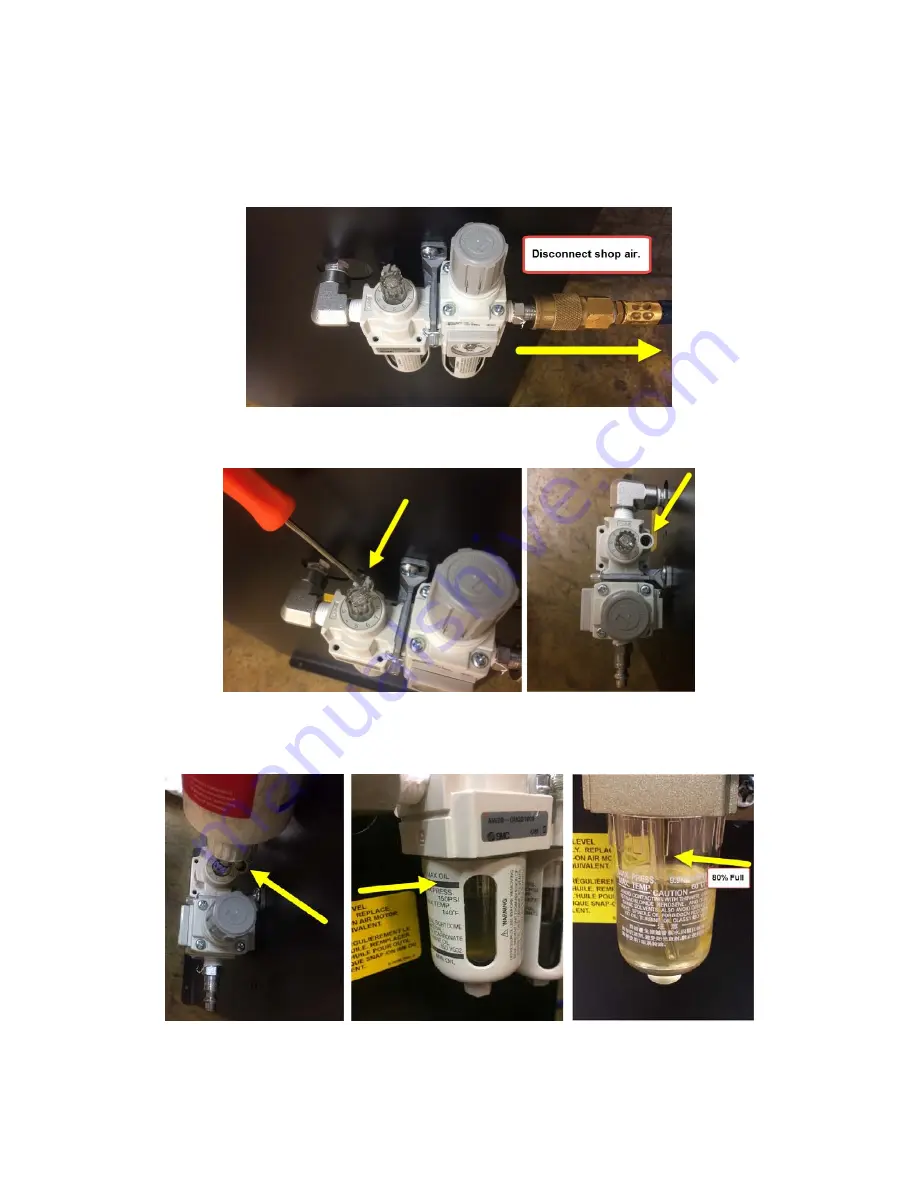
31 of 75
7.10 FILTER/REGULATOR/LUBRICATOR COMMISIONNING
PROCEDURE FOR PREPARING FRL FOR USE WITH LIFT
1. Disconnect shop air from FRL inlet. Adding Oil to the lubricator cannot take place
under a pressurized condition.
2. Using a slotted screwdriver or an Allen key, remove the filler cap from the top of the
FRL.
3. Fill FRL using Snap-On AirOil #IM6 or equivalent. Oil to be filled to the MAX line
marked on reservoir. If unit does not have MAX line mark, reservoir should be 80%
full.
4. Replace filler cap to top of FRL.
Summary of Contents for Hofmann ALIGNMENT FPA18210
Page 8: ...8 of 75 SAVE THESE INSTRUCTIONS 2 1 SAFETY WARNING LABELS SAVE THESE INSTRUCTIONS...
Page 13: ...13 of 75 6 1 TYPICAL BAY LAYOUT Figure 2 Typical Bay Layout...
Page 15: ...15 of 75 Figure 3 Chalk line layout...
Page 44: ...44 of 75 10 2 MAINTENANCE RECORDS Maintenance and Training Performed Date By Notes...
Page 57: ...57 of 75 12 0 PARTS LIST 12 1 LIFT ASSEMBLY...
Page 59: ...59 of 75 12 3 TOWER ASSEMBLY...
Page 61: ...61 of 75 12 5 DECK ASSEMBLY LEFT SIDE...
Page 63: ...63 of 75 12 7 CROSSMEMBER ASSEMBLY...
Page 65: ...65 of 75 12 9 CYLINDER ASSEMBLY...
Page 67: ...67 of 75 12 11 HYDRAULIC AND AIR KIT...
Page 70: ...70 of 75 12 14CABLE ROUTING...