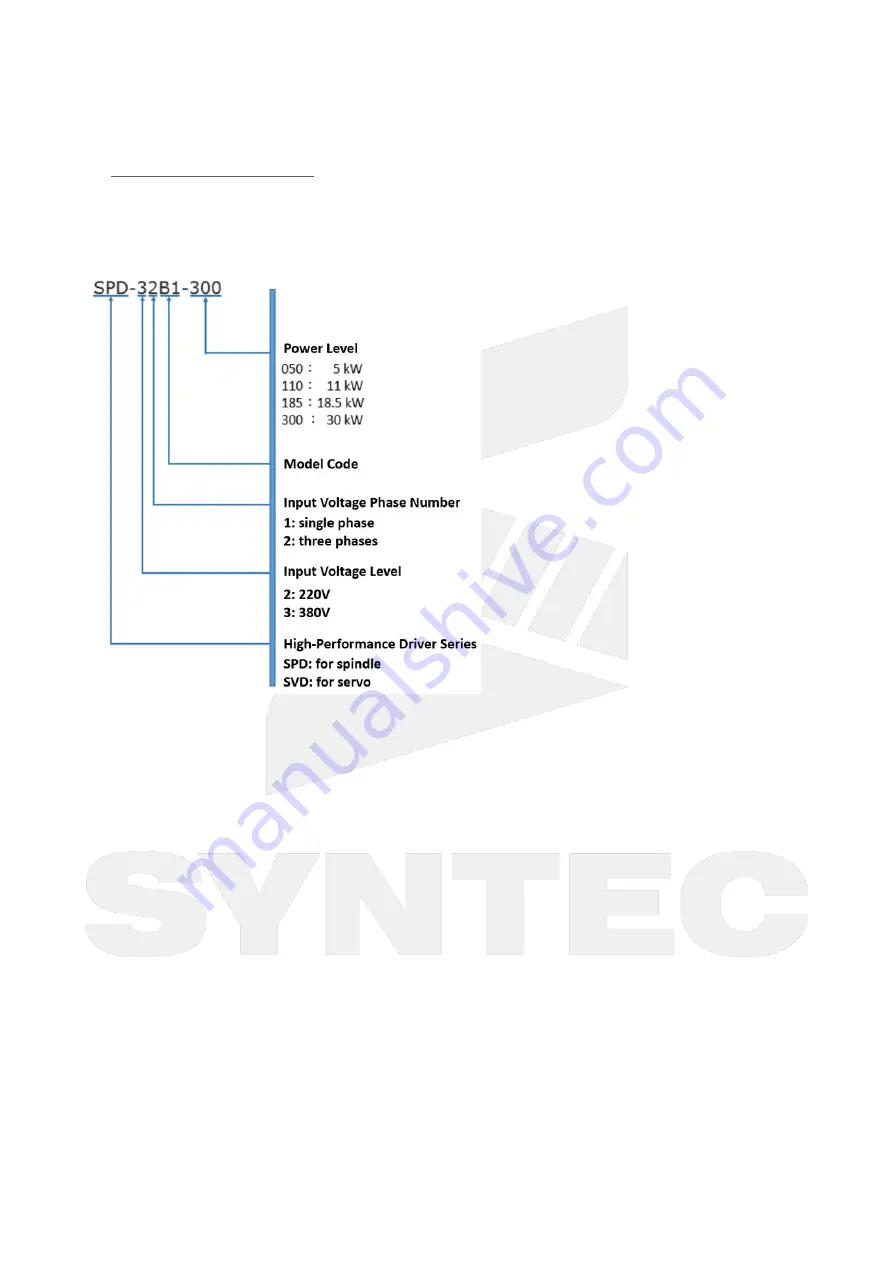
伺服產品
/Servo Products
–
Hardware Manual of 30kW Servo Drive II (SPD-32B1-300)
Wiring and Signal
–
11
•
•
•
1.
2.
1.
2.
3.
5
Wiring and Signal
5.1
Wiring Diagram
SPD-32B1-300
Installation Precautions:
Before powering on, check if the U, V, W, and G terminals are correctly wired to the motor. An incorrect
UVW sequence may lead to rotation in the reverse direction or even motor malfunction; at that point,
Encoder Testing and Magnetic Pole Offset Detection must be re-performed. An incorrect G wiring may
cause damage to the motor or the drive.
It is recommended to provide the power supply of the controller through any two terminals of the RST.
When wiring the host controller, select either general servo signal or serial servo signal-- not both.
Wiring Instructions
Power supply:
Input power from R, S, T, L1, L2
L1 and L2 are optional
Encoder Terminals:
Single-axis Axial Type (SVD) has one set of encoder feedback (6PIN) and Spindle Type (SPD) has two sets of
encoder feedback (6PIN); each set of encoder terminals has a 5V power output (up to 150mA).
Supports encoder interface of Tamagawa, SYNTEC, and NIKON.
Battery voltage checking for absolute encoders.