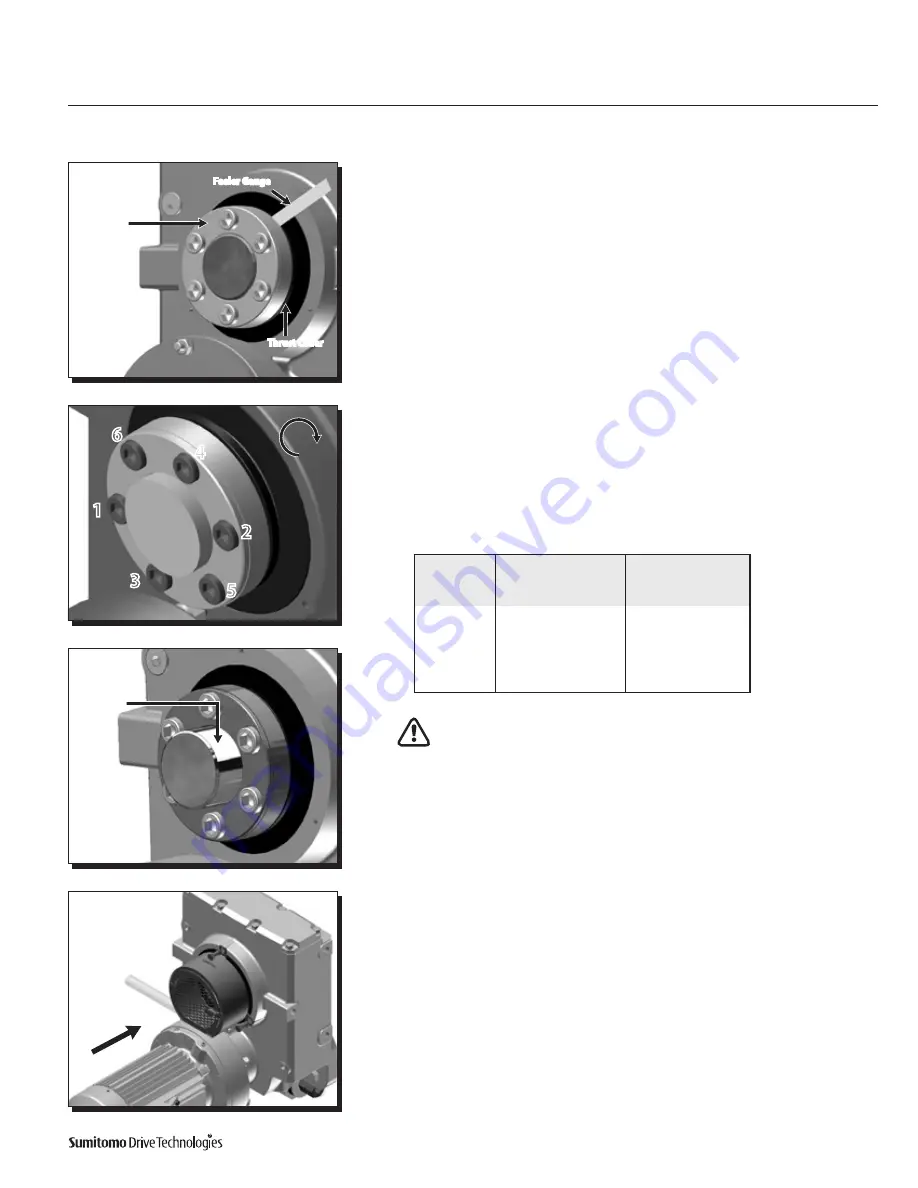
Cyclo® HBB
Operation & Maintenance Manual
11
Cyclo® HBB
Installation onto Driven Shaft
Using Taper-Grip® Bushing
11
Screw bolts into Taper-Grip bushing
• Lightly oil the threads of each bolt before inserting.
• Finger tighten each bolt to secure in place
• Be sure to
maintain the 1 mm
(approximate)
gap
between the
thrust collar
and the
bushing flange
12
Tighten bushing bolts to the correct torque value
• Following a star pattern, use a torque wrench to
gradually tighten each socket
head cap screw in 20% increments
• Refer to
Table 1, Taper-Grip Bushing Bolt Tightening Torques
, for the correct
operational screw torques
After the reducer has been running for 20 to 30 hours, re-torque the screws
to the values in Table 2. Screw torques should be subsequently checked at
normal service intervals (i e every 6 months)
13
Apply grease
to the exposed portion of the driven shaft
•
After installing and tightening
the bushing bolts with a torque wrench,
apply
grease or an anti-corrosion product
to the exposed portion of the shaft
14
For units that include a bushing safety cover, reinstall the guard over the
Taper-Grip® bushing
Bushing
Flange
1-3mm
Feeler Gauge
Thrust Collar
1
6
4
2
5
3
Apply grease
to exposed
portion of
driven shaft
Table 2 Taper-Grip® Bushing Bolt Tightening Torques
Cyclo® HBB
Model
Cap screws
(JIS Grade 12.9)
Cap screw
Torque
Qty
Size
Nm
Lb Ft
Z
6
M10x14
31
23
A
6
M12x16
51
37 5
B
6
M12x16
51
37 5
C
6
M16x20
128
95
D
6
M16x20
200
148
E
8
M16x20
200
148
Summary of Contents for Cyclo HBB
Page 1: ...0 7 6 0 1 6 0 0 0 3 H B B O M2 0 1 8...
Page 27: ...MA X MI N...