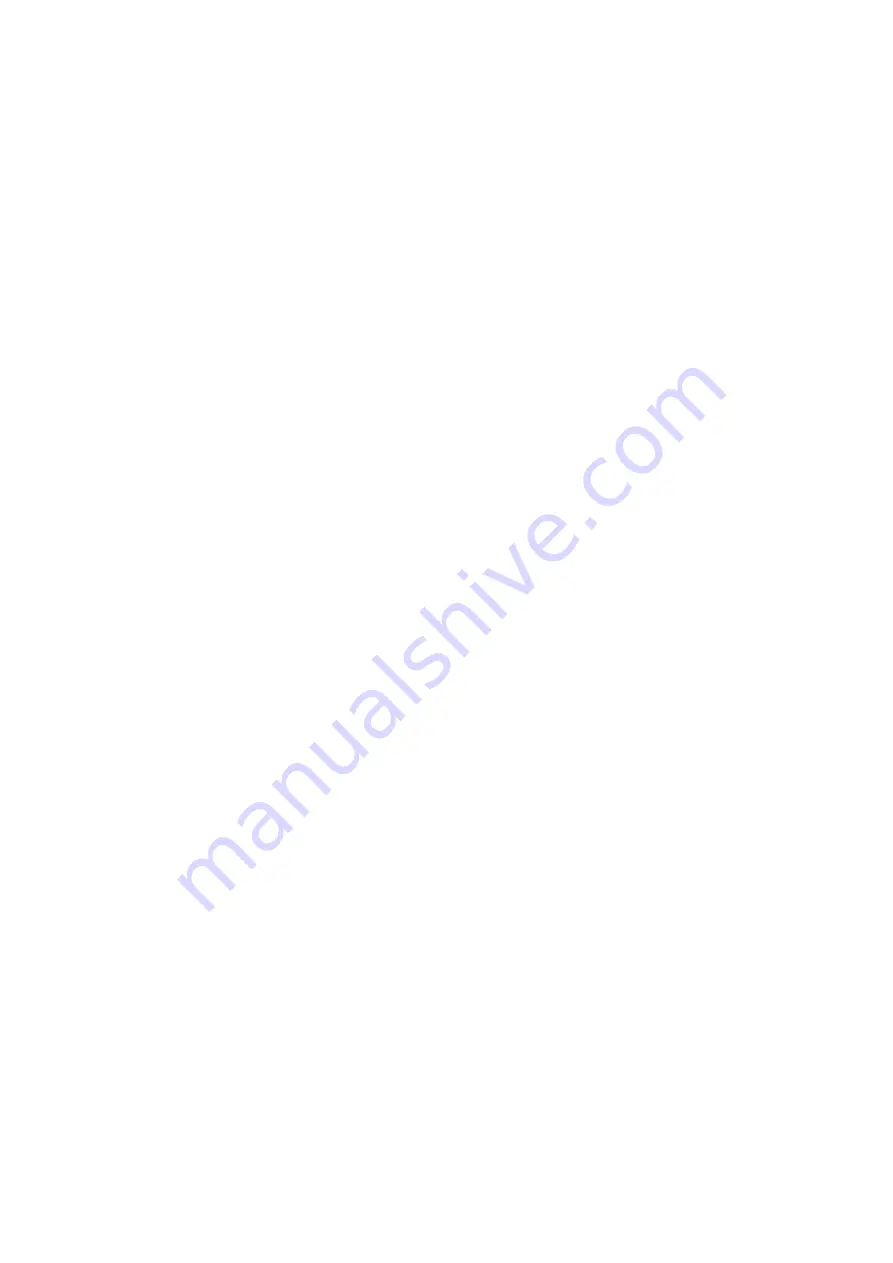
137
Section 7
Circuit Description
7-1. Circuit Description
7-1-1. Playback System
Data playback system
The RF signal of channel 0a played back from the disc is transferred from the optical block to the Disc
Drive LSI (IC100) on the BD-48 board where AGC and equalizing correction is applied to the signal.
Then the RF signal is converted to a digital signal by the read clock generated in synchronization by the
Read PLL.
After that, PR equalization, Viterbi decoding, 1-7PP demodulation, descrambling, error correction, and
other processing are applied to the signal, and then the processed signal is sent to BRIDGE (IC700) with
the SATA Interface.
In the same way, the RF signal of channel 0b, 1a, 1b are also processed by the Disc Drive LSI (0b: IC200,
1a: IC300, 1b: IC400) on the BD-48 board, and then sents to BRIDGE (IC700).
BRIDGE (IC700) controls Read system of four channels individually to produce the maximum transfer
rate, integrates it to a single system, and then sends it to the UI-32 board.
The SATA-USB3.2 BRIDGE (IC32) on the UI-32 board converts the SATA signal to a USB3.2 signal,
and the USB3.2 signal is output from the USB connector (CN32).
Address playback system
The address information played back from the disc is sent from the optical block to the Disc Drive LSI
(IC100, IC200, IC300, IC400) on the BD-48 board. The Disc Drive LSI detects a wobble signal and
decodes the address. The detected analog wobble signal is converted to a digital signal, and a wobble
clock (WCK) signal is generated by the digital PLL.
Data recording system
The recording signal that is input to the USB connector (CN32) on the UI-32 board from the host is
converted to the SATA signal by the USB3.2-SATA BRIDGE (IC32), and the SATA signal is sent to
BRIDGE (IC700) on the BD-48 board.
BRIDGE (IC700) controls distribution of Write system of four channels individually to produce the
maximum transfer rate.
Each distributed recording signal is input to the Disc Drive LSI (IC100, IC200, IC300, IC400) of each
channel where scrambling and 1-7PP modulation processing are applied to the signal. Then the processed
signal is sent to the LDD in the optical block with the Write Strategy that meets each media type, and then
the signal is recorded in the disc.
Summary of Contents for PDW-U4
Page 7: ...4 Frame Wiring 151 Revision History 152 ...
Page 24: ...21 Hold the shaded portions Keep away a screwdriver Objective lens Actuator ...
Page 155: ...152 Revision History Date History Contents 2020 10 1st Edition 9 932 764 01 ...
Page 156: ...PDW U4 SY PDW U4 CN J E 9 932 764 01 Sony Corporation Printed in Japan 2020 10 08 2020 ...