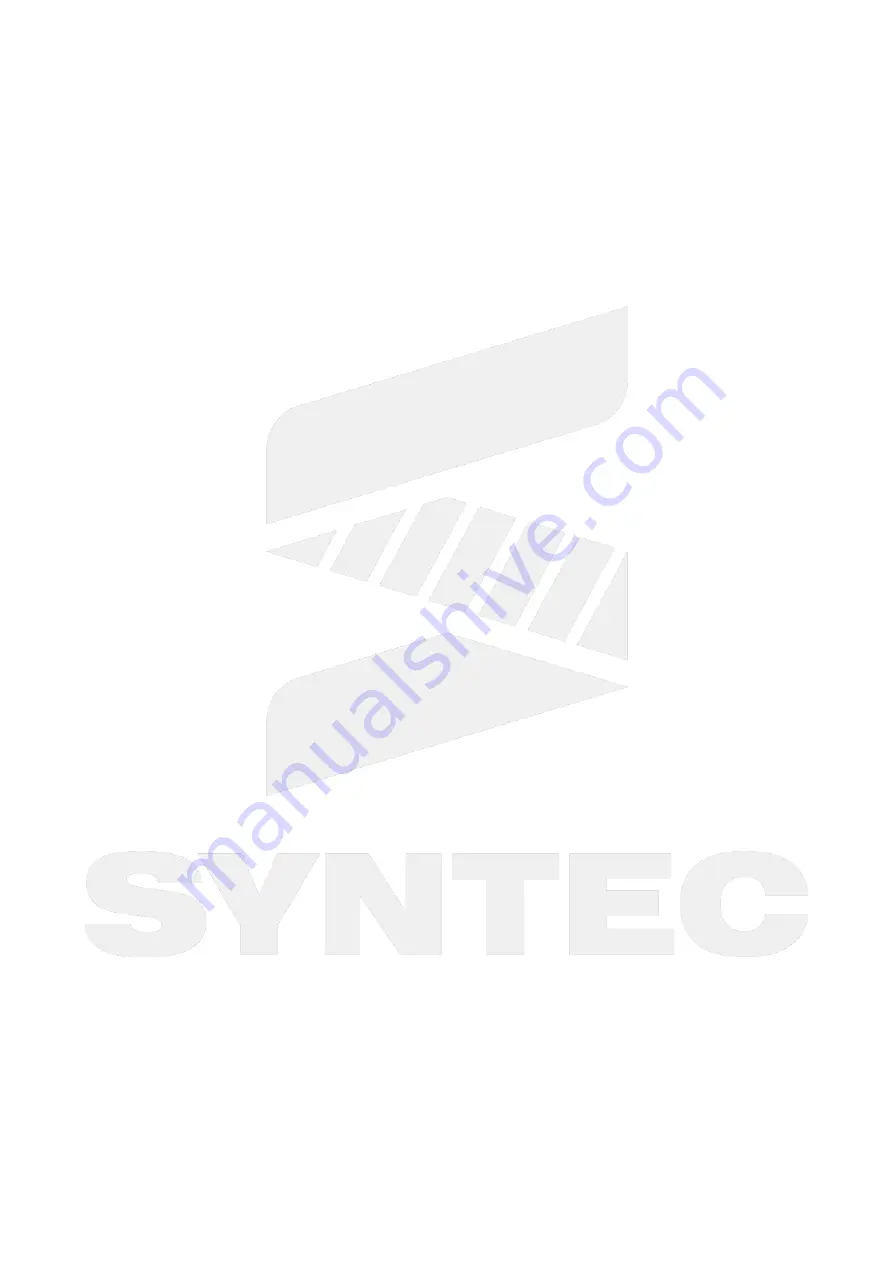
伺服產品
/Servo Products
–
Hardware Manual of 30kW Servo Drive II (SPD-32B1-300)
Wiring and Signal
–
20
5.6.2
Detailed Selection Guide for Regeneration Resistors
Motors do Negative Work under External Torque Load
Motors generally do positive work while operating, but they may do negative work when the output torque
direction is opposite of the rotation direction. For instance, the motor may output torque to resist the inertia during
braking, or it may experience an external torque load while in torque mode...etc. During those times, the external
force is doing positive work through the motor and transferring that energy to the drive; that is, the motor acts as a
generator. When this happens, the regenerative resistor must quickly dissipate the energy in order to prevent
flooding the DC terminal voltage.
Suppose the external torque load is T
L
and the unit is a percentage of the rated torque (%). The speed at that
instance in time is Wr (rpm). The regenerative resistance power must be greater than the External Torque Power =
T
L
x Rated Torque x (Wr x 2
π
/60).
For example, if the external torque is 50% of rated torque, the speed is 2000 (rpm), and the motor rated torque is
2 (Nm), then the external torque produces a power of 0.5 * 2 * 2000 * 2
π
/ 60
≈
210 W. To be safe, that number is
usually multiplied by a safety factor of around 2 ~ 3, therefore the user needs to select a regenerative resistor of
more than 420W.
Free of External Torque Load
Assuming that the motor moves back and forth, the energy generated by the inertial force during braking will be
poured back into the drive. At this time, the capacitor of the DC bus terminal of the drive is the first buffer to absorb
and reuse the energy. However, the absorption of energy by the capacitor causes the DC bus voltage to rise, so
when the voltage rises to a certain level, the second buffered regenerative resistor is turned on to convert the
energy into heat and discharge it.
The calculation method of the regenerative energy generated by the spindle motor of the drive during braking is
provided below, and the user can calculate the required resistance according to different occasions.
E
0
in the table below is the regenerative energy required to dissipate from the rated speed to the standstill when
the motor is load-free, E
0
=J*
ω
r
2
/182, where J is the rotor inertia (kg-m
2
) and
ω
r is the rated speed of the motor
( Rpm). And Ec is the energy that the DC bus capacitor can absorb, Ec = C*(V
b,max
2
-V
b
2
)/2, where C is the capacitance
value of the DC bus terminal. V
b,max
is the maximum voltage that the DC bus can withstand, the 220V drive can
withstand 400 V, and the 380V drive can withstand 800 V. The V
b
value is the rated voltage of the DC bus, and the
value is 2 times the root of the input supply voltage.
Considering the actual application, assume that the load inertia ratio is N times the motor inertia. If the speed is
braked from the rated M times to zero speed, the regenerative resistor must consume
E
0
(N+1)*M
2
-Ec
Joule. If the
motor reciprocating cycle (Time of accelerating, being steady, to decelerating) is T sec, then the regenerative
resistor power W =
1.2
[E
0
*(N+1)*M
2
-Ec]/T, 1.2 is the safety factor.
In addition, according to the application of the spindle cover, the allowable frequency index is provided for the
user to select. The allowable frequency is defined as the continuous acceleration and deceleration of the motor. In
the case where the regenerative resistor and the motor are not overheated, the maximum number of round trips
per minute is equal to 60 seconds divided by the round trip period T, i.e. 60/T. For example, when the milling
machine is performing drilling and tapping, the spindle will frequently perform acceleration and deceleration
(single drilling involves two acceleration and deceleration actions). If it is desired that the regenerative resistor is
not prone to overheating and smoke, the number of drilling per minute must be limited to less than half of the
allowable frequency.