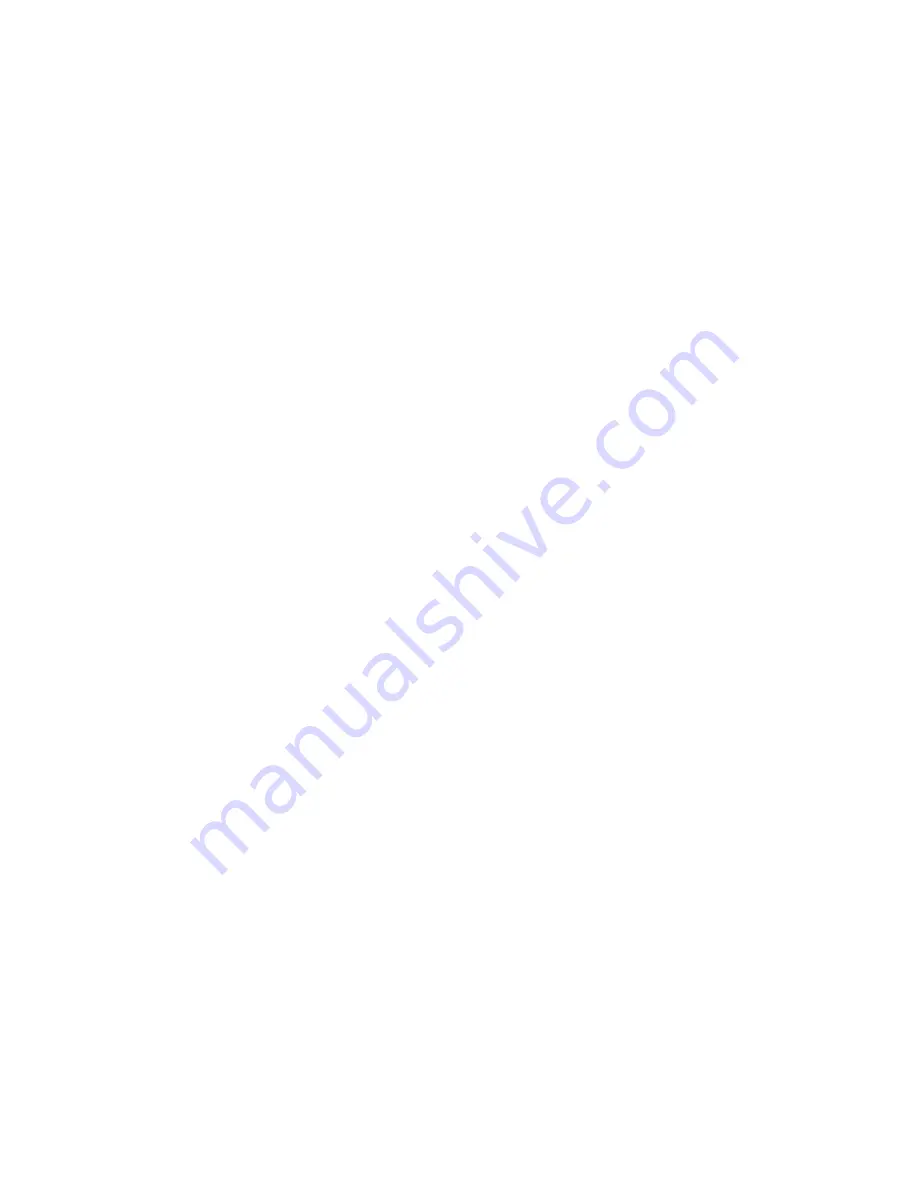
Teledyne API Model 300M CO Analyzer Instruction Manual, 04033, Rev. A
TABLE OF CONTENTS
SAFETY MESSAGES .........................................................................................II
TABLE OF CONTENTS .....................................................................................III
LIST OF FIGURES ........................................................................................... VII
LIST OF TABLES............................................................................................ VIII
1 INTRODUCTION .......................................................................................... 1-1
1.1 P
REFACE
.......................................................................................................................1-1
1.2 W
ARRANTY
....................................................................................................................1-1
1.3 P
RINCIPLE OF
O
PERATION
...............................................................................................1-3
1.4 S
PECIFICATIONS
.............................................................................................................1-5
1.5 I
NSTALLATION AND
O
VERVIEW
.........................................................................................1-6
1.6 E
LECTRICAL AND
P
NEUMATIC
C
ONNECTIONS
..................................................................1-11
1.6.1 Electrical Connections .........................................................................................1-11
1.6.2 Remote Contact Closures Zero/Span Inputs .......................................................1-11
1.6.3 Status Outputs (Optional) ....................................................................................1-11
1.6.4 RS-232 ................................................................................................................1-12
1.6.5 Pneumatic System...............................................................................................1-12
1.6.6 Sample Gas Connection......................................................................................1-13
1.6.7 Zero/Span Valve Connections .............................................................................1-13
1.6.8 Exhaust Connections...........................................................................................1-13
1.7 O
PERATION
V
ERIFICATION
.............................................................................................1-15
1.8 O
PTIONS
......................................................................................................................1-17
1.8.1 Rack Mount With Slides ......................................................................................1-17
1.8.2 Span Valve ..........................................................................................................1-17
2 OPERATION ................................................................................................ 2-1
2.1 K
EY
F
EATURES
...............................................................................................................2-1
2.1.1 CO Readout...........................................................................................................2-1
2.1.2 CO Analog Output .................................................................................................2-1
2.1.3 E
2
ROM Backup Of Software Configuration ...........................................................2-1
2.1.4 Adaptive Filter........................................................................................................2-1
2.1.5 Data Acquisition (DAS)..........................................................................................2-2
2.1.6 RS-232 Interface ...................................................................................................2-2
2.1.7 Password Protection..............................................................................................2-2
2.2 F
RONT
P
ANEL
................................................................................................................2-3
2.2.1 Front Panel Display ...............................................................................................2-3
2.2.2 Programmable Push Buttons.................................................................................2-7
2.2.3 Status LED’s..........................................................................................................2-8
iii
Summary of Contents for 300M
Page 26: ...Teledyne API Model 300M CO Analyzer Instruction Manual 04033 Rev A INTENTIONALLY BLANK 1 18 ...
Page 36: ...Teledyne API Model 300M CO Analyzer Instruction Manual 04033 Rev A INTENTIONALLY BLANK 2 10 ...
Page 56: ...Teledyne API Model 300M CO Analyzer Instruction Manual 04033 Rev A INTENTIONALLY BLANK 4 10 ...
Page 64: ...Teledyne API Model 300M CO Analyzer Instruction Manual 04033 Rev A INTENTIONALLY BLANK 5 8 ...
Page 66: ...Teledyne API Model 300M CO Analyzer Instruction Manual 04033 Rev A INTENTIONALLY BLANK 6 2 ...
Page 86: ...Teledyne API Model 300M CO Analyzer Instruction Manual 04033 Rev A INTENTIONALLY BLANK 8 8 ...
Page 94: ...Teledyne API Model 300M CO Analyzer Instruction Manual 04033 Rev A INTENTIONALLY BLANK 9 8 ...
Page 116: ...Teledyne API Model 300M CO Analyzer Instruction Manual 04033 Rev A INTENTIONALLY BLANK 11 4 ...