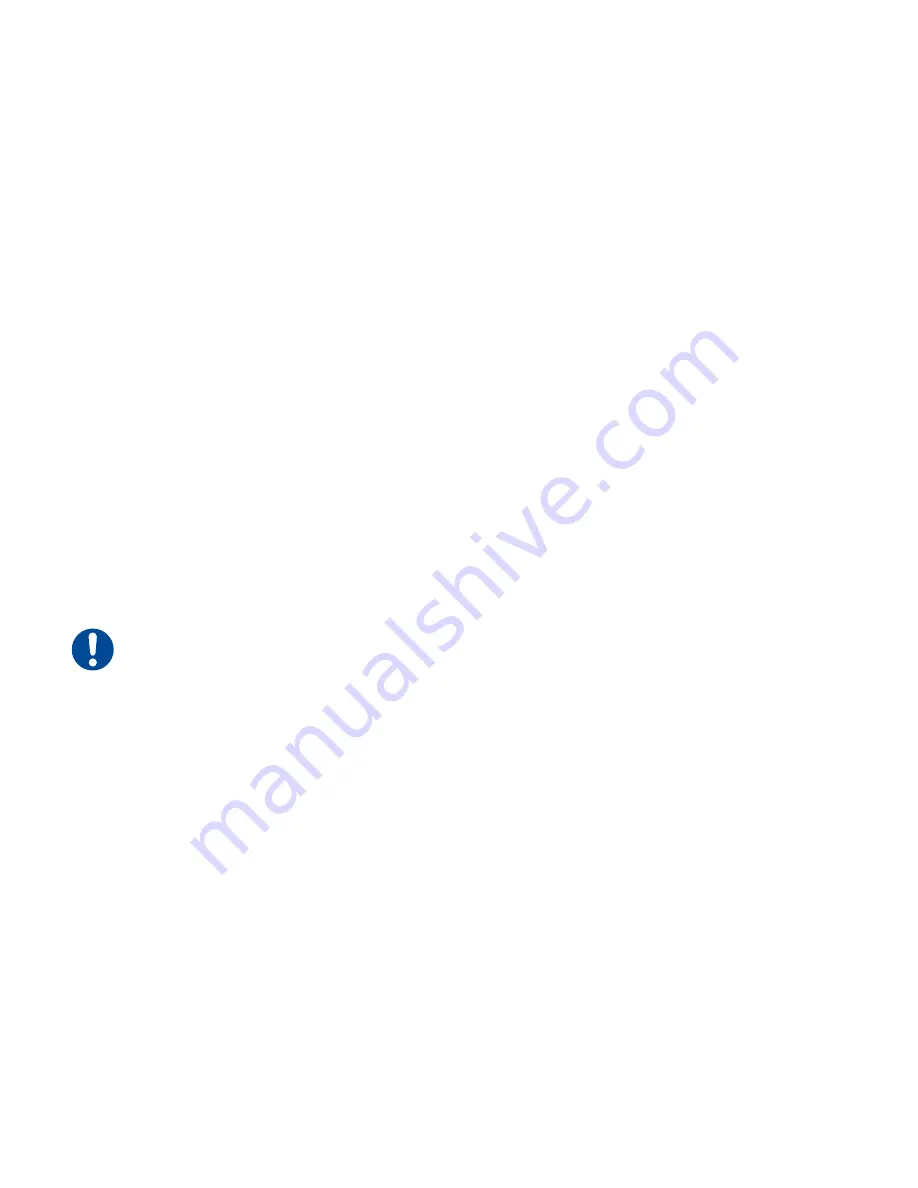
SHUTTER FUNCTIONS
PAGE
|
71
Your control system can monitor the laser’s ready status on the User I/O connector by connecting your
system’s input between Pin 8, Laser Ready, and Pin 13, Output Common (see outputs driving PLC input
module figure in the prior pages of this chapter).
The Laser Ready output closes when the laser is enabled (RDY LED illuminated yellow), indicating that
lasing is possible. The output is open (in a high-impedance state) and the RDY LED is off when lasing is
disabled.
Shutter functions
A mechanical Shutter Switch is installed on all Keyswitch-equipped lasers. Lasing is enabled when the
shutter is Open (SHT LED illuminated blue) and disabled when the shutter is Closed (SHT LED off). The
SHT LED illuminates blue to indicate that DC power is applied to the RF driver.
For ti-Series OEM and Keyswitch-equipped lasers in automated systems, the shutter function is provided
by the Shutter Open Request signal via Pin 10 on the User I/O connector. To use this “remote shutter,”
first place the Shutter Switch (if equipped) in the Open position and then apply a voltage in the range of
±5–24 VDC to Pin 10, Shutter Open Request. This input signal causes the SHT LED to illuminate and
sends DC power to the RF driver, enabling lasing. On Keyswitch-equipped lasers, a five-second delay
occurs after the input is enabled. Lasing is disabled until the manual Shutter Switch is placed in the Open
position and a Shutter Open Request signal is applied to Pin 10.
