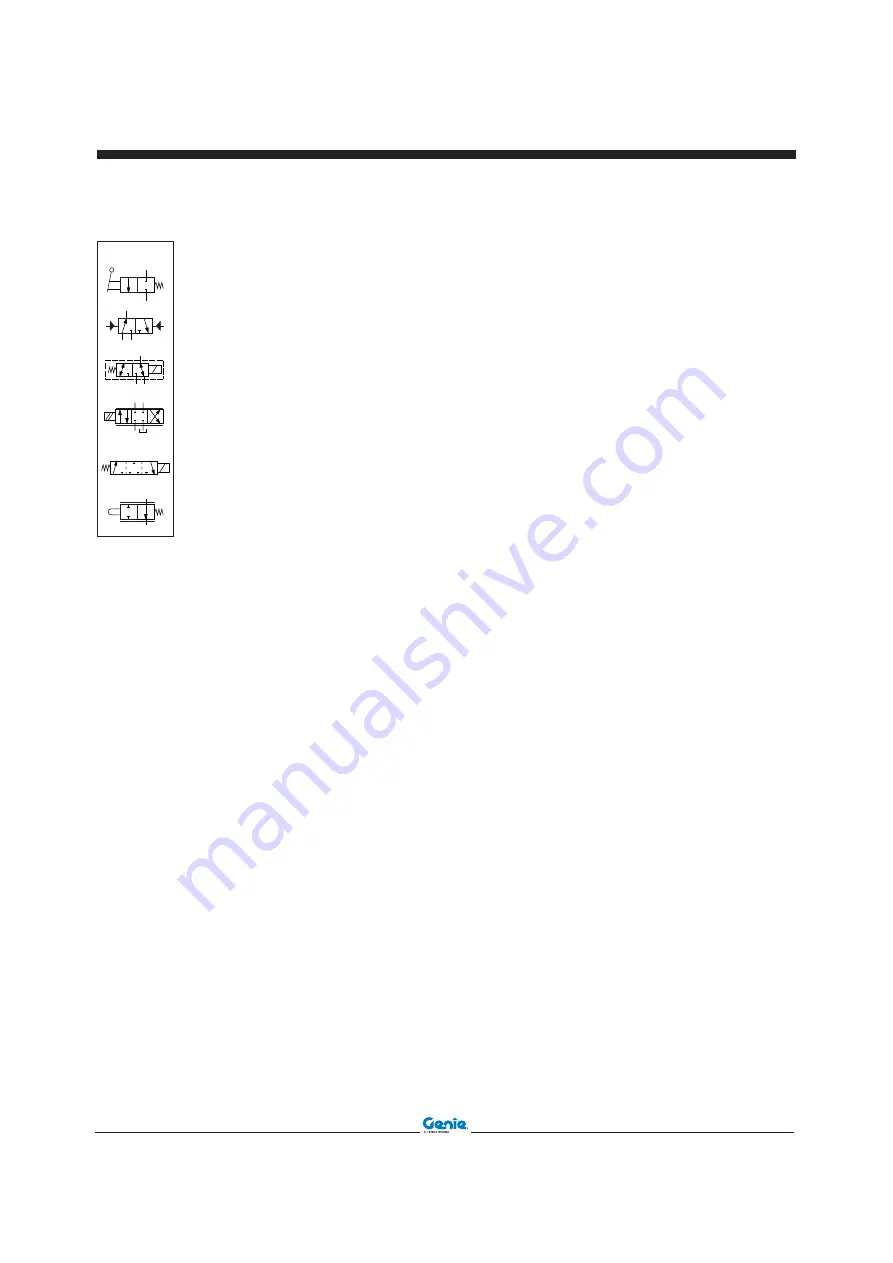
Part No. 57.4400.9203 GTH-4016SR • GTH-4018SR
93
March 2010
Section 7 • Schematics
REV A
HYDRAULIC COMPONENT LEGEND
Two-position and two-way
distributor, with manual lever
control and spring return
DISTRIBUTION - SETTING
ELEMENTS
Three-way and two-position
distributor, with hydraulic control
Electro-hydraulic single-acting
servo valve
Distributor with mechanical
control and span proportional to
the action of the same control
Two-position, three-way
distributor, with representation
of transient connection during
passage phase
Two-position, three-way
distributor, with electro-magnetic
control and spring return