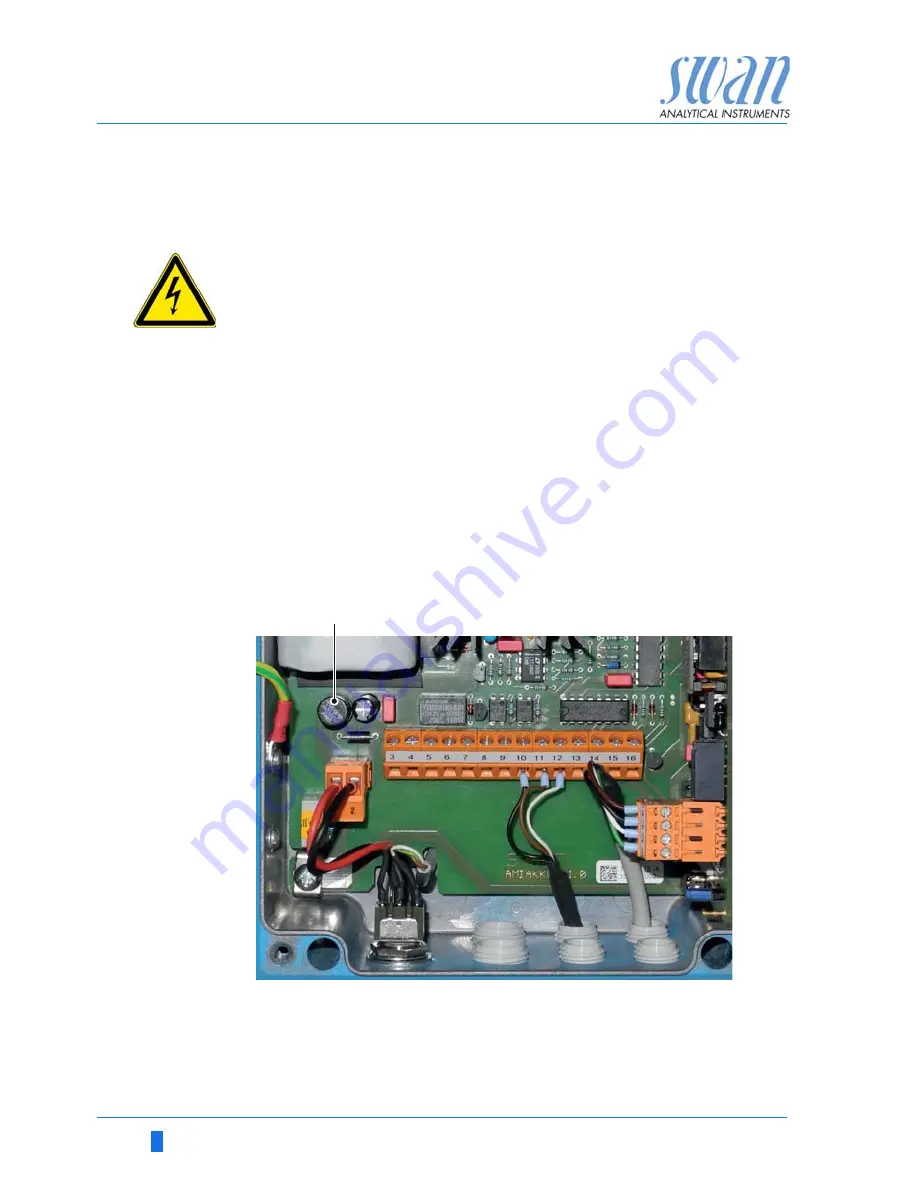
38
A-96.250.741 / 050218
AMI INSPECTOR Hydrogen
Maintenance
6.5.
Replacing Fuses
WARNING
External Voltage.
External supplied devices connected to relay 1 or 2 or to the
alarm relay can cause electrical shocks.
Make sure that the devices connected to the following con-
tacts are disconnected from the power before continuing the
installation.
– relay 1
– relay 2
– alarm relay
Find and repair the cause for the short circuit before replacing the
fuse. Use tweezers or needle-nosed pliers to remove the defective
fuse.
Use original fuses provided by SWAN only.
A
1.25 AF/250V Instrument power supply
A