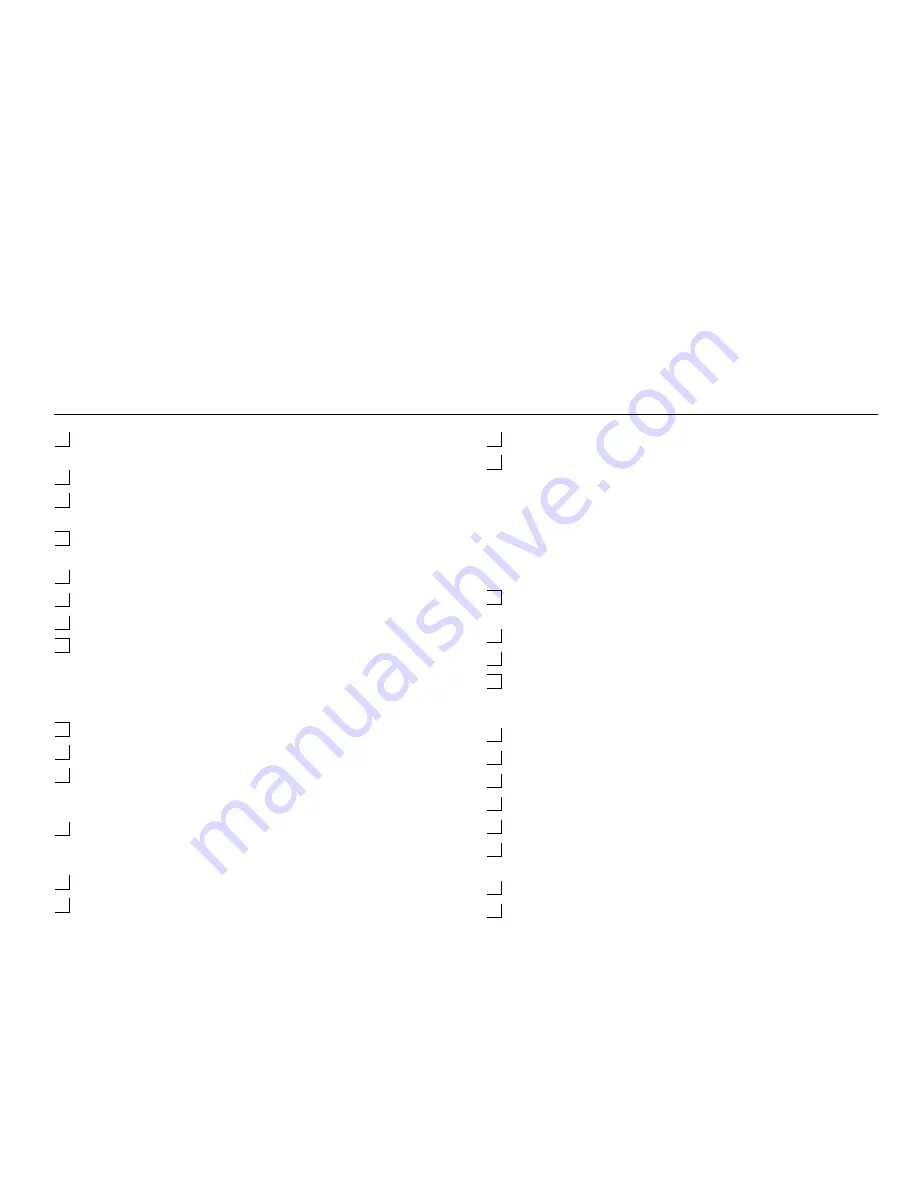
66
UNIT CHECK LIST (continued)
Observe and record refrigerant operating pressures in relation to
ambient and box temperatures.
Verify the readings above are correct for the conditions.
When box reaches 32 F (0 C) check calibration of thermostat,
thermometer and data logger.
Run unit for 30 minutes at 32 F (0 C). During this period check for
correct cycling.
Reset thermostat to 50 F (10 C).
Check throttling valve while in the heat cycle.
Check operation of Modulation system if equipped.
For Single Temp units perform a controlled check of the refrigerant
level. For Multi-temps check the charge per multi-temp unit
procedures.
MULTI-TEMP UNITS
Install the compartment bulk head(s) if equipped.
Check for correct rotation of remote evaporator fans.
Check for correct cycling and operation of remote evaporator fans.
ALL UNITS
Initiate and check defrost operation and termination.Check operation
and adjustment of damper door and remote fans. Each zone on
multi-temps must be checked for proper operation.
Set the unit for Cycle Sentry Operation.
Check for proper operation of all door switches.
Remove the compartment bulk head(s) if equipped.
Set the unit for continuous run. Continue to run the unit with the back
doors open, alternating between high speed cool and heat until at
least 6 hours (10 hours preferred) are shown on the engine run time
hour meter to ensure complete break in of the engine, time for the
belts and other moving parts to take out the initial tension and
adjustment.
ELECTRIC STANDBY OPERATIONAL CHECKS
Test AC electrical contacts and connections by connecting to AC
power and running.
Check for correct electric motor rotation.
Cycle thermostat and check for correct modes of operation.
Power source not available to test AC.
STOP UNIT
On Multi-temp units leak test interconnecting tubing.
Check and readjust all belt tensions using TK belt gauge 204-427.
Check for oil, fuel, coolant, refrigerant and exhaust leaks.
Check engine oil and coolant level.
Check entire unit for loosened hardware and fittings.
Check and adjust all skin, door and panels for correct alignment and
operation.
Complete the commissioning registration process.
Release unit.
Summary of Contents for T-1000M
Page 2: ......
Page 5: ...3 Installation Manual for T Series Systems ...
Page 12: ...10 Service Area T 580R T 600R T 680R T 680R T 680S T 800M T 800R T 880R T 880S ...
Page 13: ...11 Service Area T 1000M T 1000R T 1080R T 1080S and T 1200R ...
Page 14: ...12 Remote Power Receptacle Dimensions OPTION NORTH AMERICAN MODELS INTERNATIONAL MODELS ...
Page 15: ...13 Battery Box Dimensions OPTION ...
Page 16: ...14 Remote Status Light Dimensions OPTION ...
Page 17: ...15 HMI Controller Dimensions HMI Controller LED Display HMI Controller Graphics Display ...
Page 25: ...23 Required Tools ...
Page 27: ...25 Installation Components ...
Page 29: ...27 Uncrating the Unit ...
Page 31: ...29 Installing the Unit ...
Page 33: ...31 Installing the Hose Management Caps Cutout Guide Marks Front of Unit ...
Page 35: ...33 Installing the Hose Management System OPTION Front of Unit ...
Page 39: ...37 Securing the Evaporator Drain Hoses ...
Page 41: ...39 Installing the Fuel Pickup Tube Into a Steel or Aluminum Tank ...
Page 43: ...41 Installing the Fuel Pickup Tube Into a Plastic Tank ...
Page 45: ...43 Installing the Steel Fuel Tank 1 2 3 4 ...
Page 47: ...45 Installing the Aluminum Fuel Tank OPTION 1 2 3 4 ...
Page 49: ...47 Installing the Fuel Pump and Fuel Lines ...
Page 51: ...49 Installing the ServiceWatch Remote Download Port ...
Page 53: ...51 Installing the Remote Power Receptacle OPTION ...
Page 55: ...53 Installing the Remote Status Light OPTION ...
Page 59: ...57 Installing the Battery Box OPTION ...
Page 61: ...59 Battery Connections ...
Page 69: ...67 ...
Page 70: ......