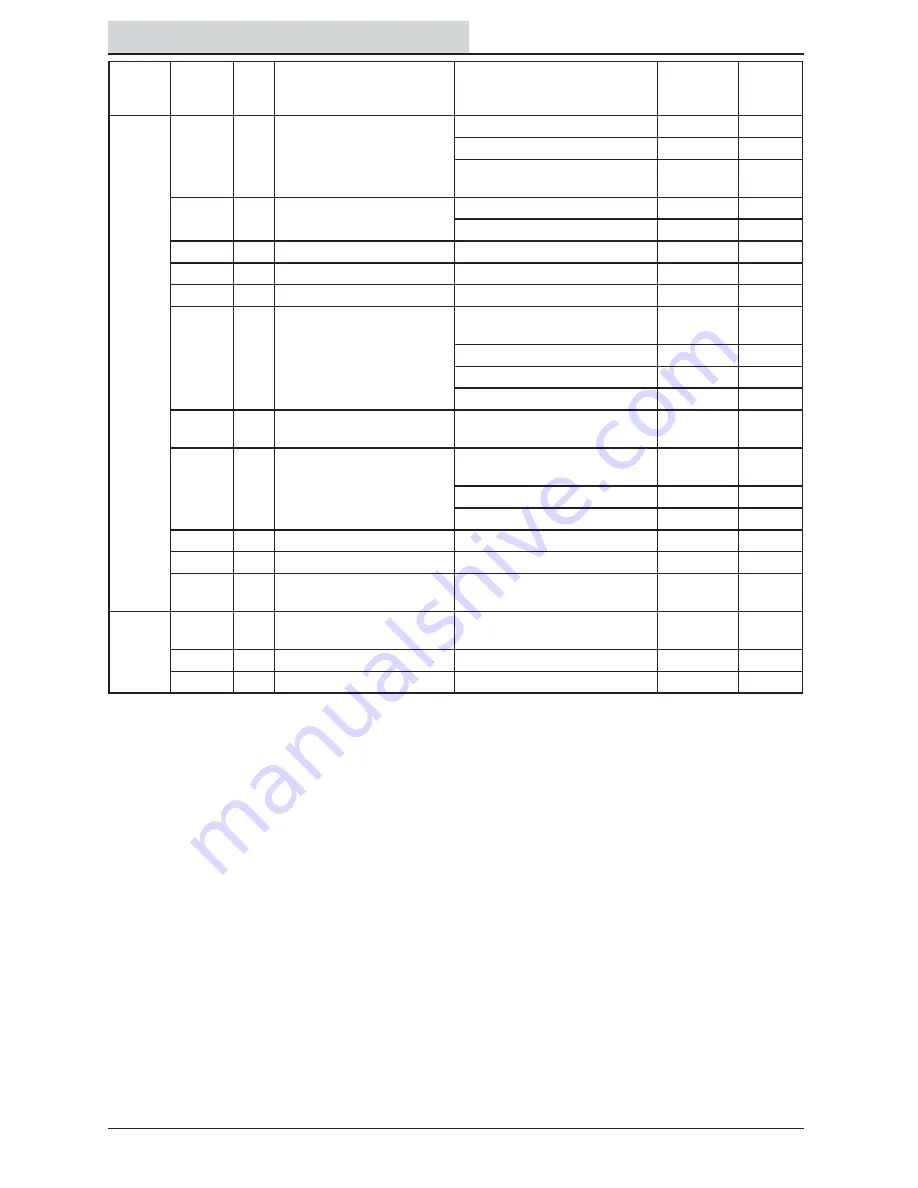
28
Sentinel 9018524 (05-2019)
MAINTENANCE
Interval
Person
Resp.
