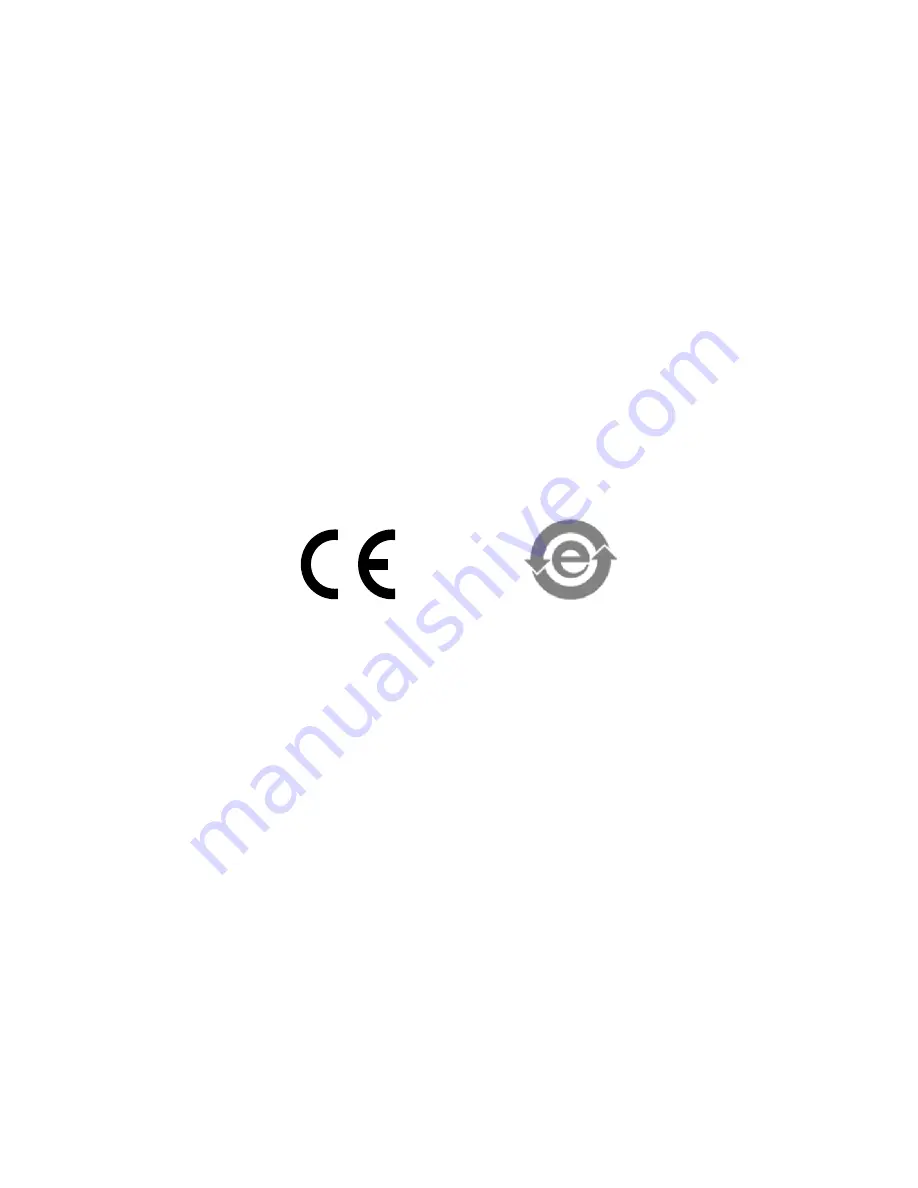
TRIO MPC-165 SERIES MICROMANIPULATOR SYSTEM OPERATION MANUAL – REV. 2.67K2 (20201130) (FW V2.62)
2
(The picture on the cover page shows a TRIO MPC-100 ROE/controller and two TRIO MP-865M
micromanipulators (one right-handed and the other left-handed). The Sutter Instrument dPatch Headstages
shown mounted on the micromanipulators are not included in the TRIO MPC-165 Series system.)
Copyright © 2020 Sutter Instrument Company. All Rights Reserved.
TRIO™ is a trademark of Sutter Instrument Company.