessories 14 6 Heratherm Thermo Scientific...
Page 106: ...Device Log 15 2 Heratherm Thermo Scientific...
Page 108: ...Contact 16 2 Heratherm Thermo Scientific...