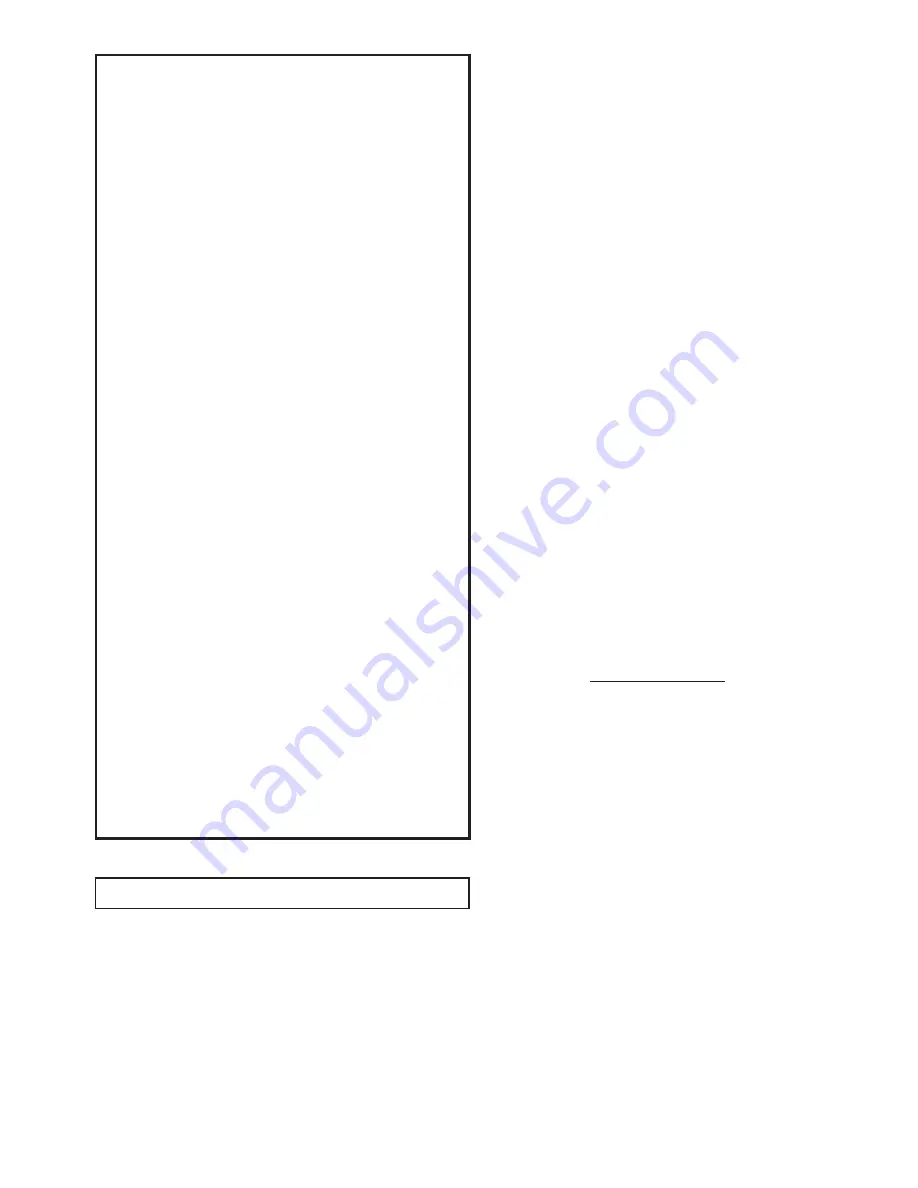
REQUIREMENTS FOR INSTALLATION
Commonwealth of Massachusetts
For all side wall horizontally vented gas fueled equipment installed
in every dwelling, building or structure used in whole or in part for
residential purposes, including those owned or operated by the
Commonwealth and where the side wall exhaust vent termination
is less than seven (7) feet above finished grade in the area of the
venting, including but not limited to decks and porches, the following
requirements shall be satisfied:
1.
INSTALLATION OF CARBON MONOXIDE DETECTORS.
At the time of installation of the side wall horizontal vented
gas fueled equipment, the installing plumber or gas fitter shall
observe that a hard wired carbon monoxide detector with an
alarm and battery back-up is installed on the floor level where
the gas equipment is to be installed. In addition, the installing
plumber or gas fitter shall observe that a battery operated or
hard wired carbon monoxide detector with an alarm is installed
on each additional level of the dwelling , building or structure
served by the side wall horizontal vented gas fueled equipment.
It shall be the responsibility of the property owner to secure the
services of qualified licensed professionals for the installation of
hard wired carbon monoxide detectors.
a.
In the event that the side wall horizontally vented gas
fueled equipment is installed in a crawl space or an attic, the
hard wired carbon monoxide detector with alarm and battery
back-up may be installed on the next adjacent floor level.
b.
In the event that the requirements of this subdivision
can not be met at the time of completion of installation, the
owner shall have a period of thirty (30) days to comply with
the above requirements; provided, however, that during said
thirty (30) day period, a battery operated carbon monoxide
detector with an alarm shall be installed.
2.
APPROVED CARBON MONOXIDE DETECTORS. Each
carbon monoxide detector as required in accordance with the
above provisions shall comply with NFPA 720 and be ANSI/UL
2034 listed and IAS certified.
3.
SIGNAGE. A metal or plastic identification plate shall be
permanently mounted to the exterior of the building at a
minimum height of eight (8) feet above grade directly in line with
the exhaust vent terminal for the horizontally vented gas fueled
heating appliance or equipment. The sign shall read, in print size
no less than one half (½) inch in size,
“GAS VENT DIRECTLY
BELOW, KEEP CLEAR OF ALL OBSTRUCTIONS”
.