Your control system can monitor the laser’s shutter status on the User I/O connector by connecting your
system’s input between Pin 14, Shutter Open, and Pin 13, Output Common (see the outputs driving PLC
input module earlier in this chapter). The Shutter Open output closes when the Shutter Switch is Open,
and a Shutter Open Request signal is present (SHT LED illuminated blue). The output is open (in a high-
impedance state) and the SHT LED is off when the manual Shutter Switch is Closed, or the Shutter Open
Request signal is removed.
Important Note: After the Shutter Open output closes, a five-second delay occurs (Keyswitch-
equipped lasers only) before lasing is enabled.
Remote interlock functions
Interlock circuits are often used to disable machinery when a shield, panel, or door is opened. Remote
interlock function allows you to connect into an external remote interlock circuit and prevent lasing by
removing DC power from the laser’s RF driver when the circuit is electrically “open.”
Lasing is enabled when a Remote Interlock signal is present (INT LED illuminated green), if RDY and SHT
LEDs are illuminated, and disabled when the Remote Interlock signal is removed (INT LED red, RDY LED
off). DC power is applied to the RF driver only when the INT LED is green and the RDY LED is yellow
(and the SHT LED is illuminated blue). Remote interlock functionality is provided by the Remote
Interlock input signal via Pin 3 on the User I/O connector.
To use the remote interlock feature, apply a voltage in the range of ±5–24 VDC to Pin 3, Remote
Interlock. Applying an interlock signal causes the INT LED to illuminate green and sends DC power to the
RF driver, which enables lasing (provided that the RDY LED is yellow and the SHT LED is blue). On
Keyswitch-equipped lasers, a five-second delay occurs after the input is enabled. Removing the interlock
signal removes DC power from the RF driver, causing the INT LED to turn red and the RDY LED to turn
off. Lasing remains disabled until a Remote Interlock signal is reapplied to Pin 3.
Your control system can monitor the laser’s remote interlock status on the User I/O connector by
connecting your system’s input between Pin 15, Interlock Open, and Pin 13, Output Common (see outputs
Summary of Contents for Novanta OEM ti Series
Page 1: ...ENGINEERED BY SYNRAD OEM ti Series User Manual...
Page 26: ...TI60 LABEL LOCATIONS PAGE 26 Ti60 label locations Figure 3 1 Ti60 hazard label locations...
Page 27: ...TI80 LABEL LOCATIONS PAGE 27 Ti80 label locations Figure 3 2 Ti80 hazard label locations...
Page 28: ...TI100 LABEL LOCATIONS PAGE 28 Ti100 label locations Figure 3 3 Ti100 hazard label locations...
Page 32: ...EUROPEAN UNION EU REQUIREMENTS PAGE 32 Table 3 1 Class 4 safety features...
Page 34: ...EUROPEAN UNION EU REQUIREMENTS PAGE 34 Figure 3 4 ti60 Declaration Document...
Page 35: ...EUROPEAN UNION EU REQUIREMENTS PAGE 35 Figure 3 5 ti80 Declaration document...
Page 36: ...EUROPEAN UNION EU REQUIREMENTS PAGE 36 Figure 3 6 ti00 Declaration document...
Page 55: ...INPUT SIGNALS PAGE 55 Table 4 5 Input signal table continued...
Page 65: ...DB 9 PIN DESCRIPTIONS PAGE 65 Table 4 9 Side mounted DB 9 pin descriptions continued...
Page 73: ...REMOTE INTERLOCK FUNCTIONS PAGE 73 Table 4 10 Ti60 general specifications continued...
Page 74: ...REMOTE INTERLOCK FUNCTIONS PAGE 74 Table 4 11 Ti80 general specifications...
Page 75: ...REMOTE INTERLOCK FUNCTIONS PAGE 75 Table 4 11 Ti80 general specifications continued...
Page 76: ...REMOTE INTERLOCK FUNCTIONS PAGE 76 Table 4 12 Ti100 general specifications...
Page 77: ...REMOTE INTERLOCK FUNCTIONS PAGE 77 Table 4 12 Ti100 general specifications continued...
Page 82: ...TECHNICAL DRAWINGS PAGE 82 Figure 4 29 Ti Series HS Outline and Mounting...
Page 83: ...TECHNICAL DRAWINGS PAGE 83 Figure 4 28 Ti 100p Outline and Mounting...
Page 84: ...TECHNICAL DRAWINGS PAGE 84 Figure 4 29 Ti 100 Fan Outline and Mounting...
Page 85: ...TECHNICAL DRAWINGS PAGE 85 Figure 4 30 ti Series packaging instructions...
Page 93: ...MAINTENANCE TROUBLESHOOTING PAGE 93 Table 4 14 Status Signals...
Page 99: ...MAINTENANCE TROUBLESHOOTING PAGE 99...
Page 105: ...APPENDIX PAGE 3 This page is intentionally left blank...