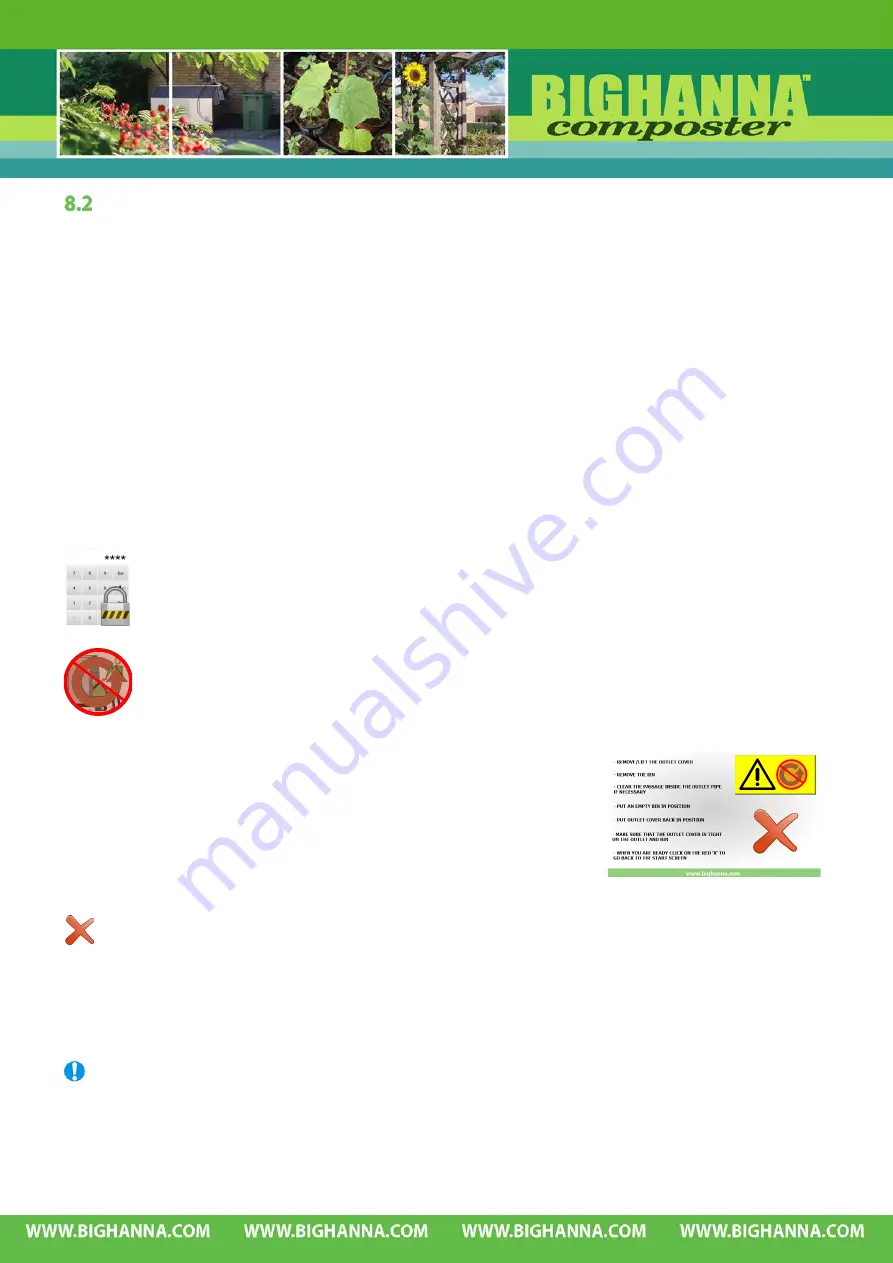
MAINTENANCE AND CLEANING MODEL T240
The recommendation is to perform a competent check-up daily under normal operation conditions,
which can be done when the food waste is fed into the machine together with sawdust or pelletised
sawdust. This does not take more than a few minutes checking the basic function of the composter,
the biological process and empty the compost bin if necessary.
8.2.1
CHECK-UP DAILY - T240
The daily operation of Big Hanna Composter includes feeding food waste and sawdust/wood pellets into
Big Hanna and clean up accidental spill when feeding food waste into Big Hanna. At the same time the
following should be checked:
⇒
WHEN FEEDING FOOD WASTE NOTE THAT CYLINDER MOTOR AND FAN IS WORKING
⇒
NOTE TEMPERATURE ON TOUCH SCREEN
If the temperature in the hot zone has dropped significantly check moisture, colour, smell, filling
level of material inside cylinder and airflow to and from cylinder. Add pellets/sawdust, empty
cylinder, clear ventilation and/or adjust settings accordingly.
⇒
EMPTY BAG OR BIN ON OUTLET IF NECESSARY
Press the ‘no emptying’ button. This button stops the cylinder from rotating while the
bag/bin is exchanged preventing spill on the floor beneath the outlet pipe.
Follow the instructions on the screen when changing the bin:
Remove the outlet cover (if appl.)
Remove the bin/bag
Clear the passage inside the outlet pipe if necessary
Put an empty bin/bag in position
Put outlet cover back in position (if appl.)
Make sure the outlet cover/bag is tight on the outlet
When you are ready click on the red ‘X’ to go back to the start
screen
The red exit ‘X’ symbol must be pressed in order to return to the start screen so that the cylinder
can rotate according to settings again.
It is important to return to the start screen once the bag/bin is exchanged making it possible for
the cylinder to run according to settings.
Note! The function of stopping the cylinder from rotating while the bag/bin is exchanged is in no
way connected to the safety system.
LOCKOUT / TAGOUT BEFORE REMOVING BOLTED COVERS.
When changing the bin a small portion of already processed compost material should be recycled, fed
in through the in-feed hopper in order to support the biological process.
Press the numeric key pad, enter the
pin code and access ‘basic’ level.
Summary of Contents for BIGHANNA T120
Page 8: ......
Page 28: ......
Page 32: ......
Page 80: ...5 3 1 START UP SCHEDULE MODEL T60 RESTAURANT WASTE...
Page 81: ......
Page 82: ...5 3 2 START UP SCHEDULE MODEL T120 RESTAURANT WASTE...
Page 83: ......
Page 84: ...5 3 3 START UP SCHEDULE MODEL T240 RESTAURANT WASTE...
Page 85: ......
Page 86: ......
Page 94: ......
Page 114: ......