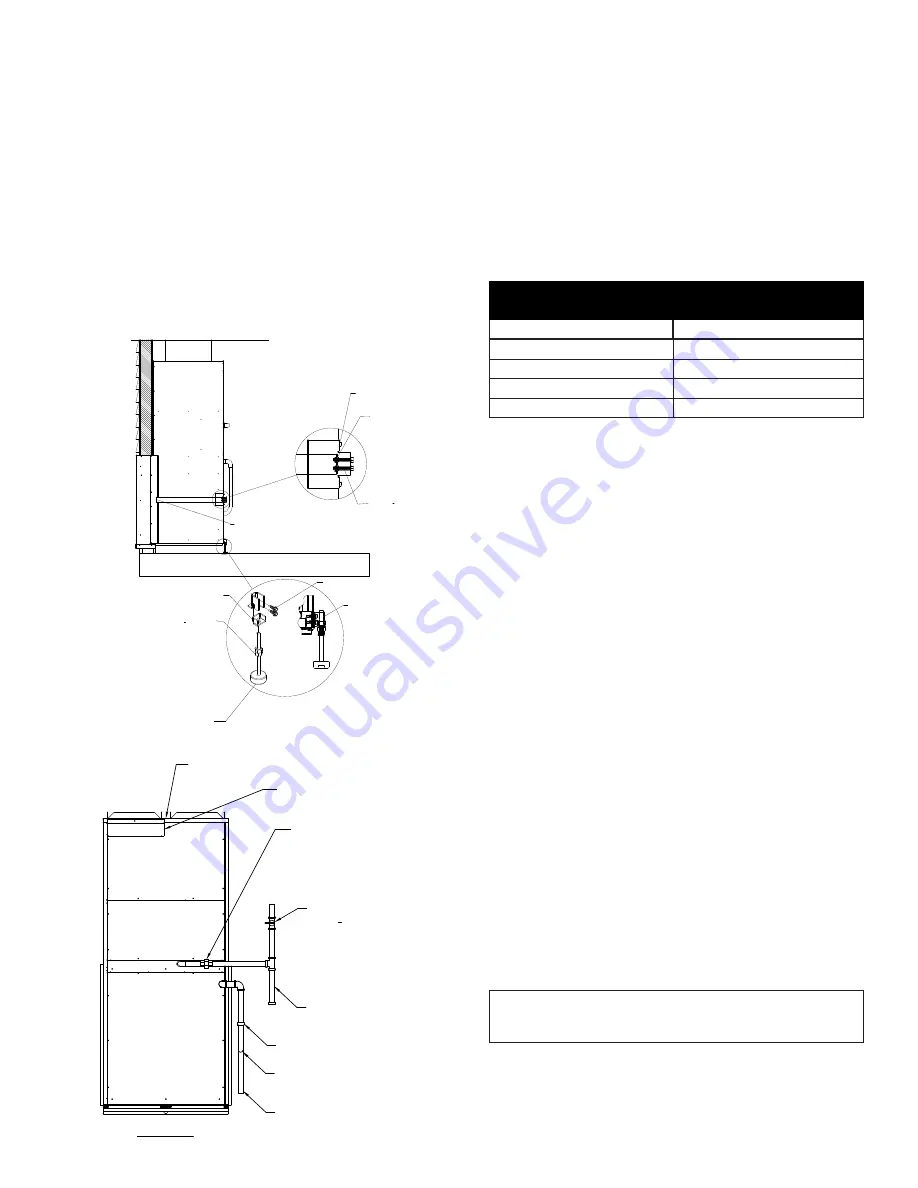
INSTALLING AND SECURING UNIT
TO WALL SLEEVE
Before installing and securing the unit to the wall sleeve, make sure
that the proper grille kit is installed. Due to the temperatures of the
combustion products released from the gas vent, DynaPack gas package
units require the use of an aluminum grille kit (see ACCESSORIES on
page 7).
1.
Double check the installation of the wall sleeve to make sure it is securely
attached to the wall opening. Inspect the wall sleeve drain for proper
installation if an inside drain is being used.
2.
Examine the gaskets on the wall sleeve to make sure there is a continuous
seal between the wall sleeve and the unit.
3.
Place DynaPack unit onto the wall sleeve. Lift the unit 3/4" and place over
the wall sleeve base (see Figure 3). A PALLET JACK works well for this.
Temporarily block the unit up and install front leveling bracket (see Figure
3). Adjust leveling legs to level.
4.
Use the two retaining straps to secure the unit to the wall sleeve (see Figure
3). Verify that the gaskets of the wall sleeve make a complete seal to the
unit paying particular attention to top and bottom corners of the unit to
sleeve seal. Caulk if needed.
DUCT WORK
The duct work for the dwelling should be designed for the lowest
possible static pressure to reduce energy usage and noise. Table 2 lists
the approximate cfm delivery of the units on each of the indoor blower
speeds. Table 4 lists the recommended heating and cooling speeds
with its approximate cfm delivery. Use both tables to properly design
the duct system for both heating and cooling cfm.