Key
Description
Procedure
Lubricant/
Fluid
No. of
Service
Points
Daily
O
1
Engine
Check air
fi
lter indicator
-
1
Empty air
fi
lter dust cap
-
1
Check air intake tubes for
damage
All
O
2
Radiator
Check coolant level in radiator
WG
1
Check and clean core exterior
-
1
O
2
Hydraulic
fl
uid cooler
Check and clean cooler
fi
ns
-
1
O
2
Turbo cooler
Check and clean cooler
fi
ns
-
1
O
2
Hydraulic
Check
fl
uid reservoir
fl
uid level
HYDO
1
O
3
Conveyor
Check chain and ratchet tips
and pins
-
2
Lubricate chain
GL
1
Clean interior
-
1
Lubricate bearings
WBG
2
O
4
Brush compartment
Check skirts for damage and
wear
-
3
O
5
Main brush
Check for damage, wear, and
adjustment
-
1
Check brush pattern
-
1
Lubricate support rod
GL
1
O
6
Side brush(es)
Check for damage and wear
-
All
O
7
Hopper dust
fi
lter
Shake
-
1
O
8
Windshield washer
reservoir
Check
fl
uid level
WF
1
50
Hours
O
1
Engine
Check fuel lines and clamps for
tightness and wear
All
O
9
Tires
Check pressure
4
O
11
Cab
fi
lters
Clean
1
NOTE: Also check procedures indicted (**) after the fi rst 50-hours of operation, and procedures indicated
(**) after the fi rst 250 hours of operation.
LUBRICANT/FLUID
UTF Universal
tractor
fl
uid (Mobil
fl
uid 424) (TENNANT part no. 767766)
EO
Engine oil, API diesel classi
fi
cation 5W-40, CK-4, full synthetic
DEF Blue
DEF
fl
uid or equivalent API registered
fl
uid, per ISO 22241-1
HYDO
TennantTrue
premium hydraulic
fl
uid or equivalent
WBG Waterproof bearing grease (TENNANT part no. 765819)
WG
Distilled water, coolant conditioner (TENNANT part no. 770172) and permanent-type ethylene
glycol
anti-freeze,
−
34° C (
−
30° F)
WF
Automotive-type windshield washer
fl
uid
GL
SAE 90 weight gear lubricant (Grade GL5)
NOTE: More frequent intervals may be required in extremely dusty conditions.
Summary of Contents for sentinel
Page 99: ...99 Sentinel 9018524 05 2019 TROUBLESHOOTING MAIN WIRE HARNESS DIAGRAM ...
Page 100: ...100 Sentinel 9018524 05 2019 TROUBLESHOOTING MAIN WIRE HARNESS DIAGRAM ...
Page 101: ...101 Sentinel 9018524 05 2019 TROUBLESHOOTING MAIN WIRE HARNESS DIAGRAM ...
Page 102: ...102 Sentinel 9018524 05 2019 TROUBLESHOOTING MAIN WIRE HARNESS DIAGRAM ...
Page 103: ...103 Sentinel 9018524 05 2019 TROUBLESHOOTING MAIN WIRE HARNESS DIAGRAM ...
Page 104: ...104 Sentinel 9018524 05 2019 TROUBLESHOOTING MAIN WIRE HARNESS DIAGRAM ...
Page 105: ...105 Sentinel 9018524 05 2019 TROUBLESHOOTING MAIN WIRE HARNESS DIAGRAM ...
Page 106: ...106 Sentinel 9018524 05 2019 TROUBLESHOOTING MAIN WIRE HARNESS DIAGRAM ...
Page 107: ...107 Sentinel 9018524 05 2019 TROUBLESHOOTING MAIN WIRE HARNESS DIAGRAM ...
Page 108: ...108 Sentinel 9018524 05 2019 TROUBLESHOOTING MAIN WIRE HARNESS DIAGRAM ...
Page 109: ...109 Sentinel 9018524 05 2019 TROUBLESHOOTING MAIN WIRE HARNESS DIAGRAM ...
Page 110: ...110 Sentinel 9018524 05 2019 TROUBLESHOOTING MAIN WIRE HARNESS DIAGRAM ...
Page 111: ...111 Sentinel 9018524 05 2019 TROUBLESHOOTING MAIN WIRE HARNESS DIAGRAM ...
