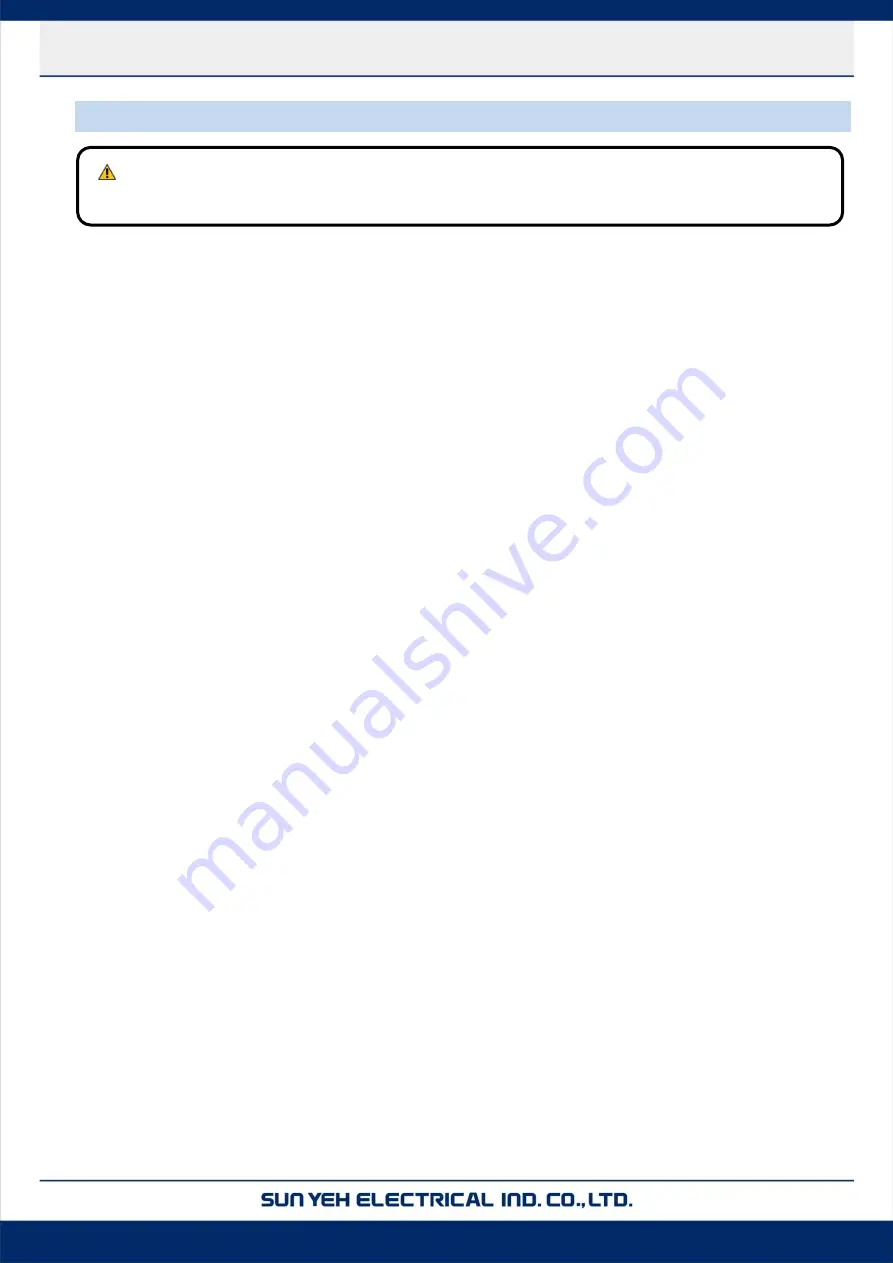
【M Series】Multi-turn Electric Valve Actuator
1
2021.06
Failure to follow safety instructions may cause serious injury, equipment damage, or void-
ed warranty.
1
General Information
1.1
Safety Instructions
Installation, maintenance and repair works must be performed by trained personnel.
The Handling shall follow the safety and warning instruction contained in this manual.
The user should read and follow instructions contained in this operation manual included with
the product. Failure to do this may result in damages and void warranty. Sun Yeh will not
be liable for damages due to operator negligence or misuse.
Local health and safety regulation shall be complied with.
In a few cases, the surface temperature may exceed 60°C (140
℉
). Please check the surface
temperature before operation, using an appropriate thermometer and wearing protective
gloves before operation.
1.2
Installation, Storage, Transport
Please read operation manual and wiring diagram carefully before installation.
Perform all basic settings including stroke limitation for open and close direction prior to op-
eration.
Verify the power supply’s voltage is in accordance with the data on nameplate to prevent short
circuit or electrical/electronic parts damage caused by incorrect power input.
Turn power off before wiring or maintenance.
Connect the ground wire to PE point inside the electric actuator.
To avoid functional failure caused by static, do not touch any components on the PCBA with
metal tools or bare hands.
Use proper techniques when installing conduit and properly seal the connection to prevent
vapor condensation from entering the unit.
Actuator should be installed in an upright or horizontal position. Do not mount upside down
or below a horizontal position.
These units are not designed to operate in vacuum spaces or where an explosive atmosphere
exists.
Periodically inspect actuator enclosure to prevent dust from accumulating.
Summary of Contents for M Series
Page 1: ...SY04 C001A EN APP iOS Android ...
Page 7: ... M Series Multi turn Electric Valve Actuator 4 2021 06 3 2 Nameplate Instruction Caution ...
Page 24: ... M Series Multi turn Electric Valve Actuator 21 2021 06 Settings Menu 8 1 2 ...
Page 25: ... M Series Multi turn Electric Valve Actuator 22 2021 06 ...
Page 26: ... M Series Multi turn Electric Valve Actuator 23 2021 06 ...
Page 75: ......