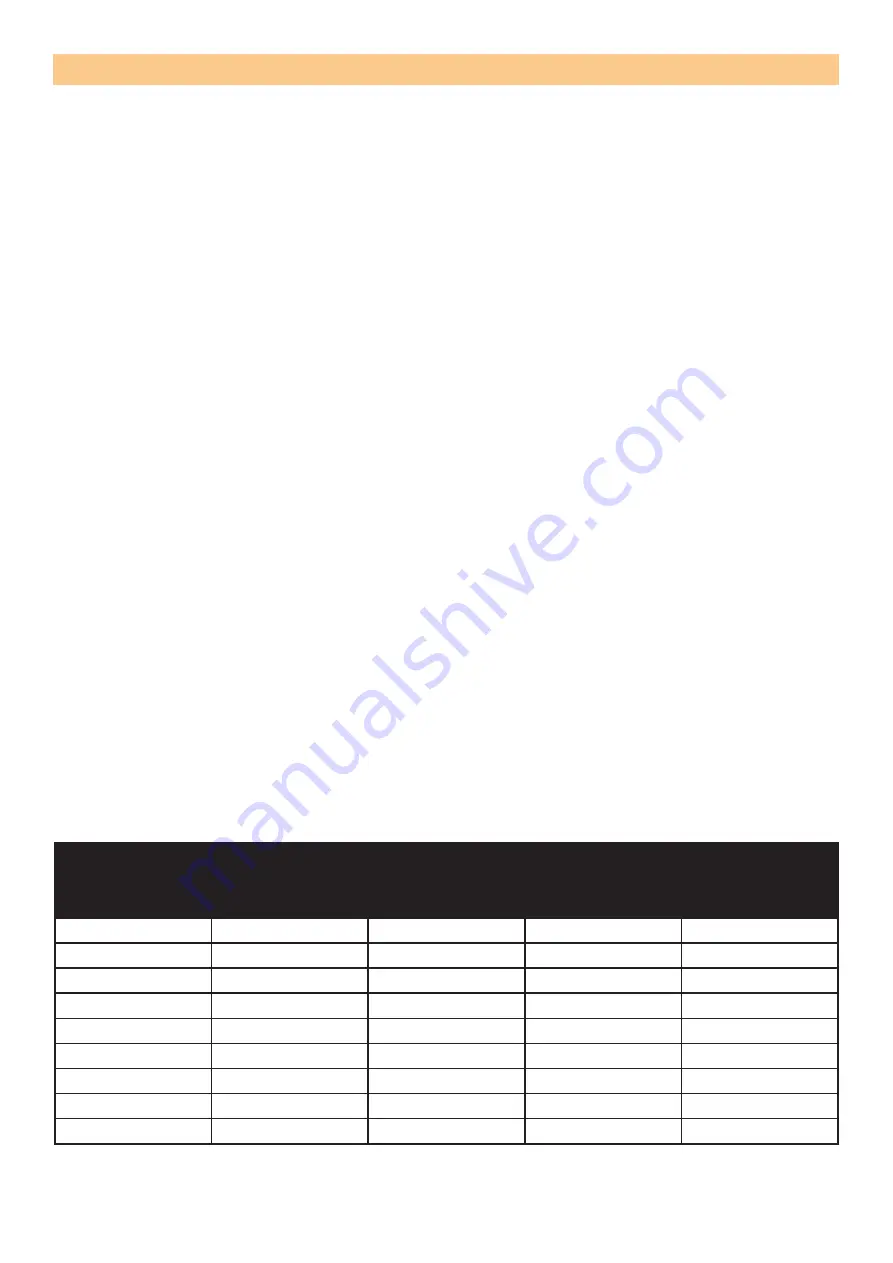
Page 3 - 18
TL49J
PHYSICAL DAMAGE
When looking for physical damage, it is important that the machine is clean. Large dents in the
boom from operators hitting obstacles are generally easy to see. Crack in welds or corrosion dam
-
age can be harder to spot. The biggest wear and tear is due to the constant vibration from towing
the machine. Curbs and speed bumps passed at high speed can also cause severe damage to the
tow bar or the axle.
On machines fitted with the optional sliding axle, inspect the underside of the axle carrier and the
sliding box suspension.
On machines fitted with the fixed axle, check the fixing bolts and the main chassis member.
Check the area just behind the coupling where the vertical boom is secured to the tow bar. Incase
the vertical boom is not secured to the tow bar and the machine is towed over a long distance on
poor roads, damage may have occurred due to the constant banging of the vertical boom against
the towbar. Also check the top boom rest. The top boom must be locked in place during transport.
Note
Forgetting to lower the boom leads to damage occurring to the underside of the top boom due to move
-
ment in its rest position during transportation. Fitting the top boom lock would greatly reduce the need
for top boom repairs or possible replacement.
Another area prone to damage is the drop nose. When reversing, the basket may hit a low wall or a
post. The impact may not be easy to spot on an already battered basket however may bend the bot
-
tom of the drop nose. Check the straightness of the top tie bar. A slight dip is acceptable but a kink or
sideways bend is unacceptable. Check both booms for creases in the steel next to the main bosses
which is next to the slew post and the vertical boom. Hoses and cables are prone to damage, wear and
tear. If the outer sheathing on the hydraulic hose is a slightly frayed fitting, a temporary outer sleeve
may be adequate depending on the size of the damage.
