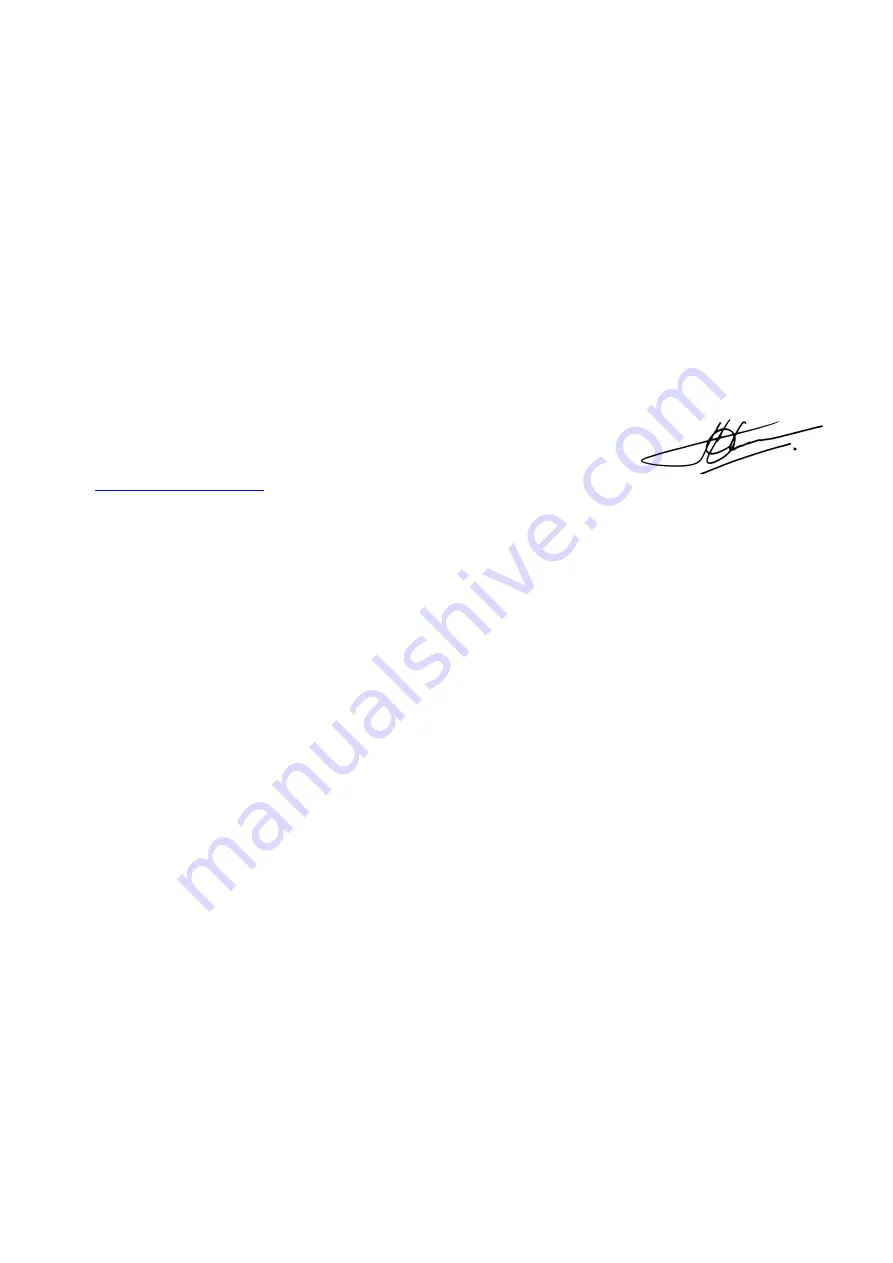
ST 1082-F/R
EC DECLARATION OF CONFORMITY in application of the European 'Machines' Directive (98/37/EC)
ALI DECLARATION OF CONFORMITY in application of the ANSI\ALI ALCTV-1998 and UL201
Manufacturer : Stertil B.V., Postbox 23, 9288 ZG
KOOTSTERTILLE Holland
Machine
: Hydraulic mobile column lifts
Make
: STERTIL-KONI
Model
: ST 1082-F/BAT Fixed wheels and fixed forks
: ST 1082-R/BAT Retractable wheels and fixed
forks
: ST 1082-F/V/BAT Widened model with fixed
wheels and fixed forks
Version
: Battery powered
Options
: Adjustable forks
: Wheel adaptors
: Longer extensions and wheel adaptors
The undersigned U.Bijlsma, Director, for this purpose authorized by Stertil BV, hereby declares that the mobile column lift described
above, has been designed according to the 'Machines' Directive, ANSI\ALI ALCTV-1998 and UL201 and has been found to meet the
fundamental safety requirements stipulated by these directives.
This Wheel Engaging Mobile Automotive Lifts are approved by:
Stertil, Kootstertille
INTERTEK TESTING SERVICES NA. Inc.
U.Bijlsma
3933 US Route 11. Cortland, NY 13045
Director
Telephone: 607-753-6711 Fax: 607-756-9891
Signature:
WEB:
www.intertek-etlsemko.com
Date: 01-05-05
Under report no J99024825-003
Summary of Contents for ST 1082-F/BAT
Page 1: ...Mobile Column Lifts ST 1082 F BAT ST 1082 R BAT Installation operation service 32738980 A ...
Page 2: ......
Page 14: ...10 ...
Page 31: ...27 MICROPROCESSOR BOARD Fig 8 1 Location of fault indication LED s ...
Page 37: ...33 FIG A ...
Page 39: ...35 FIG B Item 6 locked with loctite 542 sealant ...
Page 42: ...38 FIG E CONTROL BOX ...
Page 44: ...40 FIG F SCHEMATIC DIAGRAM ...
Page 51: ......