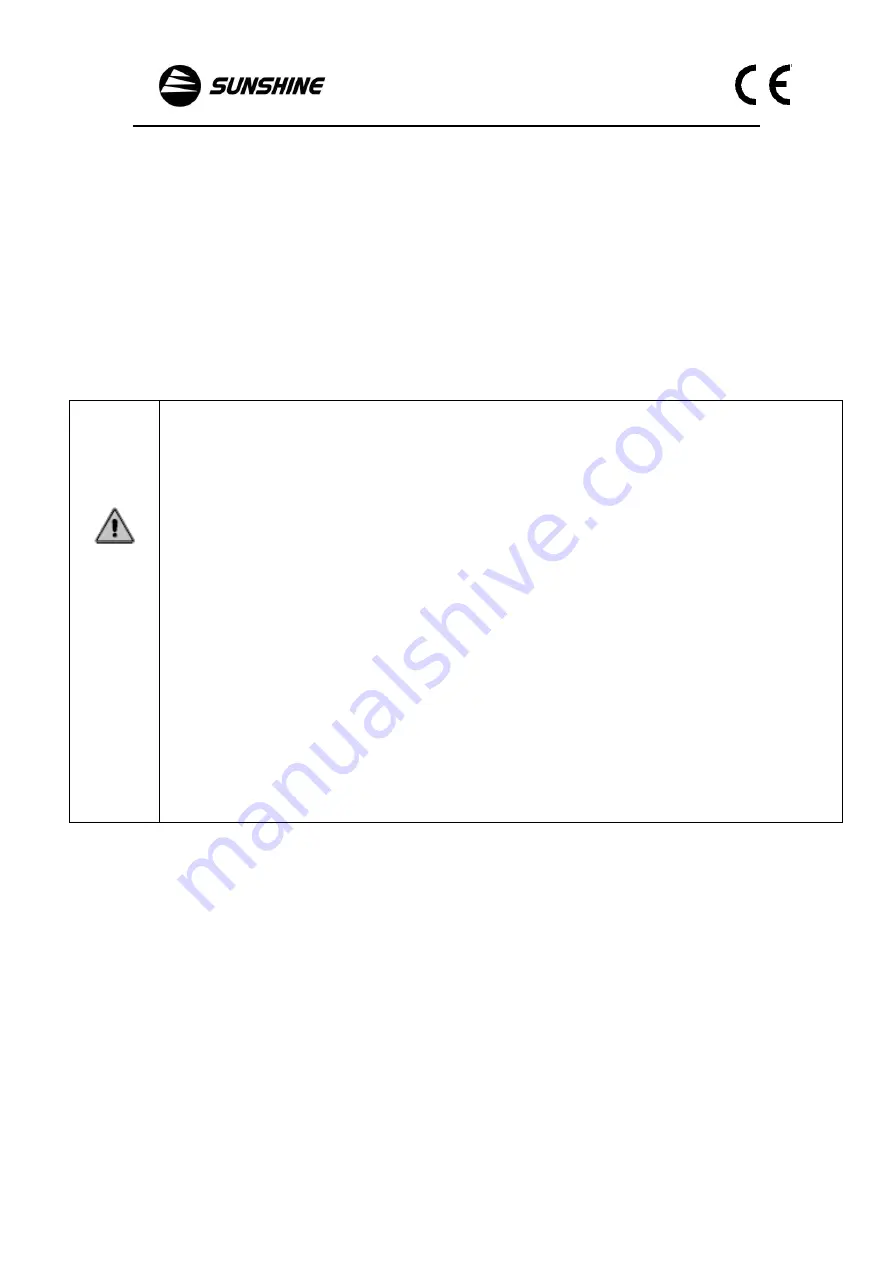
34
slider are the same, or should be adjusted two ends of the curtain rope slider height until
they are the same; two sliding Height Maximum tolerance is 5 mm.
4
、
In the trial run of the process, should observe the vibration, noise of lift , whether
the oil leak, pump motor functioning, the implementation of electrical components etc..
5
、
Do 2-3 times the full load test, simultaneous detection of item 3,4,if there's no problem, just do
repair work
1
、
Operate strictly in accordance with operating procedures, don't operate lift casually
2
、
Make sure center of gravity as close as possible to the panel made by two poles. because
center of gravity is different from cars during lifting.
3
、
The motor reverse is prohibited to avoid damage to the pump during initial installation
4
、
A comprehensive inspection is needed every half month especially whether three
expansion bolts behind pole panel is loose
5
、
Hydraulic oil must be a regular manufacturers of high pressure anti-wear hydraulic oil.
6
、
Observe the oil level frequently to avoid starvation and damage caused by oil pump idle.
7
、
Always check the working status of mechanical safety lock to make it safe and reliable.
8
、
Hydraulic valve, system pressure has been adjusted at the factory, the user can not adjust
is casually and should be responsible for the consequences.
9
、
Repair work, the mechanical safety lock must be effective working state.
Chapter V Maintenance
5.1 Maintenance
Car lift maintenance should pay attention to the following points
1
、
Should ensure the cleanliness of lift, There's no obstacles around to avoid crash or
fall during the lifting process, damages to people and equipment
2, Maintain the hydraulic hoses, electrical lines are clean to avoid aging and damaged
Of lines.
Summary of Contents for QJ-Y-2-35
Page 1: ...0 2 Post Lift Instruction Manual Model No QJ Y 2 35...
Page 7: ...6 Chapter II Safety instructions...
Page 9: ...8 2 2 The warning signs...
Page 10: ...9...
Page 18: ...17...
Page 19: ...18 1 Hex nuts M20 8 2 Wire rope 2 Pump station connection diagram...
Page 25: ...24...
Page 26: ...25...
Page 27: ...26 Above is the drawing of parts of point a and b...
Page 29: ...28 Above is the drawing of parts at point c...
Page 30: ...29 Above is the drawing of parts at point e and f...
Page 40: ...39 7 3 Hydraulic principle diagram Interface schematic 7 4Pump station decomposition diagram...
Page 46: ...45 Company saved...
Page 47: ...46...
Page 48: ...47...
Page 49: ...48...
Page 50: ...49...
Page 51: ...50...
Page 56: ...55 99 15040000006steel rope 8 8665 2 10091011140920Channel section steel 1...