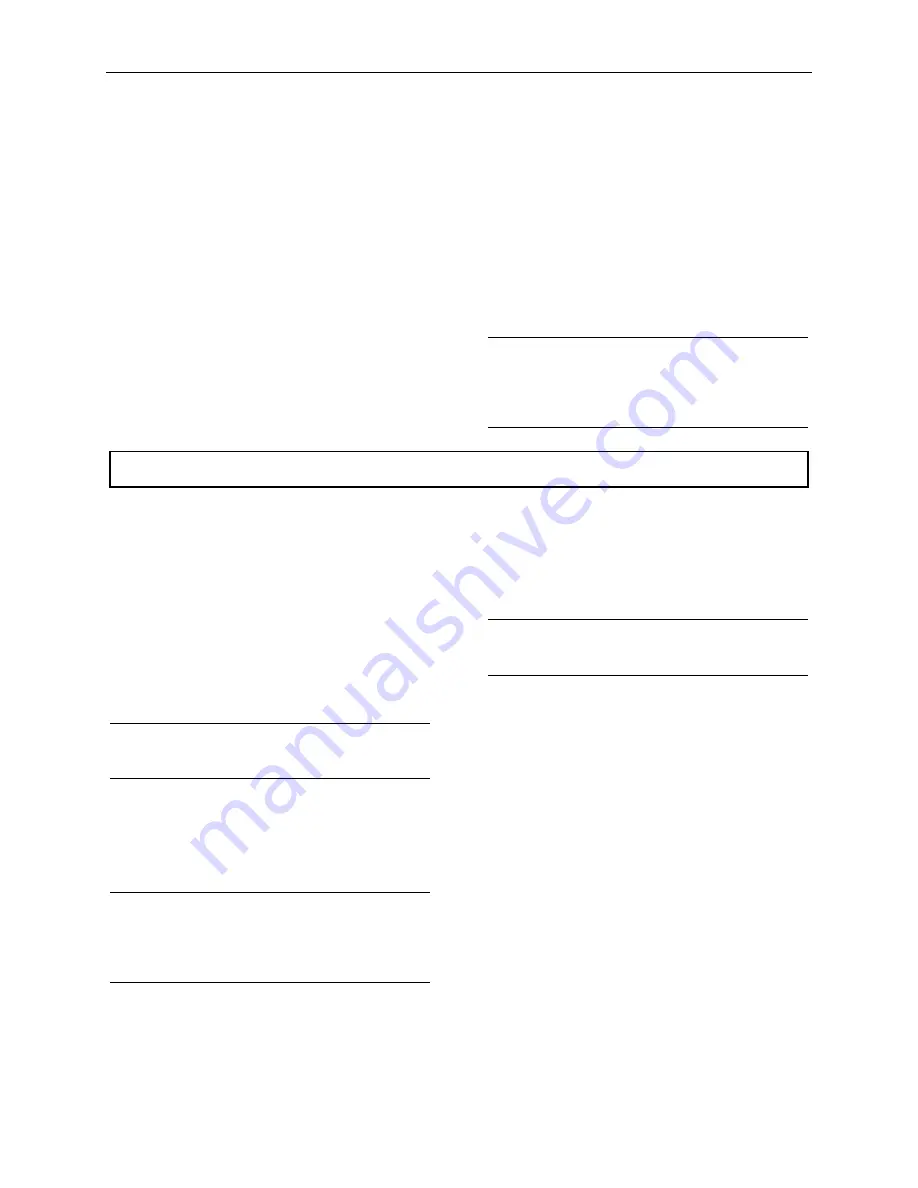
Installation and Operation Manual
SA-07-11-87 Rev A
9
January 2019
Factors which affect the quality of a Sundyne
pump, when stored, are:
•
Humidity
•
Temperature
•
Surrounding chemicals
Long-term storage methods must prevent
damaging conditions from making contact with
the internal components of the equipment. When
the equipment is stored in strong chemical
environments or near salt water, protection must
occur immediately upon receipt of the
equipment.
Recommended Long-Term Storage
Procedures
Sundyne recommends that you do the following
to prevent damage to your pump during long-
term storage:
1. Store your pump only in an indoor, climate
controlled building. These conditions will
maintain constant temperature and humidity.
2. Perform inert gas purging of component
internals.
3. Use desiccant bags.
Note: Because long-term storage of
equipment is of a highly critical nature,
it is recommended that Sundyne be
contacted to provide more details on
the above procedures.
Suction and Discharge Piping
It is recommended to adhere to the following
best practices for installing and maintaining
suction and discharge piping:
1. Install a suction strainer (12 mesh - .062" or
1.6mm opening) initially and clean the
suction line prior to starting the pump. This
procedure will protect the impeller from
damage by mill scale, welding slag, or other
foreign particles during initial startup. After
about three months, a permanent ¼” mesh
strainer is installed.
Note: Sundyne recommends installation of a
differential pressure instrument across
strainer to indicate strainer condition.
2. When installing piping to the pump, ensure
that all piping is supported independently
from the pump.
3. All piping must always line up with the pump
flanges.
Note: Never use force to position piping into
place at the flanged suction and
discharge connection locations. Failure
to have piping properly aligned may
impose excessive strains on the unit.
4. Sundyne recommends using a straight pipe
assembly of at least ten times the length of
the pipe diameter for suction and at least
five times the diameter for discharge.
Note: Carefully select the size of pipe and
fittings to be installed so that friction
losses will remain low.
5. Never use a suction pipe that is smaller in
diameter than the pump suction inlet.
6. Sundyne recommends installation of a
discharge check valve to prevent reverse
rotation.
7. Use block valves (both suction and
discharge) when isolating the pump during
shutdown. This practice will minimize
process leakage and prevent possible
reverse rotation from pump back-flow.
8. It is recommended that suction and
discharge pressure gauges be installed on
any pump that is not flow controlled. If no
flow measuring device is installed, there is
no way to determine accurately where on its
curve the pump is operating.