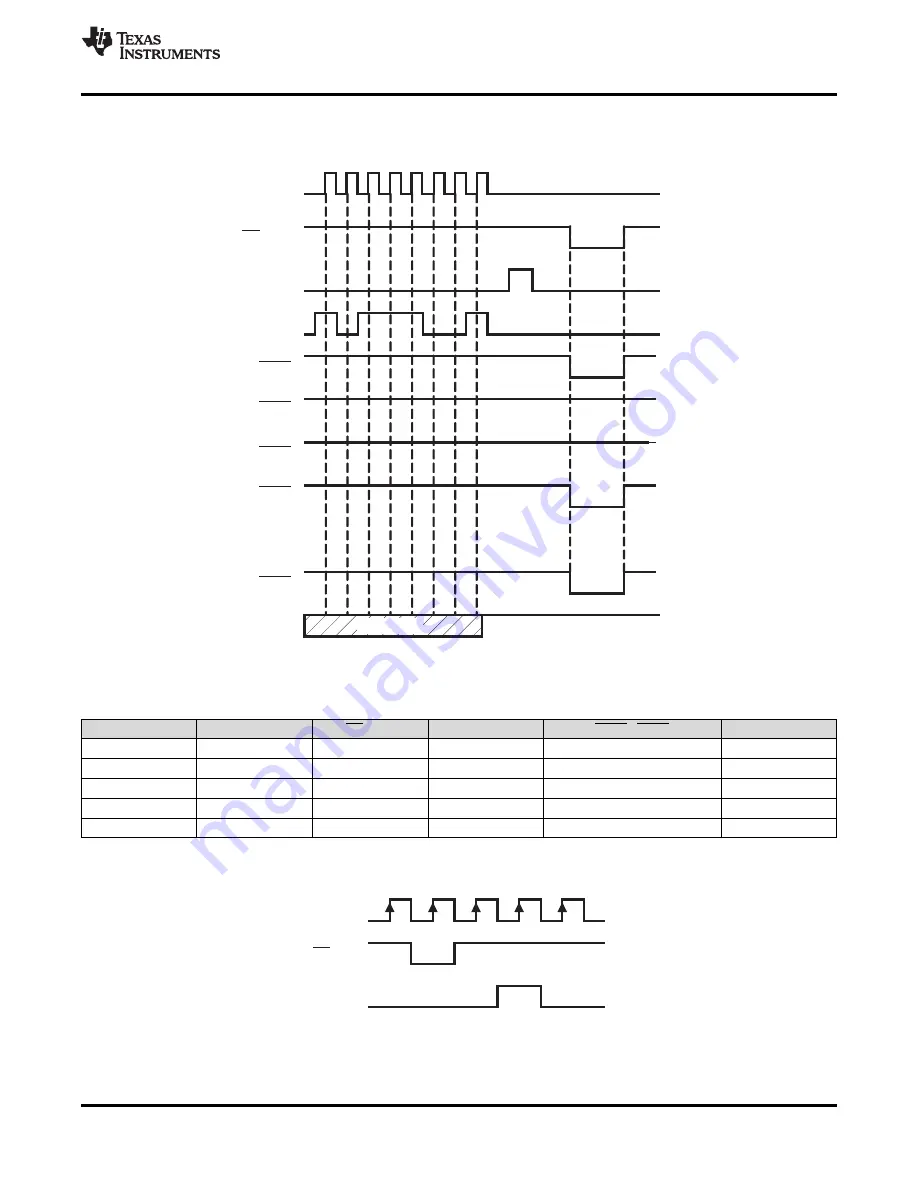
1
2
3
4
5
1
0
1
1
1
1
0
0
0
0
CLK
OE(ED2)
LE(ED1)
1
2
3
0
4
6
7
5
0
1
off
on
off
on
off
on
off
on
off
on
Don't care
CLK
OE(ED2)
LE(ED1)
SDI
OUT0
OUT1
OUT2
OUT3
OUT7
SDO
SLVS695D – JUNE 2007 – REVISED JANUARY 2015
Device Functional Modes (continued)
Figure 11. Normal Mode
Table 4. Truth Table in Normal Mode
CLK
LE(ED1)
OE(ED2)
SDI
OUT0...OUT7
SDO
↑
H
L
Dn
Dn...Dn – 7
Dn – 7
↑
L
L
Dn + 1
No change
Dn – 6
↑
H
L
Dn + 2
Dn + 2...Dn – 5
Dn – 5
↓
X
L
Dn + 3
Dn + 2...Dn – 5
Dn – 5
↓
X
H
Dn + 3
Off
Dn – 5
The signal sequence shown in
makes the TLC591x enter Current Adjust and Error Detection Mode.
Figure 12. Switching to Special Mode
In the Current Adjust Mode, sending the positive pulse of LE(ED1), the content of the shift register (a current
adjust code) is written to the 8-bit configuration latch (see
).
Copyright © 2007–2015, Texas Instruments Incorporated
17
Product Folder Links: