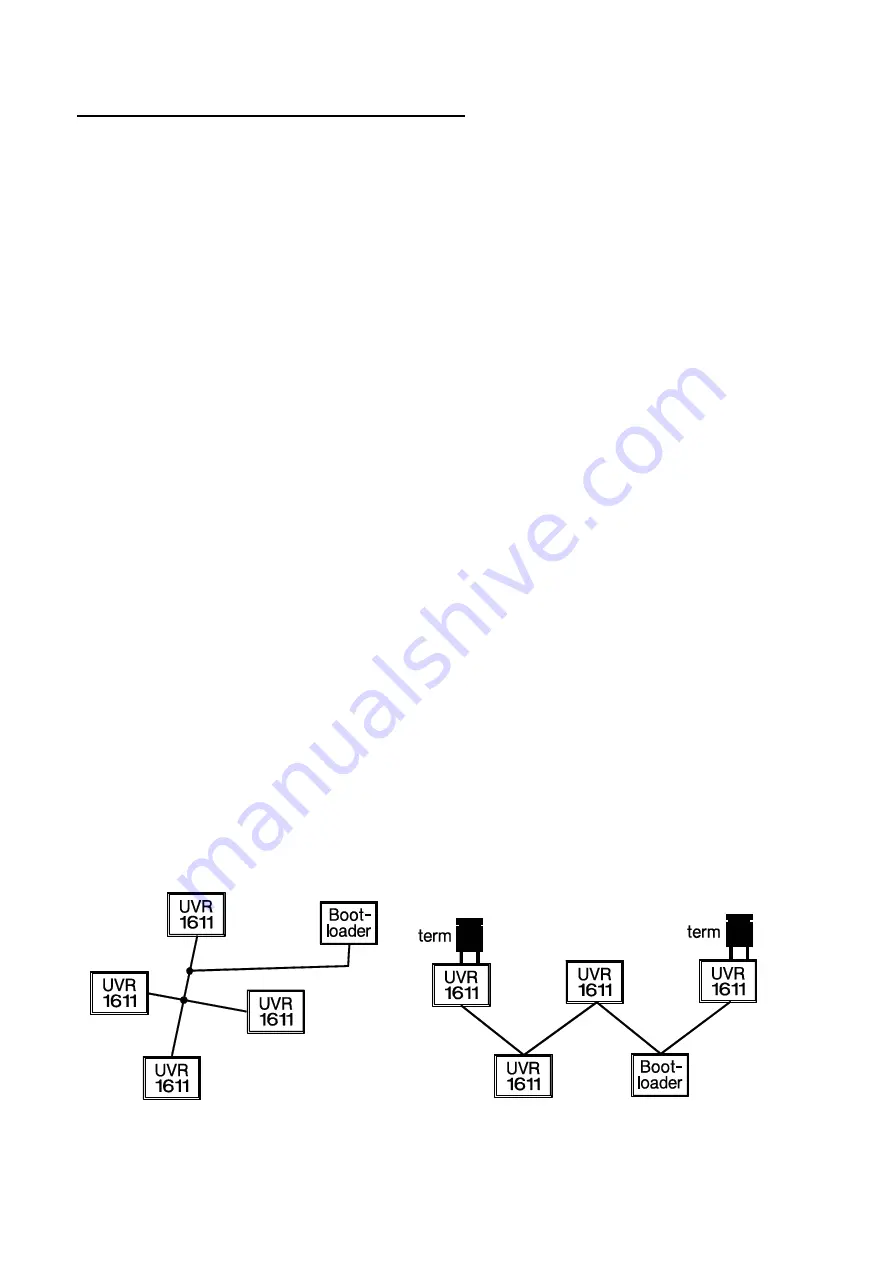
CAN bus and IR-CAN infrared interface
The IR-CAN interface (infrared CAN) offers a simple way of transferring functional data. It is
located under the two buttons of the UVR1611 and on the lower side of the bootloader case.
During the data transfer, the bootloader must lie in the correct position on the controller:
Bootloader – upper edge = Controller display – lower edge, the sideways position of the
display is marked on the bootloader.
For transferring the functional data the controller must be prepared via the
"Datenverwaltung"
("data administration")
menu. This is only permitted in expert mode. The controller switches to
data transfer mode when the "
Upload
bzw.
Download wirklich starten?
" ("
Really start upload
or
download?
") query is confirmed. After this, the bootloader is placed in the correct position
on the controller (at the lower edge of the display and between the markings). As with the
CAN cable, the data transfer is started by pressing the Start button on the bootloader. The
green LED flashes during the transfer and the functional data takes about 15 seconds to
transfer.
Since an operating system can take about 5 minutes to transfer, this should always be
done via a CAN bus cable connection
. If the loading of the operating system is interrupted
then a renewed transfer is only possible via a cable connection!
In addition to data transfer, the ethernet interface of the CAN bus also allows direct access to
the CAN network devices via a browser on the PC. Both LEDs flash briefly when the CAN
cable is plugged in and after about 20 seconds, the green LED lights up to indicate that the
BL-NET is ready to operate on the CAN bus.
When using the CAN bus to connect several devices with a total cable length above 5 m,
correct termination of the bus is important. The network
terminators
must be connected at
the
cable ends
. The lower side of every controller, and the bootloader, have a corresponding
jumper bridge (
term
) for this. A CAN bus must never be connected from a node (terminal) to
other devices in a star formation. The correct layout is a series cable from the first device
(with terminator) to the second device, then the third, etc., and the last bus connection must
also have a termination jumper.
Additional information on the correct layout of a CAN bus network (e.g.: cable selection, etc.)
is provided in the UVR1611 controller handbook.
Wrong
Right
6