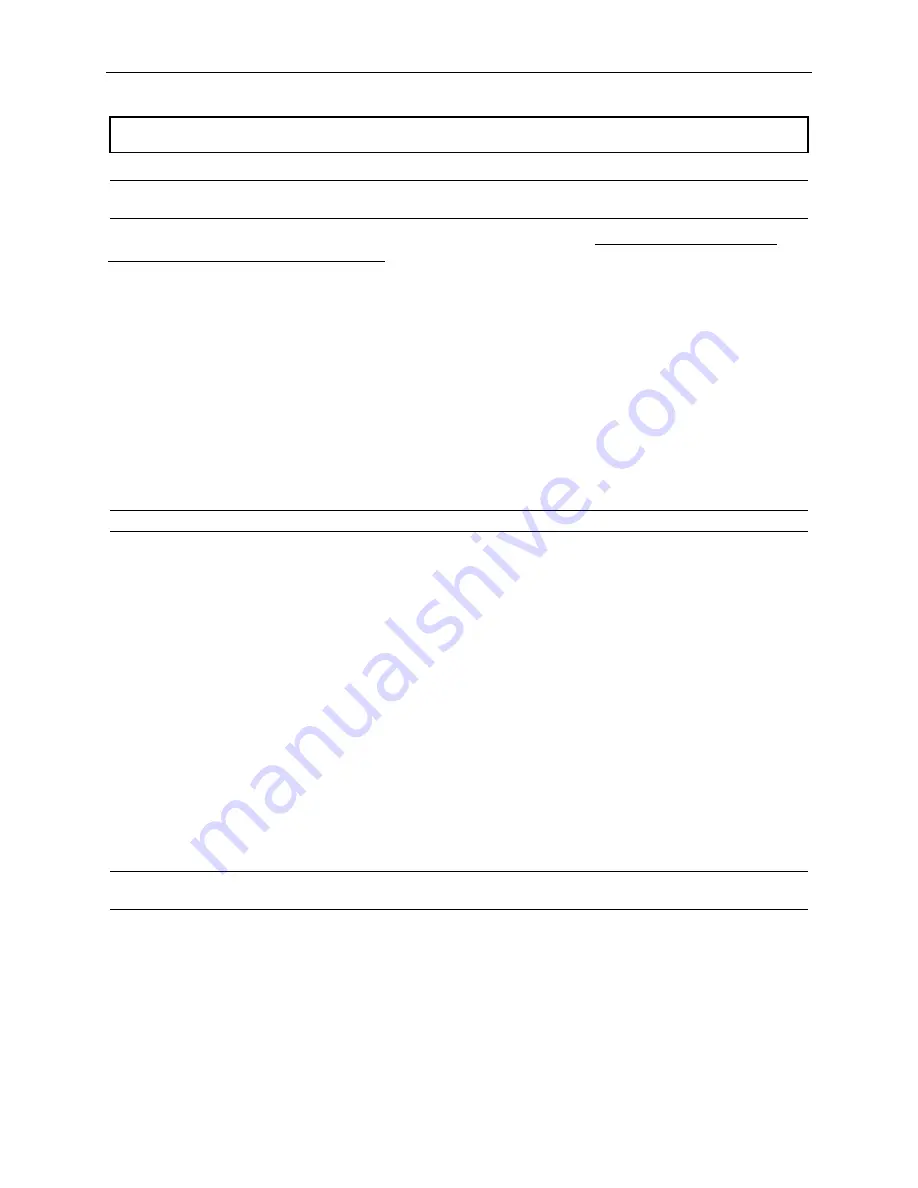
Installation and Operation Manual
SA-07-11-87 Rev A
7
January 2019
Installation and Start-Up Checklist
Note: Lock out all switch gears, including main driver, and instrumentation before working on this
equipment.
This checklist is
NOT
intended to be inclusive. You must read and follow: instruction manuals, outline
drawings, specification sheets and curves for this equipment during installation, commissioning, and
operation. Your total satisfaction is our goal. Please call with any questions or comments. Be sure to have
the unit serial number that is imprinted on the pump nameplate, and request “Sundyne Field Service”.
Is all the information underlined above readily available?
Are the following bolted/threaded connections tight?
•
Pump flange bolts?
•
Seal environment piping and port connections?
•
Pump case drain plug?
Is a check valve installed in the discharge line?
Is Port 1 on the seal housing or the DRAIN on the cartridge seal open to atmosphere, or piped to
safety drain or flare vent header? (Back pressure must not exceed 5 psig).
Note: A drip leg must be used if the Port 1 connection rises from the seal housing.
Are all other seal system ports identified and connected according to the outline drawings?
Do process conditions, suction pressure, suction temperature, discharge header pressure, and
specific gravity agree with specification sheet information?
DO NOT
test the pump on water
unless it is designed for water. Check with your representative or Sundyne if you must test on a
different fluid than shown on the specification sheet.
Prior to starting the unit, have you opened the suction valve fully and discharge throttled to allow
design flow, typically 40-50% open? Check the control valve to be sure it is functional. Inspect the
case drain, ports, and flanges for leaks. Has the pump been vented through Port 6. Check suction
pressure to be sure it agrees with the specification sheet.
Unlock the main driver circuit and bump the motor. Rotation is Counter Clockwise, as viewed
from the top end of the motor. Is rotation correct? Once rotation is verified start the main driver.
After commissioning, bumping the motor is not required.
If pressure control is being used, throttle the discharge valve immediately after start-up. Does the
discharge pressure agree with the specification sheet? If flow control is being used, adjust the
valve until flow agrees with the design value listed on the specification sheet.
Listen for any unusual noises or pressure fluctuations.
Note: If you have any questions or concerns about these procedures or the information supplied, please
call your representative or Sundyne.