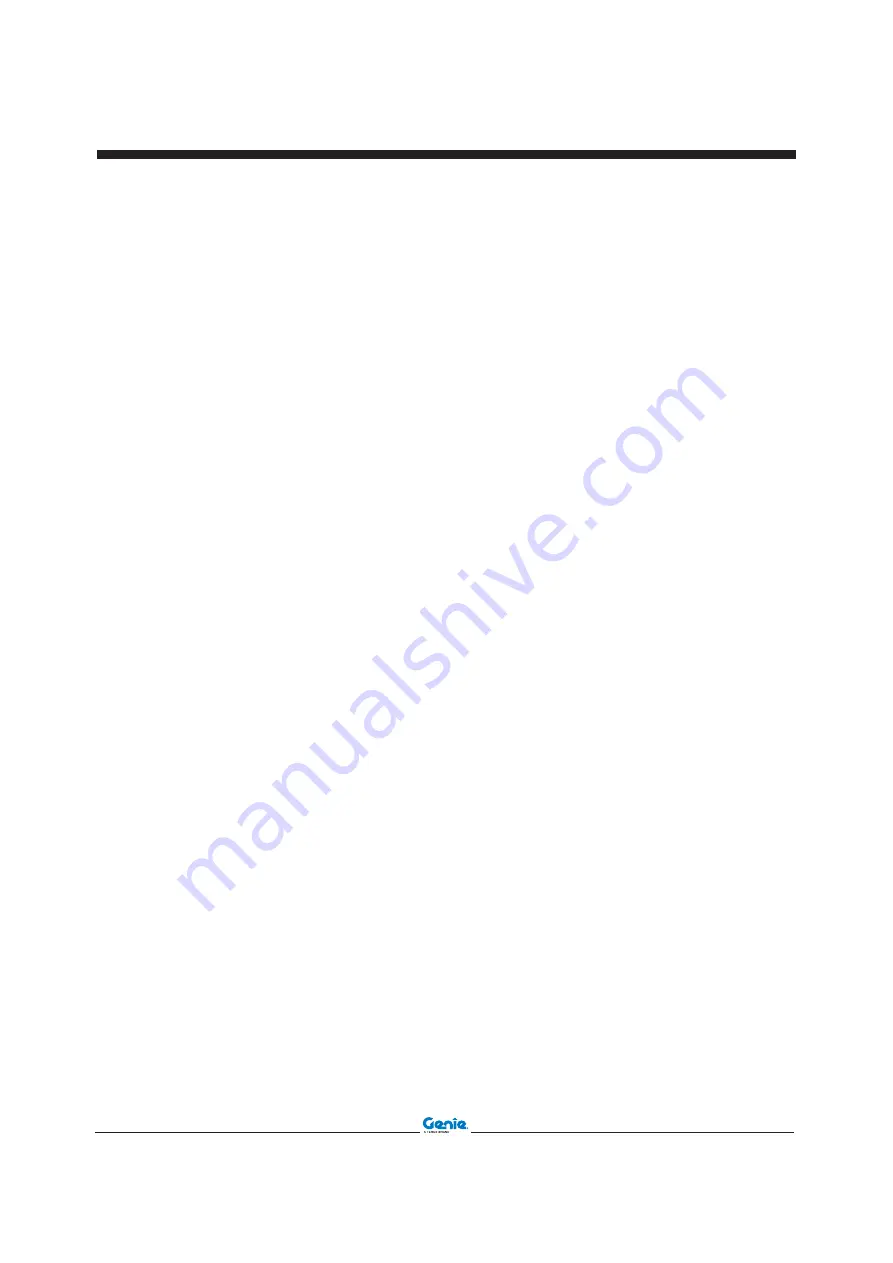
Part No. 57.4400.9203 GTH-4016SR • GTH-4018SR
3
March 2010
Section 2 • Specification
SPECIFICATION
REV A
When the pressure upstream of the heat exchanger
exceeds 8 bar, the flow rate in excess is directly
discharged to the tank through the check valve
(30)
having a cracking pressure of 8 bar indeed.
The scope of this valve is to prevent any risk of
heat exchanger damage due to excessive pressure
(machine start-up at very low temperatures).
This heat exchanger is part of the main machine
radiator (cooling also the engine) and is installed
inside the engine compartment.
The gear pump
(4)
feeds the hydraulically powered
service/emergency brakes pedal pump
(31)
which
is installed underneath the cabin bottom in such
a way the operator can easily control the service
brake circuit by a mechanical pedal which is a part
of the pump itself.
The main function of this pump is to use the
pressurized oil available from the gear pump
(4)
to
maintain two hydraulic accumulators
(32)
and
(33)
charged at a pressure not exceeding 150 bar.
The first accumulator
(32)
, having a capacity of 0.5
liters and a nitrogen pre-charge pressure of 50 bar,
feeds the service brake line whilst the second one
(33)
, having a capacity of 1.5 liters and a nitrogen
pre-charge pressure of 35 bar, feeds the parking
brake line.
The electrical pressure switch
(34)
, installed on
the service brake pressure line, signals when the
pressure is applied to the service brake line.
The electrical pressure switch
(35)
, installed on
the parking brake pressure line, signals when the
pressure charging the accumulators is too low and
then the pump
(31)
is expected to recharge them
using the flow coming from the gear pump
(4)
.
The service brake output line is linked, through the
electrical 3 ways/2 positions selector valve
(36)
,
to the wet type brake disks packages, which are
installed inside the axles.
When the selector valve
(36)
is not energized, the
brake pump
(31)
is directly linked to the brakes
disks so producing the requested braking effect
when the operator in the cabin pushes on the brake
pedal.
When the selector valve
(36)
is energized, the
service brakes ports of the front axle, receive a
pressure of 10 bar which makes stronger the effect
of the anti-slipping device, device which is installed
inside the front axle.
This low pressure is generated by a pressure
reducing valve
(37)
fed by the low pressure
generated by the transmission charge pump.
The brakes pedal pump
(31)
is also linked, through
the port “R”, to the parking brake handle selector
valve
(38)
controlling the parking brake function.
When the handle of this valve, which is located in
the cabin on left of the operator’s seat, is placed in
the parking brake “on” position, the parking brake
hydraulic line, connected to the front axle
(20)
, is
vented to the tank.
This condition allows the parking brake package,
installed inside the axle, to be self-activated,
through an internal mechanism energized by disk
springs, so maintaining the machine in the parking
condition.
On the other position of the lever, the parking
brake hydraulic line is pressurized at 30 bar so
maintaining the parking brake disks released and
then allowing the machine to move without any
braking effect.
Two electrical pressure switches
(39)
signals when
the parking brake is activated.
After the flow rate generated by the gear pump
(4)
and used by the brakes pedal pump
(31)
to maintain
the accumulators
(32)
and
(33)
charged, leaves the
brakes pedal pump itself, this is available to power
the air condition compressor hydraulic gear motor
(40)
which can be installed on the machine as an
option.
The gear pump
(3)
powers two distinct and
separated circuits: the steering circuit (priority
circuit) and the circuit driving the boom functions,
the slewing turret and the stabilizers operations
(secondary circuit).
The flow rate coming from this pump is controlled
by the load sensing priority valve
(41)
which is
controlled by the steering load sense line “LS”.
The principle of this valve is to ensure that all the
necessary flow rate is available to the steering
circuit when requested by the steering operation
and to give the exceeding flow rate to the secondary