4.
INSPECTION. The state or local gas inspector of the side
wall horizontally vented gas fueled equipment shall not approve
the installation unless, upon inspection, the inspector observes
carbon monoxide detectors and signage installed in accordance
with the provisions of 248 CMR 5.08(2)(a)1 through 4.
(b) EXEMPTIONS: The following equipment is exempt from 248
CMR 5.08(2)(a)1 through 4:
1.
The equipment listed in Chapter 10 entitled “Equipment Not
Required To Be Vented” in the most current edition of NFPA 54
as adopted by the Board; and
2.
Product Approved side wall horizontally vented gas fueled
equipment installed in a room or structure separate from the
dwelling, building or structure used in whole or in part for
residential purposes.
UNIT START - UP
WARNING!
Failure to follow these instructions may lead to a fire, explosion, property
damage, personal injury, or loss of life.
CAUTION:
This furnace is equipped with a direct ignition control Do not
attempt to manually light the burners.
BEFORE OPERATING,
smell all around the appliance area for gas. Be
sure to smell next to the floor because gas is heavier than air and will
settle on the floor. If you smell gas STOP. Open the windows and doors
to clear out any gas. Recheck all gas piping and connections for leaks.
TO CHECK THE UNIT OPERATION:
1.
Make sure the gas valve is switched ON. Remove the gas
compartment door. Turn the gas valve knob or move the switch
to the ON position. See figure 5. Do not use any tools to turn the
knob. If you are unable to push in and turn the knob by hand then
call a qualified service technician for assistance. Replace the gas
compartment door.
2.
Turn on electrical power to the unit.
3.
Switch the room thermostat to heat.
4.
Raise the set point to above the room temperature.
5.
The thermostat will call for heat and the combustion blower will
begin to operate.
6.
The combustion blower will operate for 15 to 20 seconds before
the ignition controls begins sparking, then the gas valve will open
and the burners will light. The burners can be viewed through the
sight glass in the door panel.
7.
The room air blower starts 30 seconds after the burners light.
8.
Once the room reaches the set temperature, the burners turn off
and the room air blower turns off 90 seconds later.
9.
Switch the room thermostat over to cooling.
10.
Lower the set point to below the room temperature.
11.
After a slight delay the room air blower will begin to run and the
compressor will start. Note: There will be a 5 minute delay in the
compressor starting if the thermostat set point was raised and then
lowered again.
12.
Once the room reaches the set temperature, the compressor will
turn off and the room air blower will turn off 30 seconds later.
TO SHUT DOWN UNIT
To turn off the unit switch the room thermostat to OFF. Turn the electrical
power off and close the manual gas supply valve before performing any
service to the unit.
HEATING ADJUSTMENTS
1.
Turn off the unit at the room thermostat and shut off the manual gas valve.
2.
Connect a pressure gauge with suitable range (0 to 10” for natural and 0 to
15” for LP) to the inlet pressure port on the gas valve. See figure 5.
3.
Open the manual gas valve and turn the unit on.
4.
Once the furnace is operating, check the inlet gas pressure. Adjust the
pressure regulator to obtain an inlet pressure of 5” to 10” water column for
natural gas and 11” to 13” for LP gas.
5.
Turn off the unit and shut off the manual gas valve.
6.
Move the pressure gauge to the manifold pressure port on the gas valve.
See figure 5.
7.
Once the furnace is operating, check the manifold pressure. Adjust the gas
valve pressure regulator to obtain a manifold pressure of 3.5” water column
for natural gas and 10.0” water column for LP gas.
8.
On natural gas installations the input to the furnace must be checked to
insure safe operation. Any other gas appliances that use the gas meter
must be turned off including the pilot lights.
9.
With the Dynapack furnace running, count the time it takes for the gas meter
to make one revolution. Also record the gas meter rate of cubic feet per
revolution. You will also need the average heating value of the natural gas
for your location. Plug these factors into the equation below to calculate the
gas input rate to the furnace in BTU per hour.
BTU/HR Input =
Cubic Feet Per
Revolution
X 3600 X Heating
Valve
Number of Seconds Per
Revolution
10.
Your recorded value on input must be or- 2% of the rated input. If it
is not then adjust the manifold pressure lower to reduce the input or higher
to increase the input. Do not go outside of 3.2” to 3.8” water column.
11.
The only adjustment for LP gas is to maintain the 10” water column manifold
pressure.
12.
Turn off the unit, close the manual gas valve, and remove the pressure
gauge. Make sure the gas valve pressure port plug screws are tightened
along with the gas valve regulator cap. Replace the burner compartment
door.
13.
Open the manual gas valve and turn on the furnace.
14.
Place a thermometer in the return air along with one in the supply air
as close to the furnace as possible. Once the supply air temperature is
constant, record both temperatures. Subtract the return air temperature
from the supply air temperature. This difference is the temperature rise of
the furnace.
15.
Compare the measured temperature rise to the nameplate range. If the
measured rise is lower than the nameplate minimum, then select the next
lower blower speed for the heating speed. If the measured temperature rise
is above the nameplate maximum, then select the next higher blower speed
for the heating speed.
16.
If a new blower speed was selected then re-measure the temperature rise
and repeat the adjustment if needed.
COOLING ADJUSTMENTS
The only cooling adjustment that can be made is in the blower speed.
1.
Turn the unit on in the cooling mode and allow to operate until stable.
2.
Place a thermometer in the return air opening and another in the supply air
opening as close to the unit as possible.
3.
The a/c unit must operate until condensate water is coming off of the
evaporator coil. Measure the return and supply air temperatures.
4.
Proper cooling operation is obtained if there is a 20 degree Fahrenheit drop
in air temperature through the a/c unit.
5