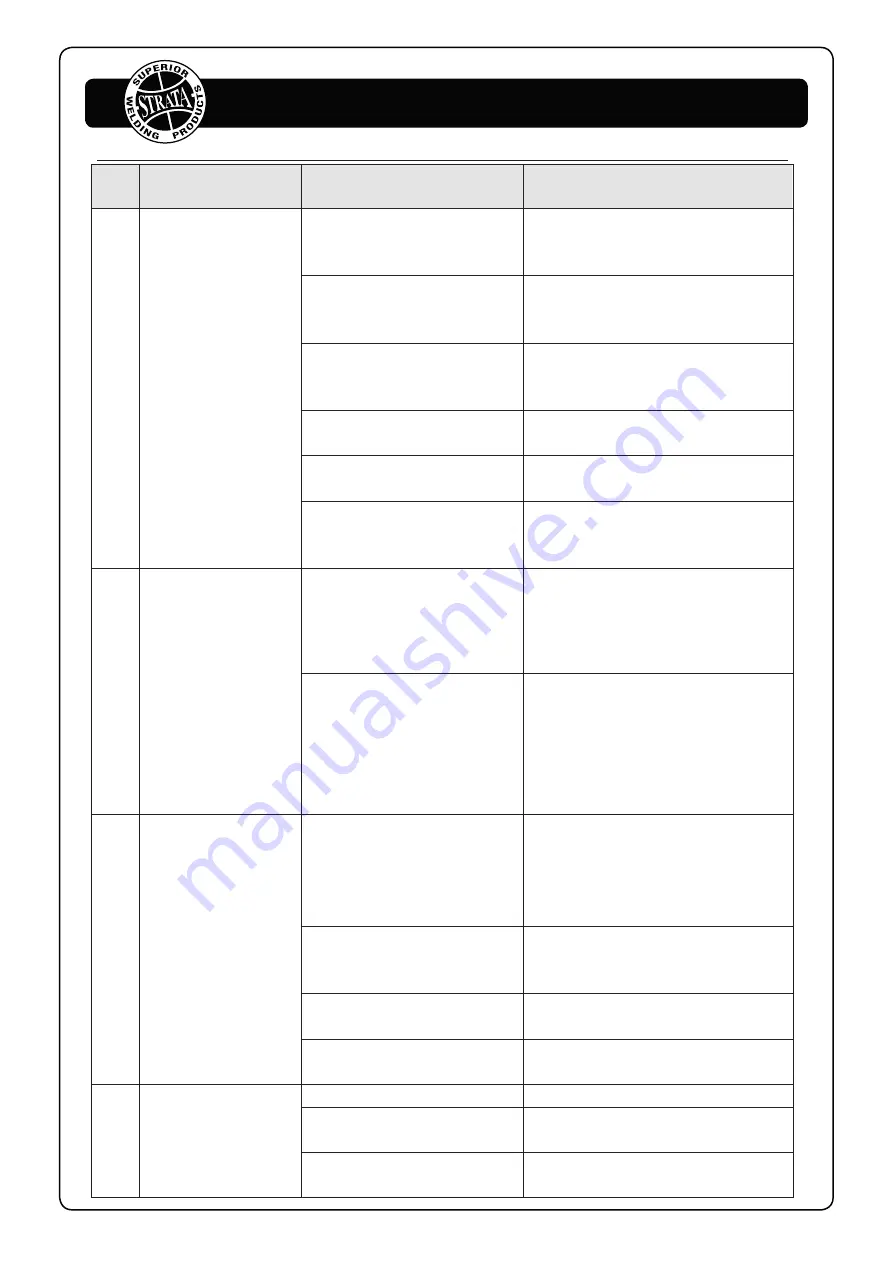
MAINTENANCE AND TROUBLESHOOTING
NO.
Problem
Possible Reason
Suggested Remedy
1
T
ungsten burning
away quickly
Incorrect Gas or No Gas
Use pure Argon. Check cylinder has
gas, connected, turned on and torch
valve is open
Inadequate gas flow
Check the gas is connected, check
hoses, gas valve and torch are not
restricted.
Back cap not fitted correctly
Make sure the torch back cap is
fitted so that the o-ring is inside the
torch body
Torch connected to DC +
Connect the torch to the DC- output
terminal
Incorrect tungsten being used Check and change the tungsten type
if necessary
Tungsten being oxidised after
weld is finished
Keep shielding gas flowing 10–15
seconds after arc stoppage. 1 second
for each 10amps of weld current.
2
Contaminated
tungsten
Touching tungsten into the
weld pool
Keep tungsten from contacting weld
puddle. Raise the torch so that the
tungsten is off of the work piece 2 -
5mm
Touching the filler wire to the
tungsten
Keep the filler wire from touching
the tungsten during welding, feed the
filler wire into the leading edge of
the weld pool in front of the tungsten
3
Porosity - poor
weld appearance
and colour
Wrong gas / poor gas flow
/gas leak
Use pure argon. Gas is connected,
check hoses, gas valve and torch are
not restricted. Set the gas flow
between 6-12 l/min. Check hoses
and fittings for holes, leaks et
Contaminated base metal
Remove moisture and materials like
paint, grease, oil, and dirt from base
metal
Contaminated filler wire
Remove all grease, oil, or moisture
from filler metal
Incorrect filler wire
Check the filler wire and change if
necessary
4
Yellowish residue /
smoke on the
alumina nozzle &
discoloured
tungsten
Incorrect Gas
Use pure Argon gas
Inadequate gas flow
Set the gas flow between 10 - 15
l/min flow rate
Alumina gas nozzle too small Increase the size of the alumina gas
nozzle
62
www.strata.co.nz
ADVANCEMIG 255C