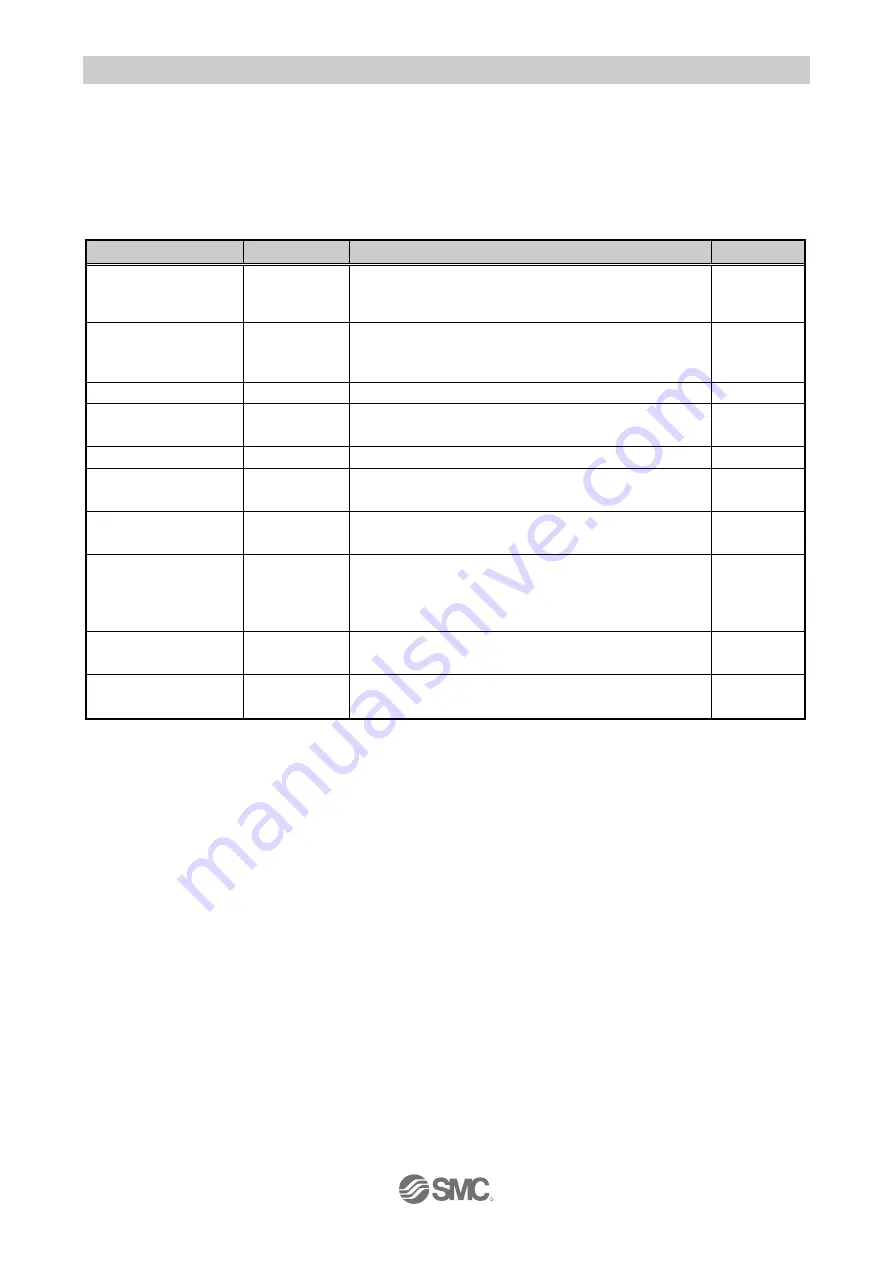
- 43 –
No.JXC
※
-OMY0002
7.3 Return to origin parameter
The "Return to origin parameter" is the setting data for the return to origin operation.
Details of Return to origin parameter
Activation: "XX" = Become effective just after recorded into the controller
"X" = Become effective after restarting the controller
"-" = The parameter cannot be changed (fixed value)
Parameter name
Range
Description
Activation
ORIG direction
1 to 2
Sets the direction of return to origin operation. Note1)
1. CW
2. CCW
X
Return to origin mode
*1)
The setting for the return to origin operation.
1: Pushing origin operation [Stop]
2: Limit switch origin [SW]
XX
ORIG limit
*1)
A pushing force level at which to set the origin.
XX
ORIG time
Fixed value
This is a fixed value for the controller.
(Do not change the setting)
-
ORIG speed
*1)
The allowable speed to move to origin.
XX
ORIG ACC/ DEC
*1)
The acceleration and deceleration during return to origin
operation.
XX
Creep speed
Fixed value
This is a fixed value for the controller.
(Do not change the setting)
-
ORIG sensor
*1)
The setting for the ORIG sensor.
0. The origin sensor is not effective. [Disable]
1. The origin sensor is N.O type. [N.O].
2. The origin sensor is N.C type. [N.C].
XX
ORIG SW DIR
Fixed value
This is a fixed value for the controller.
(Default value is "0")
-
Undefined parameter
No.21
Fixed value
This is a fixed value for the controller.
(Default value is "0")
-
*1)
The actuator model determines the available input values. Refer to the operation manual of the actuator for details.