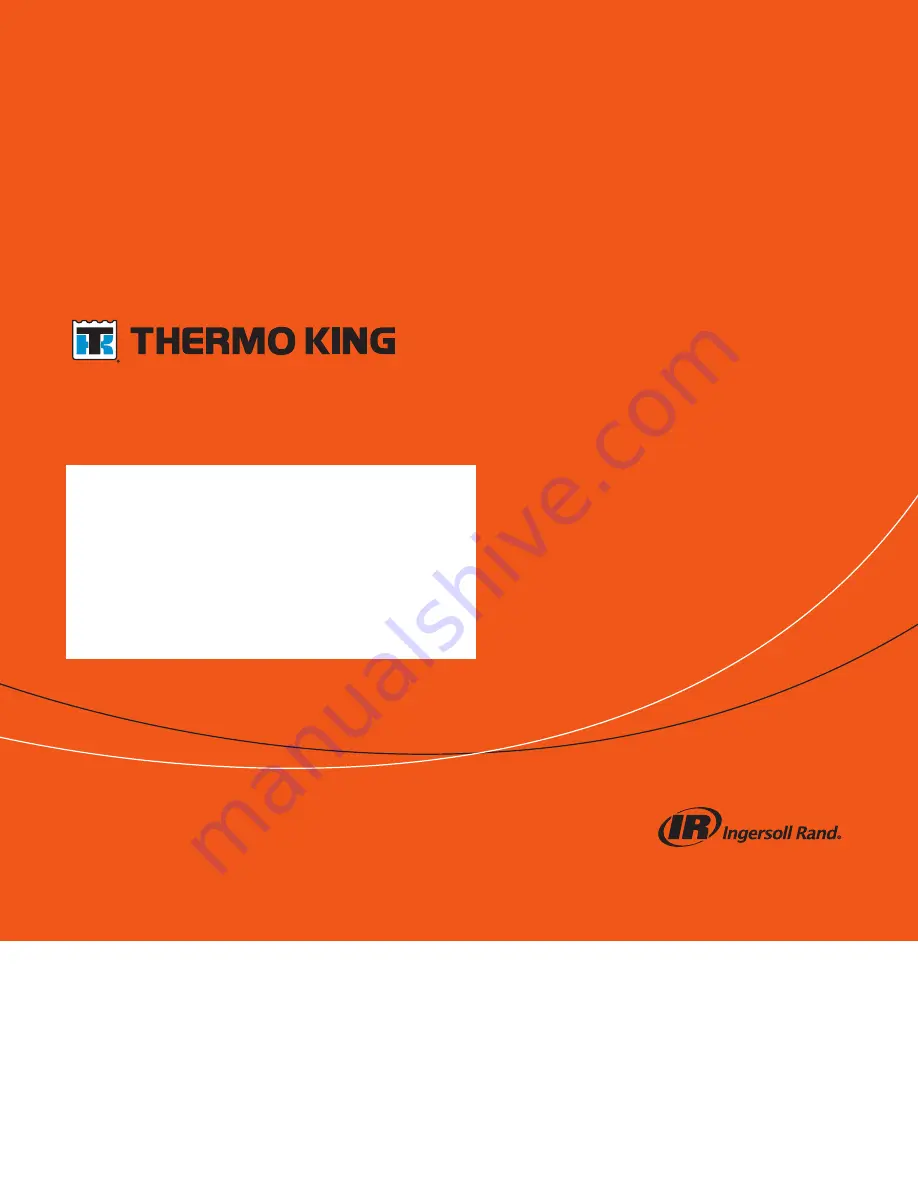
Installation Manual
Ingersoll Rand’s Climate Solutions sect
or delivers energy-efficient HV
ACR solutions f
or
customers globally
. Its world class brands include
Thermo King, the leader in transpor
t
temper
ature c
ontrol and
Trane, a pr
ovider of energy efficient heating, ventilating and air
conditioning syst
ems, building and contr
acting servic
es, parts suppor
t and advanced c
ontrols
for c
ommercial buildings and homes.
©2011 Ingersoll-Rand Company
Printed in U.S.A. on R
ecycled Paper
Truck Edition (TSA, EMEIA and AP)
Single Temperature Systems
T-580R, T-800M and T-1000M (with TSR Controller)
T-680S, T-880S, T-1080S (with SR-3 Controller)
T-600R, T-680R, T-800R, T-880R, T-1000R & T-1080R (with SR-3 Controller)
T-1200R (EMEIA Only with SR-3 Controller)
TK 55212-1-IM (Rev. 4, 01/15)
Summary of Contents for T-1000M
Page 2: ......
Page 5: ...3 Installation Manual for T Series Systems ...
Page 12: ...10 Service Area T 580R T 600R T 680R T 680R T 680S T 800M T 800R T 880R T 880S ...
Page 13: ...11 Service Area T 1000M T 1000R T 1080R T 1080S and T 1200R ...
Page 14: ...12 Remote Power Receptacle Dimensions OPTION NORTH AMERICAN MODELS INTERNATIONAL MODELS ...
Page 15: ...13 Battery Box Dimensions OPTION ...
Page 16: ...14 Remote Status Light Dimensions OPTION ...
Page 17: ...15 HMI Controller Dimensions HMI Controller LED Display HMI Controller Graphics Display ...
Page 25: ...23 Required Tools ...
Page 27: ...25 Installation Components ...
Page 29: ...27 Uncrating the Unit ...
Page 31: ...29 Installing the Unit ...
Page 33: ...31 Installing the Hose Management Caps Cutout Guide Marks Front of Unit ...
Page 35: ...33 Installing the Hose Management System OPTION Front of Unit ...
Page 39: ...37 Securing the Evaporator Drain Hoses ...
Page 41: ...39 Installing the Fuel Pickup Tube Into a Steel or Aluminum Tank ...
Page 43: ...41 Installing the Fuel Pickup Tube Into a Plastic Tank ...
Page 45: ...43 Installing the Steel Fuel Tank 1 2 3 4 ...
Page 47: ...45 Installing the Aluminum Fuel Tank OPTION 1 2 3 4 ...
Page 49: ...47 Installing the Fuel Pump and Fuel Lines ...
Page 51: ...49 Installing the ServiceWatch Remote Download Port ...
Page 53: ...51 Installing the Remote Power Receptacle OPTION ...
Page 55: ...53 Installing the Remote Status Light OPTION ...
Page 59: ...57 Installing the Battery Box OPTION ...
Page 61: ...59 Battery Connections ...
Page 69: ...67 ...
Page 70: ......