Note
If in doubt, replace or ask Snorkel or its local representative for advice.
NUTS & BOLTS
Replace any missing bolts immediately. The main pivot shafts and pivot pins are secured with one or
two locking pegs. The locking peg not only secures the shafts from falling out but also stops them from
turning.
Most nuts used are nyloc nuts which are superior to the normal full nut and spring washer. Never use
plain nuts and spring washers unless originally fitted. Always torque fixings.
THREAD SIZE
MAXIMUM TIGHTENING TORQUES
UNPLATED
PLATED
Nm
Lbf.in.
Nm
Lbf.in.
M4
4.6
40.7
3.5
31
M5
9.5
84.1
7.1
62.8
M6
16.0
142.0
12.0
106.0
M8
39.0
345.0
29.0
257.0
M10
77.0
682.0
58.0
513.0
M12
135.0
1200.0
101.0
894.0
M14
215.0
1900.0
161.0
1420.0
M16
330.0
2920.0
248.0
2190.0
M20
650.0
5750.0
488.0
4320.0
SERVICE AND REPAIR
Table 3-7
: Torque table for nuts & bolts.
Summary of Contents for TL37-01-007625
Page 1: ...TL37J PARTS MANUAL TL37J PARTS MANUAL...
Page 8: ......
Page 16: ...REPAIR PARTS TL37J PARTS MANUAL JOCKEY WHEEL JOCKEY WHEEL Tue Mar 23 07 46 30 UTC 2021 2 3...
Page 18: ...REPAIR PARTS TL37J PARTS MANUAL AXLE ASSEMBLY AXLE ASSEMBLY Tue Mar 23 07 46 30 UTC 2021 2 4...
Page 20: ...REPAIR PARTS TL37J PARTS MANUAL BRAKE ASSEMBLY BRAKE ASSEMBLY Tue Mar 23 07 46 31 UTC 2021 2 5...
Page 28: ...REPAIR PARTS TL37J PARTS MANUAL SLEW ASSEMBLY SLEW ASSEMBLY Tue Mar 23 07 46 33 UTC 2021 2 9...
Page 33: ...REPAIR PARTS TL37J PARTS MANUAL CAGE ASSEMBLY CAGE ASSEMBLY Tue Mar 23 07 46 34 UTC 2021 2 11...
Page 35: ...REPAIR PARTS TL37J PARTS MANUAL BOTTOM RAM BOTTOM RAM Tue Mar 23 07 46 34 UTC 2021 2 12...
Page 37: ...REPAIR PARTS TL37J PARTS MANUAL TOP RAM TOP RAM Tue Mar 23 07 46 34 UTC 2021 2 13...
Page 43: ...REPAIR PARTS TL37J PARTS MANUAL OUTRIGGER RAM OUTRIGGER RAM Tue Mar 23 07 46 35 UTC 2021 2 16...
Page 55: ...REPAIR PARTS TL37J PARTS MANUAL DECALS UK KIT DECALS UK KIT Tue Mar 23 07 46 38 UTC 2021 2 22...
Page 102: ......
Page 135: ...Page 3 30 TL37J...
Page 136: ...Page 4 1 TL37J TROUBLESHOOTING CONTENTS FAULT FINDING 4 2 FAULT FINDING MATRIX 4 4...
Page 146: ...BATTERY CIRCUIT SCHEMATIC...
Page 147: ...BATTERY HYDRAULIC FLOW DIAGRAM 29 BATTERY HYDRAULIC FLOW DIAGRAM...
Page 148: ...MAINS CIRCUIT SCHEMATIC...
Page 149: ...MAINS HYDRAULIC FLOW DIAGRAM 31 MAINS HYDRAULIC FLOW DIAGRAM...
Page 150: ...PETROL CIRCUIT SCHEMATIC...
Page 151: ...PETROL HYDRAULIC FLOW DIAGRAM PETROL HYDRAULIC FLOW DIAGRAM...
Page 152: ...BI FUEL PETROL CIRCUIT SCHEMATIC...
Page 153: ...BI FUEL HYDRAULIC FLOW DIAGRAM BI FUEL HYDRULIC FLOW DIAGRAM...
Page 154: ...BI FUEL DIESEL CIRCUIT SCHEMATIC...
Page 155: ...DIESEL CIRCUIT SCHEMATIC...
Page 156: ...MAINS GEN SET CIRCUIT SCHEMATIC...
Page 157: ...BATTERY ANSI CANTILT CIRCUIT SCHEMATIC From SN TL37J 01 00291...
Page 158: ...MAINS ANSI CANTILT CIRCUIT SCHEMATIC From SN TL37J 01 00291...
Page 159: ...PETROL ANSI CANTILT CIRCUIT SCHEMATIC From SN TL37J 01 00291...
Page 160: ...BI FUEL PETROL ANSI CANTILT CIRCUIT SCHEMATIC From SN TL37J 01 00291...
Page 161: ...BI FUEL DIESEL ANSI CANTILT CIRCUIT SCHEMATIC From SN TL37J 01 00291...
Page 162: ...DIESEL ANSI CANTILT CIRCUIT SCHEMATIC From SN TL37J 01 00291...
Page 163: ...MAINS GEN SET ANSI CANTILT CIRCUIT SCHEMATIC From SN TL37J 01 00291...