Page 112: ...112 Sentinel 9018524 05 2019 TROUBLESHOOTING MAIN WIRE HARNESS DIAGRAM ...
Page 113: ...113 Sentinel 9018524 05 2019 TROUBLESHOOTING MAIN WIRE HARNESS NOTES ...
Page 114: ...114 Sentinel 9018524 05 2019 TROUBLESHOOTING MAIN WIRE HARNESS NOTES ...
Page 115: ...115 Sentinel 9018524 05 2019 TROUBLESHOOTING MAIN WIRE HARNESS NOTES ...
Page 116: ...116 Sentinel 9018524 05 2019 TROUBLESHOOTING CAB WIRE HARNESS DIAGRAM ...
Page 117: ...117 Sentinel 9018524 05 2019 TROUBLESHOOTING CAB WIRE HARNESS DIAGRAM ...
Page 118: ...118 Sentinel 9018524 05 2019 TROUBLESHOOTING CAB WIRE HARNESS NOTES ...
Page 119: ...119 Sentinel 9018524 05 2019 TROUBLESHOOTING HOPPER WIRE HARNESS DIAGRAM ...
Page 120: ...120 Sentinel 9018524 05 2019 TROUBLESHOOTING HOPPER WIRE HARNESS DIAGRAM ...
Page 121: ...121 Sentinel 9018524 05 2019 TROUBLESHOOTING HOPPER WIRE HARNESS NOTES ...
Page 122: ...122 Sentinel 9018524 05 2019 TROUBLESHOOTING VARIO BRUSH HARNESS DIAGRAM OPTION ...
Page 123: ...123 Sentinel 9018524 05 2019 TROUBLESHOOTING VARIO BRUSH HARNESS DIAGRAM OPTION ...
Page 124: ...124 Sentinel 9018524 05 2019 TROUBLESHOOTING VARIO BRUSH HARNESS DIAGRAM OPTION ...
Page 126: ...126 Sentinel 9018524 05 2019 TROUBLESHOOTING ELECTRICAL SCHEMATIC PAGE 1 356858 1076547 1 2 3 ...
Page 132: ...132 Sentinel 9018524 05 2019 TROUBLESHOOTING ELECTRICAL SCHEMATIC PAGE 7 1 2 3 ...
Page 133: ...133 Sentinel 9018524 05 2019 TROUBLESHOOTING ELECTRICAL SCHEMATIC PAGE 8 1 2 3 1 4 5 6 ...
Page 134: ...134 Sentinel 9018524 05 2019 TROUBLESHOOTING ELECTRICAL SCHEMATIC PAGE 9 1 4 5 6 ...
Page 135: ...135 Sentinel 9018524 05 2019 TROUBLESHOOTING ELECTRICAL SCHEMATIC PAGE 10 2 3 4 5 6 7 8 1 ...
Page 136: ...136 Sentinel 9018524 05 2019 TROUBLESHOOTING ELECTRICAL SCHEMATIC PAGE 11 2 3 4 5 6 7 8 1 ...
Page 138: ...138 Sentinel 9018524 05 2019 TROUBLESHOOTING ...
Page 141: ...141 Sentinel 9018524 05 2019 TROUBLESHOOTING ...
Page 170: ...170 Sentinel 9018524 05 2019 TROUBLESHOOTING HYDRAULIC SCHEMATIC PAGE 1 6 5 4 3 2 1 1058282 ...
Page 172: ...172 Sentinel 9018524 05 2019 TROUBLESHOOTING HYDRAULIC SCHEMATIC PAGE 3 1058282 1 2 3 4 5 6 ...
Page 173: ...173 Sentinel 9018524 05 2019 TROUBLESHOOTING HYDRAULIC SCHEMATIC PAGE 4 ...
Page 174: ...174 Sentinel 9018524 05 2019 TROUBLESHOOTING HYDRAULIC SCHEMATIC PAGE 5 1058282 ...