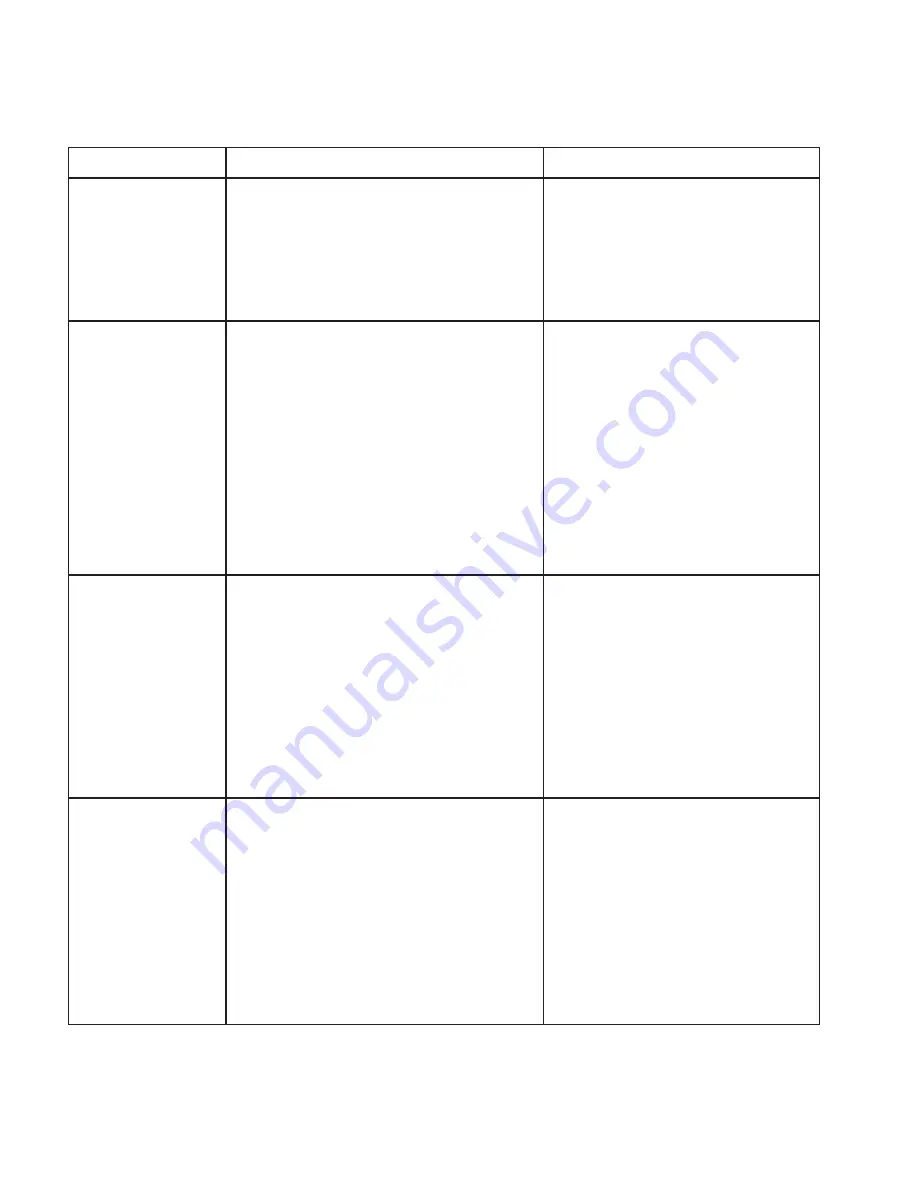
General IntelliPro
®
Troubleshooting Problems (Continued)
Problem
Possible Cause
Corrective Action
Inadequate circulation.
(For IntelliPro alert display
messages, refer to Alerts and
Warnings on page 34).
Filter or pump basket dirty.
Suction/discharge piping is too small.
Speed is set too slow for proper fi ltration cycle.
Check trap basket; if plugged, turn pump off and
clean basket.
Check and clean pool fi lter.
Increase piping size.
Increase fi ltration run time
Electrical problem.
(For IntelliPro alert display
messages, refer to Alerts
and Warning on page 34).
Could appear as a “Low Voltage” alarm.
PRIME ERROR may be displayed.
Could appear as “Over Heat” alert.
PRIME ERROR may be displayed.
Check voltage at motor terminals and at panel while
pump is running. If low, see wiring instructions or
consult power company.
Check for loose connections.
Check line voltage; if less than 90% or more than
110% of rated voltage consult a licensed electrician.
Increase ventilation.
Reduce ambient temperature.
Tighten any loose wiring connections.
Motor internal terminal overload protector is open.
Motor runs too hot. Turn power to
motor off.
Check for proper voltage.
Check for proper impeller or impeller rubbing.
Mechanical Troubles and
Noise.
The pump motor is running but with loud noise.
Foreign matter (gravel, metal, etc.) in pump impeller.
Cavitation.
If suction and discharge piping are not adequately
supported, pump assembly will be strained. Do not
mount pump on a wooden platform!
Securely mount on concrete platform
for quietest performance.
Disassemble pump, clean impeller, follow pump
service instructions for reassembly.
Improve suction conditions.
Increase pipe size.
Decrease number of fi ttings.
Increase discharge pressure.
IntelliPro does not respond
to IntelliTouch, EasyTouch,
SunTouch, IntelliComm
commands.
Improper automation IntelliPro setup.
Communication network inoperative.
1. Ensure that the communication cable is connected
at both ends.
2. Check that the IntelliPro local address matches
with the address used in the IntelliTouch.
3. Check that the IntelliPro has been assigned a
circuit name on the IntelliTouch.
4. Ensure that the IntelliPro display says “DISPLAY
NOT ACTIVE”.
A defective device on the network can inhibit the
proper operation of other network device. Devices
should be disconnected sequentially until the network
starts working.
36
IntelliPro
®
Variable Speed Pump Installation and User’s Guide