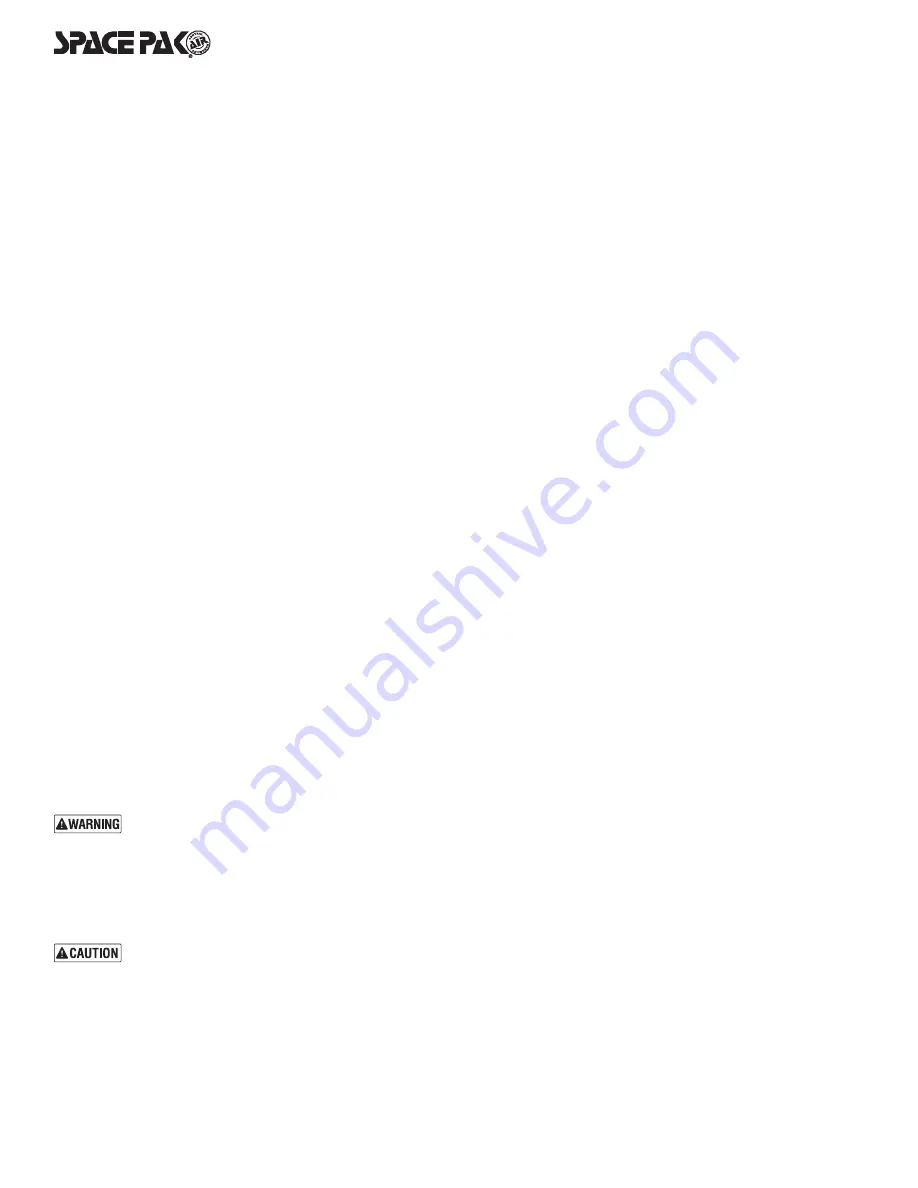
– 6 –
Split Inverter Air-to-Water Heat Pump
Section 3: Installation
Choose the Right Heat Pump Unit
Perform appropriate load calculation to determine required
heating or cooling load for the project. Refer to specifications in
this manual to determine proper size heat pump.
Installation Location
• The SISO module must be installed outdoors, in a location
capable of supporting the full weight, plus any potential snow
load. The outdoor unit must be secured to the support with
sufficient hardware to withstand any potential wind or seismic
conditions without shifting or tipping. Additionally the outdoor
unit should be installed with enough clearance (see "E"
dimension) to allow for condensate roll-off during the defrost
cycle. This will prevent freezing under the unit during defrost.
• The outdoor module should be located away from sources
of heat or moisture such as combustion vents, dryer vents,
building exhausts etc.
• Proper clearances shown in Fig. 3.3 must be respected.
Water Loop Connection
Please read below for water piping instructions
• The piping must be clean and free from dirt. Prior to insulating
the pipe, it is suggested that a leak test be performed to ensure
no water leaks are present.
• The system must be supplied with a pump sized to provide
the minimum flow rate specified in the Glycol/Water System
Design section of this manual. Pump selection must consider
the pressure loss through the plumbing system and its
components, plus the pressure loss through the Heat Pump's
internal heat exchanger. The pump must be rated for the full
range of heated or chilled water temperatures, as well as any
anti-freeze or corrosion inhibitor additives.
• Install a wye strainer capable of system flow rate at anticipated
level of contamination at the liquid input of the heat pump as
shown in this manual to protect the internal components from
damage or fouling due to contaminants or sediment.
• DO NOT use the heat pump for DIRECT heating of potable
water. The heat exchanger and internal components are not
suitable for this application.
Never expose the SIS Hydronic circuit to pressures
in excess of 60 PSI. Loss of coolant, property
damage or equipment damage may result.
The total system must be protected with a Pressure
Relief Valve or valves sized to protect the system
component with the lowest pressure rating. In no
instance shall this exceed 60 PSI.
If the indoor module is installed in a location where
it may be exposed to freezing temperatures, it is the
responsibility of the installing contractor to ensure
that sufficient Propylene Glycol concentration is
maintained in the hydronic circuit to provide freeze
protection in all foreseeable conditions.
If the hydronic circuit is not charged with any anti-
freeze solution, then the water must include a cor-
rosion inhibitor suitable for hydronic systems, and
installed according to the manufacturer's recom-
mendations.
Electrical Connections
Both the SISI indoor module and the SISO outdoor module must
be connected to individual circuits, each sized and protected
according to the Rating Labels affixed to the exterior of each
module.
If the auxiliary heater function is employed, the electric elements
must be powered by their own dedicated circuit, sized and protected
according the auxiliary heater manufacturer’s requirements.
Connect the RS485 communication wires using the two-conductor
cable attached the supplied line set.
If the auxiliary heater or Domestic Hot Water functions are used,
make electrical connections according to drawing labeled SISI
Indoor Module Wiring.
All electrical connections must be made in accordance with the
National Electric Code and all local codes and requirements.