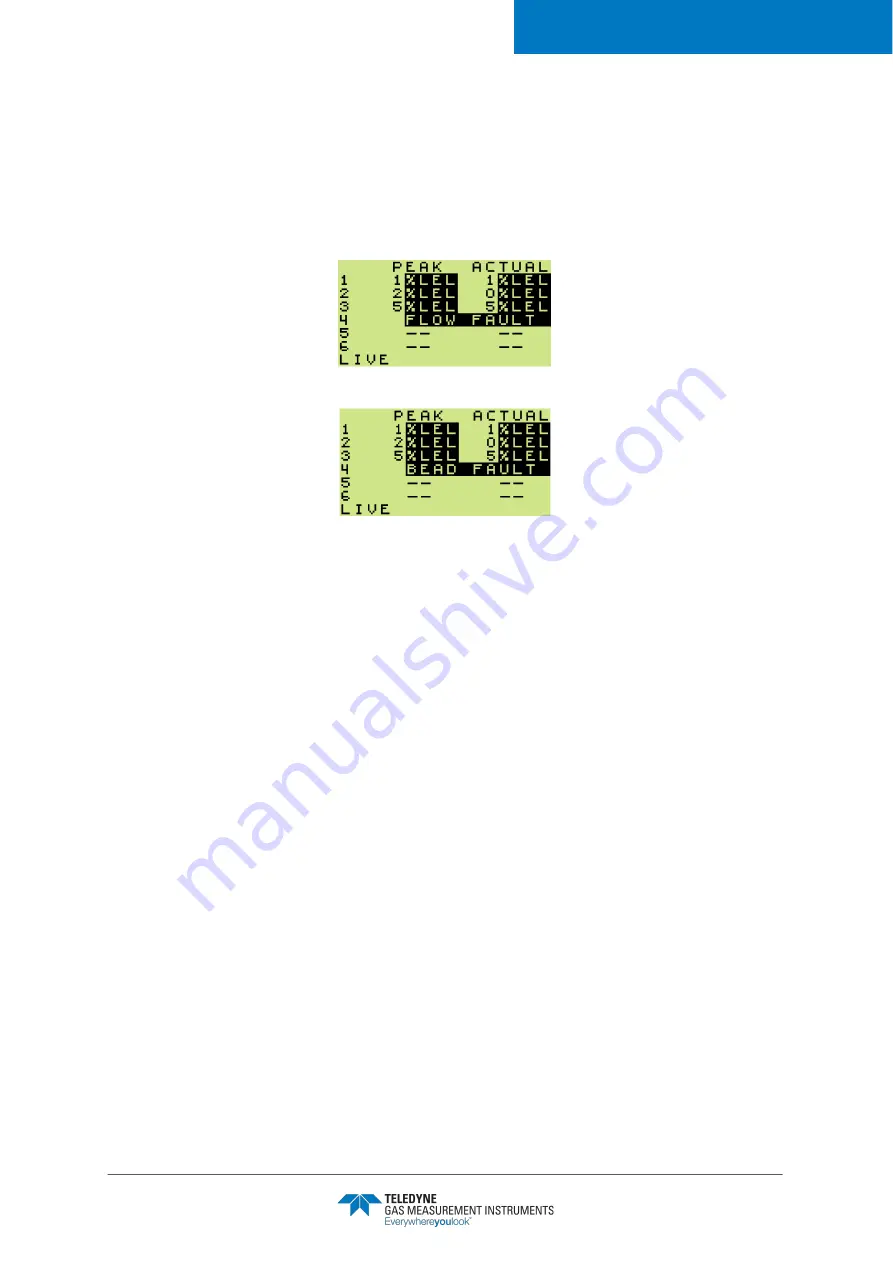
GT SERIES
1 INSTRUMENT, 7 APPLICATIONS
22
67112
Revision 10
4.3.6. Barhole Faults
If a Flow Fault or Bead Fault is detected, the pump stops automatically. Sampling is aborted if in
progress. A Purge cycle will commence.
Flow Fault or Bead Fault are recorded as shown in
and
.
Figure 31: Flow Fault
Figure 32: Bead Fault
4.4. Carbon Monoxide (CO) Mode
The CO mode is used to check the interior of premises and appliances for CO leakage.
4.4.1. Available Ranges
• 0 - 25% Oxygen (O
2
)
if fitted
• 0 - 2000 ppm Carbon Monoxide (CO)
4.4.2. Features
Carbon Monoxide mode features:
• Four display options:
– CO Direct
– Differential
– Air Free
– CO Viewing
• Pump ON / OFF
• Automatic & Manual Datalogging
• Invert Display
• Backlight
• Flashlight