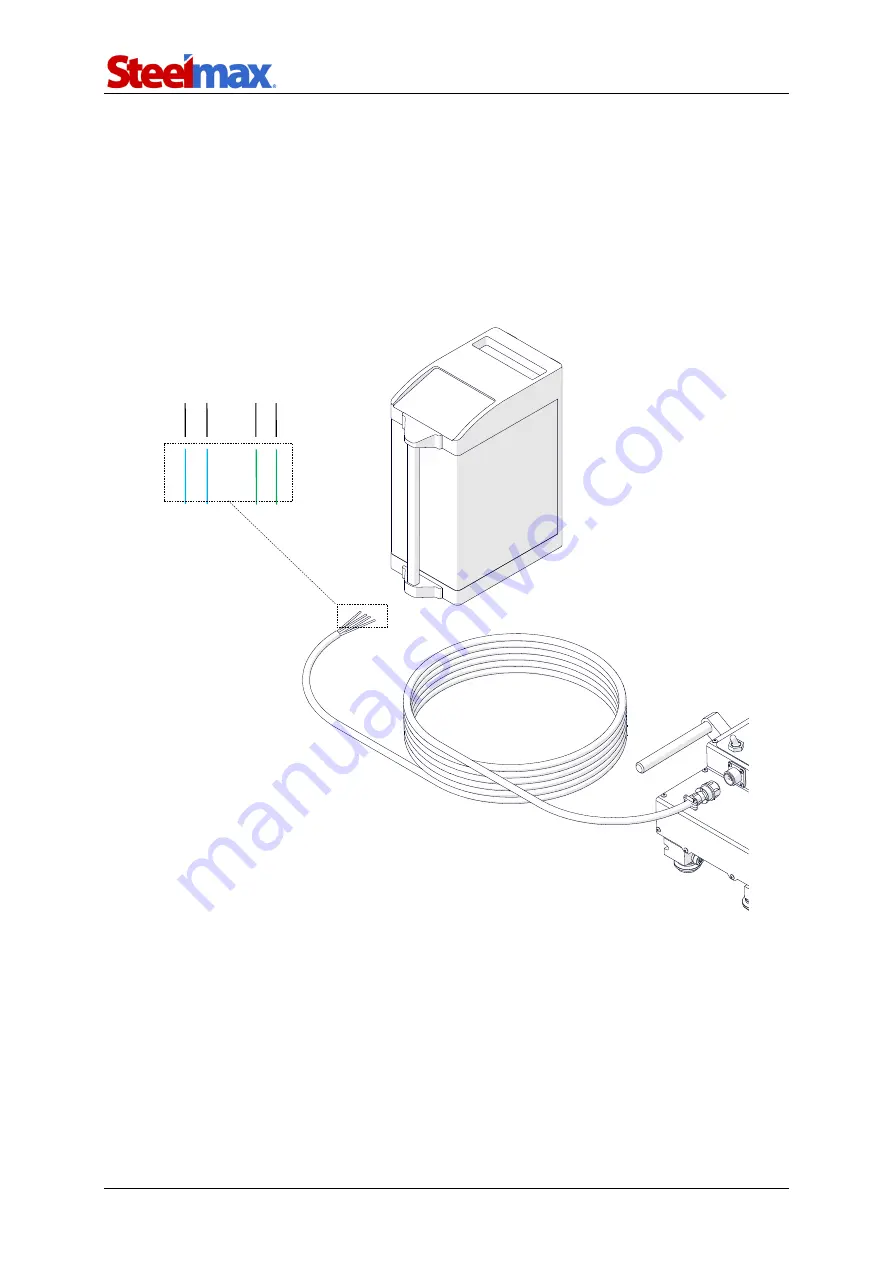
Rail Runner LT
Rail Runner LT
– Operator’s Manual
18
3.6. Connecting to the welding or plasma cutting circuits
The carriage can control two torches by using the arc ignition cable plugged into the
arc ignition socket. To do this, according to the diagram shown in Fig. 10 connect
one blue-jacketed wire to one terminal of the welding / plasma cutting circuit. Then,
connect the other blue-jacketed wire to the other terminal of the same circuit.
To control the second torch, connect the green-jacketed wires to the terminals of the
second welding circuit.
Fig. 10.
Connecting the arc ignition cable to welding / plasma cutting circuits
Make sure that the
arc
ignition
cable
is
connected
correctly. To do this, turn on the
power of the carriage, and then set
the arc ignition
switch
to TEST. This should
enable the arc for a while.
B
lu
e
B
lu
e
G
re
e
n
G
re
e
n
Circuit 2
Circuit 1