AIR FILTER
The Dynapack unit is equipped with a permanent, cleanable air filter.
This filter can be used if the unit is installed so that the filter is accessible
to the homeowner. The permanent filter installed inside the unit must
be removed and discarded if a disposable filter is installed in the return
air duct. See Table 3 for the minimum filter area required for the
Dynapack unit based on unit capacity. It is recommended that air filters
be cleaned or replaced monthly to keep the cooling coil and interior duct
surfaces clean and able to operate most efficiently. Optional MERV 13
filters are available.
MINIMUM REQUIRED SURFACE AREA FOR
DISPOSABLE FILTERS
MODEL NUMBER
FILTER AREA
DYPA12
288 square inches
DYPA18
288 square inches
DYPA24
480 square inches
DYPA30 & DYPA36
480 square inches
TABLE 3
CONDENSATE DRAIN
The Dynapack unit and wall sleeve each have there own drain. The unit
drain is for the condensate developed by the evaporator coil. It needs
to be trapped and routed to the building drain system. Use ¾” pvc pipe
and fittings (field supplied).
The wall sleeve is equipped with a drain pan that collects rain water
entering the wall sleeve and the unit condenser coil area. At the time
of installation of the wall sleeve, this drain can be directed directly out-
side or turned inside and routed to the building drain system. If the
wall sleeve drain is routed to the building sewer system then it must be
trapped to prevent sewer gasses from escaping.
ELECTRICAL CONNECTIONS
The Dynapack unit is approved using copper conductors only. See the
unit data plate for unit minimum circuit ampacity. Size the wire based
on the unit circuit ampacity, type of wire used, and method of wiring, in
conduit or open. If the electrical supply is 208 volt, then do not exceed
3% voltage drop based on the length of wire run. See the National
Electrical Code or the Canadian Electrical Code for more information.
The typical electrical supply is two phase wires where voltage measured
is 208-230 volts phase to phase. An additional wire for unit grounding
is required. See the unit data plate for the maximum fuse or circuit
breaker size. It is recommended that time delay fuses or a two pole
HACR breaker be used in order to prevent nuisance trips.
Alternately, the Dynapack unit may be wired with one phase wire
where the voltage measured is 208-230 volts phase to neutral. In this
case, the phase wire should be connected to L1 on the contactor. An
additional wire for unit grounding is required.
On 208 volt systems the transformer wiring needs to be changed. Swap
the red transformer wire for the orange wire for 208 volt operation.
A disconnect should be installed next to the unit so the electrical power
can be turned off for servicing or maintenance.
GAS SUPPLY
All Dynapack units are built to operate on natural gas. The unit must
be converted using the manufacturers conversion kit in order to operate
on LP gas.
WARNING!
Any conversion of a natural gas unit to liquefied petroleum (LP) gas must be
done by qualified personnel using a conversion kit available from the manufacturer, following
the instructions in the conversion kit, If done improperly, over firing of the burners and improper
burner operation can result. This can create carbon monoxide which could cause asphyxiation.
Minimum gas supply pressure for purposes of input adjustment:
Minimum
Maximum
Natural Gas
5" W.C. *
10" W.C.
Liquefied Petroleum (LP) Gas
11" W.C.
13" W.C.
*Water Column
3
#10-24 X 1
1
2
MACHINE SCREW
LEG LEVELER
38-16 HEX NUT
THE LEVELER BRACKET INSTALLS
INTO UNIT BRACKET AND IS HELD
IN PLACE BY THE UNIT WEIGHT
#12 X .75" DRILL SCREWS
(2 PLACES)
LOCATE BRACKET BY INSTALLING
THE TAB UNDER THE UNIT BASE
AND ABOVE THE BASE RAIL.
TINNERMAN CLIP
ATTACH BRACKET TO UNIT
WITH (2) #10 X 1/2" DRILL SCREWS
(2 ON EACH BRACKET)
ENGAGE FLANGE ON WALL SLEEVE
WITH FLANGE ON STRAP. TIGHTEN
MACHINE SCREWS UNTIL BRACKET
CAN BE SECURED TO UNIT WITH
DRILL SCREWS.
RETURN
SUPPLY
ACCESS PANEL
TO
CONTROLS
ACCESS PANEL
TO GAS VALVE
AND BURNERS
ACCESS PANEL
TO COMPRESSOR
AND OUTDOOR FAN
DRIP LEG (FIELD SUPPLIED)
MANUAL SHUTOFF VALVE
WITH
1
8
"NPT PLUGGED TAPPING,
ACCESSIBLE FOR TEST GAUGE
CONNECTION (FIELD SUPPLIED)
CONDENSATE DRAIN
GROUND JOINT UNION
(FIELD SUPPLIED)
FILTER DOOR
TRAP
ROUTE TO BUILDING DRAIN
ELECTRICAL POWER ENTRANCE
FRONT VIEW
Figure 4
Figure 3