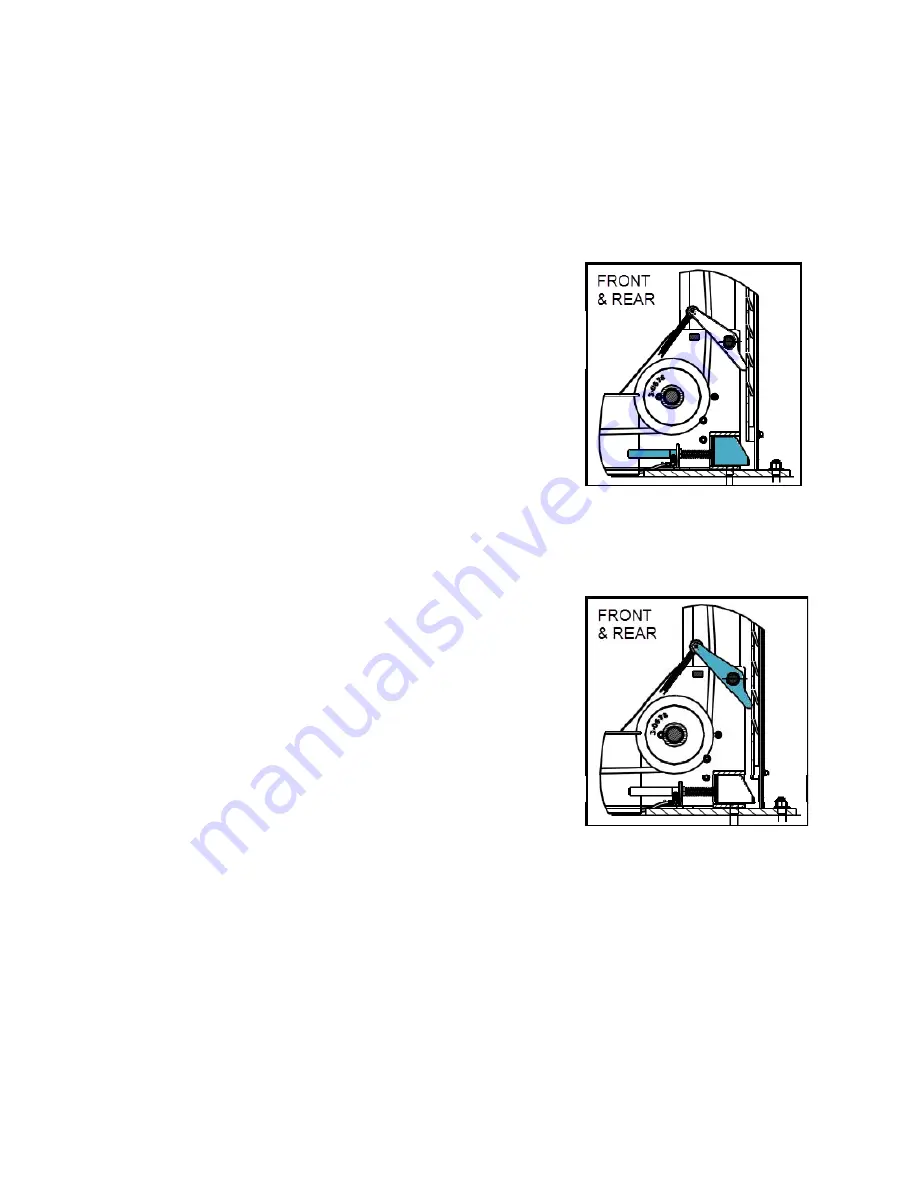
48 of 75
Fully raise the lift, to inspect sheaves in runways. Hold lowering handle down
to lower lift onto safety latches
Pull on cables in runway to create slack in cables.
Check all sheaves for excessive wobble, or movement. Grasp rim of sheave
and attempt to wobble (tilt) side to side. If sheaves wobble (tilt) more than 3/16”
(1.6 mm) side to side, or move in and out more than 1/32 (0.8 mm), the sheave
and sheave pin (shaft) should be replaced. Replace immediately if needed.
10.5.3 Sheave Pins
Sheave pins are held in place by a Hex Head Bolt,
washer and lock washer.
Check for loose sheave pins, loose or missing
fasteners to hold sheave pins in place. Remediate
situation immediately.
10.6 MECHANICAL SAFETY LATCH (DOG)
Watch and listen to safety latch operation during lift
operation, to ensure that latches move as required,
have not lost spring preload, and line up with slots
in latch plates (safety ladders) in columns.
Watch for broken traction springs on safety latches.
Check and adjust safety ladders if lift is not level on safety, or if safeties do not
engage properly. Stop using the lift if any malfunction or damage is observed.
10.7 AUXILIARY SAFETY MECHANISM
With lift not loaded, all four cable break levers should
produce deflection of the lift cables. Inspect slack cable
device as follows:
Check for missing or damaged parts.
Watch for broken springs. Check if the spring is
properly seated in the support tube and in the
holder on the cable break safety lever.
Watch cable tracking properly on cable break
safety roller.
Check if the safety roller and bolt are properly
attached to the cable break safety lever.
Verify that the cable break safety lever is centered within the cross-member, and
that it lines up with the openings in the safety ladder.
Verify using hand force or a light lever that the cable break safety lever pivots on
the shaft. Lubricate with light lubricant if required.
10.8 AIRCYLINDERS, AIR LINES, VALVES AND FITTINGS
10.8.1 General Checks
Check
filter/regulator/lubricator in supply line to lift. (customer supplied, typically
at compressor). Drain water trap filter bowl and adjust oil feed according to
manufacturer’s instructions.
Summary of Contents for Hofmann ALIGNMENT FPA18210
Page 8: ...8 of 75 SAVE THESE INSTRUCTIONS 2 1 SAFETY WARNING LABELS SAVE THESE INSTRUCTIONS...
Page 13: ...13 of 75 6 1 TYPICAL BAY LAYOUT Figure 2 Typical Bay Layout...
Page 15: ...15 of 75 Figure 3 Chalk line layout...
Page 44: ...44 of 75 10 2 MAINTENANCE RECORDS Maintenance and Training Performed Date By Notes...
Page 57: ...57 of 75 12 0 PARTS LIST 12 1 LIFT ASSEMBLY...
Page 59: ...59 of 75 12 3 TOWER ASSEMBLY...
Page 61: ...61 of 75 12 5 DECK ASSEMBLY LEFT SIDE...
Page 63: ...63 of 75 12 7 CROSSMEMBER ASSEMBLY...
Page 65: ...65 of 75 12 9 CYLINDER ASSEMBLY...
Page 67: ...67 of 75 12 11 HYDRAULIC AND AIR KIT...
Page 70: ...70 of 75 12 14CABLE ROUTING...