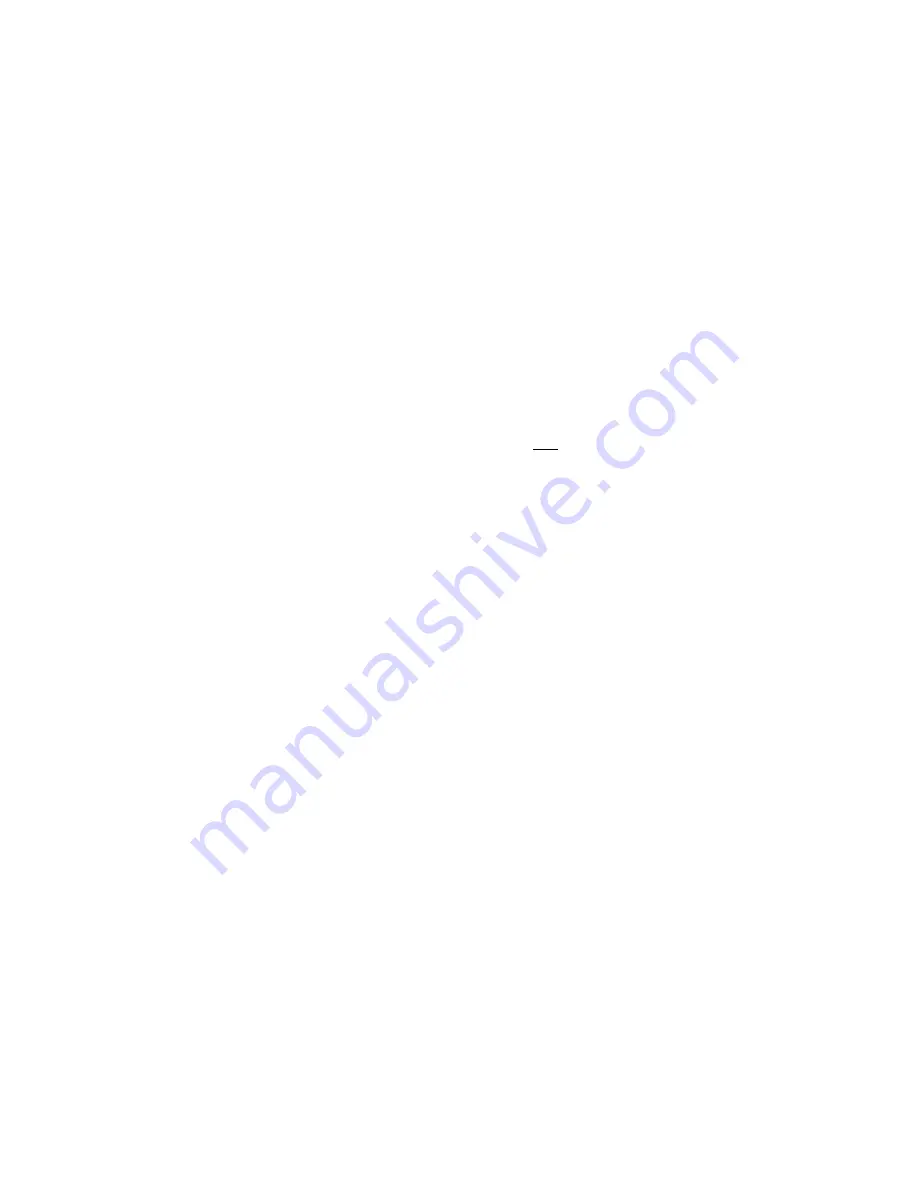
Fuselage Continued
Complete the next three steps (64, 65, and 66) using a slow setting aliphatic wood glue
(Carpenters or White glue works fine) to bond parts along mating surfaces. Note that the
front of the parts in these steps will form a shelf where the nose sheeting will later rest, thus
proper fit and alignment will be critical.
64.
Locate two each of the following parts: F55, F56, and F57. These will form the
right
and
left
bottom
of the nose section. Fit one each F55 to the
inside
of
right
and
left
fuselage
doublers, resting on the outer steps of part F51 and the motor mount F52. Remove part,
coat mating surfaces with a slow setting aliphatic wood glue (carpenters glue) and re-install.
65.
Fit two each of part F56 along the inside of
right
and
left
F55, resting on F51 and F52.
Remove part, apply glue and bond as given in step 64 above.
66.
Finally, fit two each of part F57 together at
center
between the
right
and
left
parts F56,
resting on parts F51 and F52.
Note: Due to variation in thickness of materials from the mill (which tend to run over), it may
be necessary to slightly reduce the thickness of one part F57. We do not advise simply
forcing this part to fit, rather use a fine grit paper to carefully reduce the part thickness so
that the fit is not overly snug, but certainly not loose and full of gaps. If you do over sand or
the material runs thin, it will be necessary to fill any gaps with balsa wood filler.
Allow the glue used to bond parts to setup, now working from
inside
the nose of the model
use medium CA to bond parts F55, F56, F57, the fuselage doublers, motor mount, and
former F30.
67.
Fit and bond F58a, F58b, and F58c together to form the F58 nose sheeting.
68.
Moisten both surfaces of F58 with glass cleaner to soften it and allow it to bend around the
curves of the nose easily. Allow the glass cleaner to soak in for a couple of minutes. Now
position F58 on the nose, tabbing it into the slots in the upper fuselage sides. Carefully
bend the sheeting around the nose, and hold it in place with masking tape until dry. When
the wood is thoroughly dry, remove the tape and nose sheeting. Coat the mating surfaces
of the nose where the sheeting will rest with thick CA. Re-install the sheeting and hold in
place until the glue cures. Wipe up any glue that oozes out around the edges.
While you wait for the nose sheeting to dry skip ahead to begin the hatch assembly steps
beginning on page 31 - go ahead, I won’t tell anyone you skipped ahead... just don’t forget
to come back!
69.
Inspect all installed parts within assembly for proper bond.
Revisit any parts that were
simply tack glued together with a thin bead of medium CA glue along adjoining
surfaces.
Now, sand the bottom of the fuselage, removing the stepped surface of the wood and
flowing the rounded bottom into the curve of the nose. Round the corners off - they are
quite thick and can take a fair sized radius. Take your time and make it look nice.
70.
Sand the top and front of the nose smooth. Round off the corners at the front of the nose,
flowing the curves into a sharp point at the back of the nose where the windscreen will meet
the sheeting (about 3/4 inch forward of the cockpit).
Build Instructions
FullHouse™ 500 Build Instructions. © 2012 Stevens AeroModel. All rights reserved.
!
Page 30
□
□
□
□
□
□
□