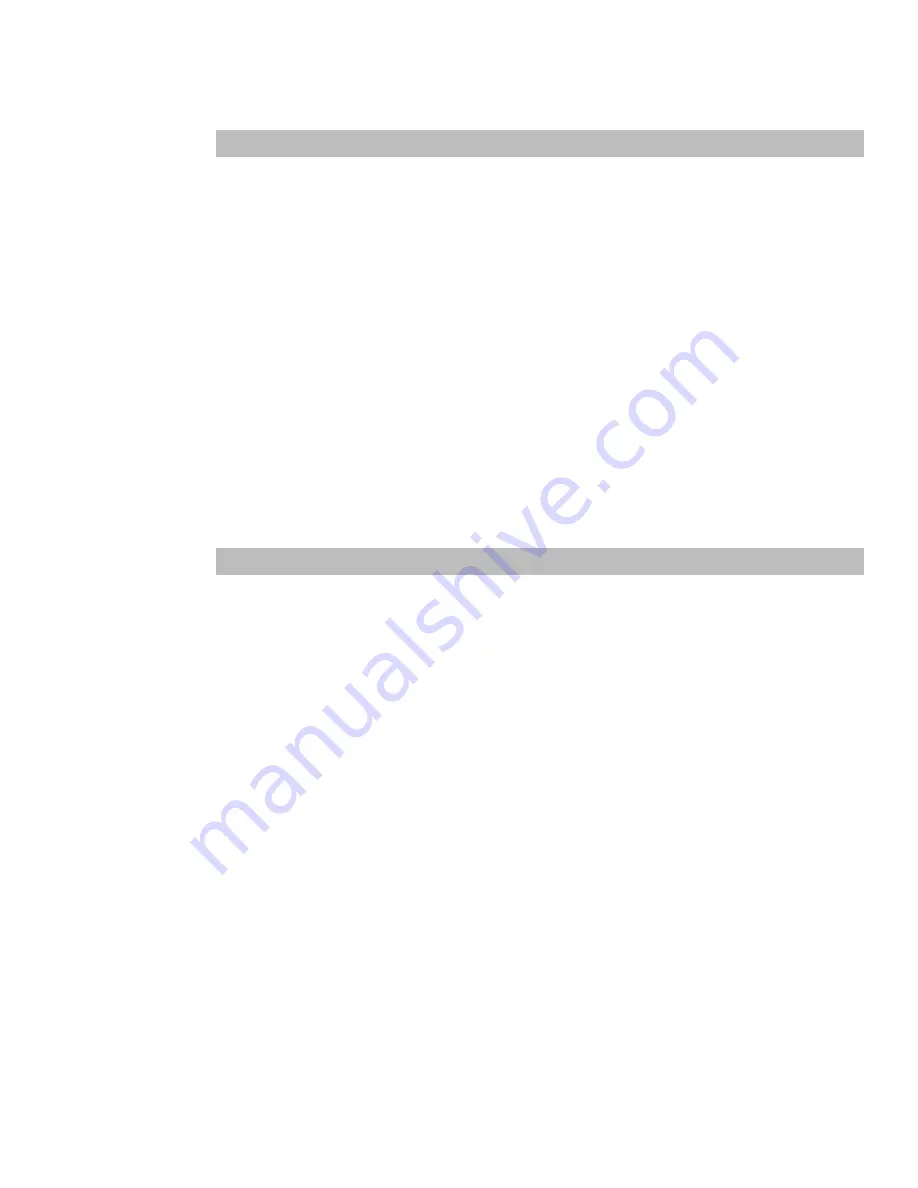
table of contents
v
Synrad FH Flyer Marking Head Operator’s Manual Version 3.4
Technical Reference
5
Tracking hardware ......................................................................................................4-9
Position encoder .............................................................................................................................
4-9
Part sensor .........................................................................................................................................
4-14
DC power supply ............................................................................................................................
4-18
WinMark Pro tracking setup ....................................................................................4-19
Determining line speed ............................................................................................4-24
Line speed formula ........................................................................................................................
4-24
Sample calculations .......................................................................................................................
4-24
Tracking optimization ................................................................................................4-26
Text ......................................................................................................................................................
4-26
Graphics .............................................................................................................................................
4-27
Mark placement ..............................................................................................................................
4-28
Line speed optimization ..............................................................................................................
4-28
Summary ...........................................................................................................................................
4-29
Tracking (cont.)
4
FH Flyer technical overview .....................................................................................5-3
Marking head ...................................................................................................................................
5-3
Beam expansion ..............................................................................................................................
5-3
Lens specifications .........................................................................................................................
5-4
Input/Output circuitry ..............................................................................................5-5
User Interface overview ...............................................................................................................
5-5
In15 VDC supply ..............................................................................................................
5-7
Digital input circuitry ....................................................................................................................
5-7
Digital output circuitry .................................................................................................................
5-14
FH Index/Tracker to Flyer conversion ......................................................................................
5-18
FH Smart to Flyer conversion .....................................................................................................
5-21
USB port ..........................................................................................................................5-25
USB connections .............................................................................................................................
5-25
Electrical isolation/electrical noise ...........................................................................................
5-25
Ethernet port ................................................................................................................5-26
Ethernet overview ..........................................................................................................................
5-26
Ethernet port LEDs .........................................................................................................................
5-26
Ethernet/Flyer cabling ..................................................................................................................
5-26
Fast Acting Safety Interlock .....................................................................................5-29
Flyer web interface .....................................................................................................5-31
Summary of Contents for FH FLYER
Page 146: ...SYNRAD FH Series Flyer Operator s Manual Version 3 4 116 This page intentionally left blank...
Page 206: ...SYNRAD FH Series Flyer Operator s Manual Version 3 4 176 This page intentionally left blank...
Page 224: ...222 SYNRAD FH Series Flyer Operator s Manual Version 3 4 This page intentionally left blank...