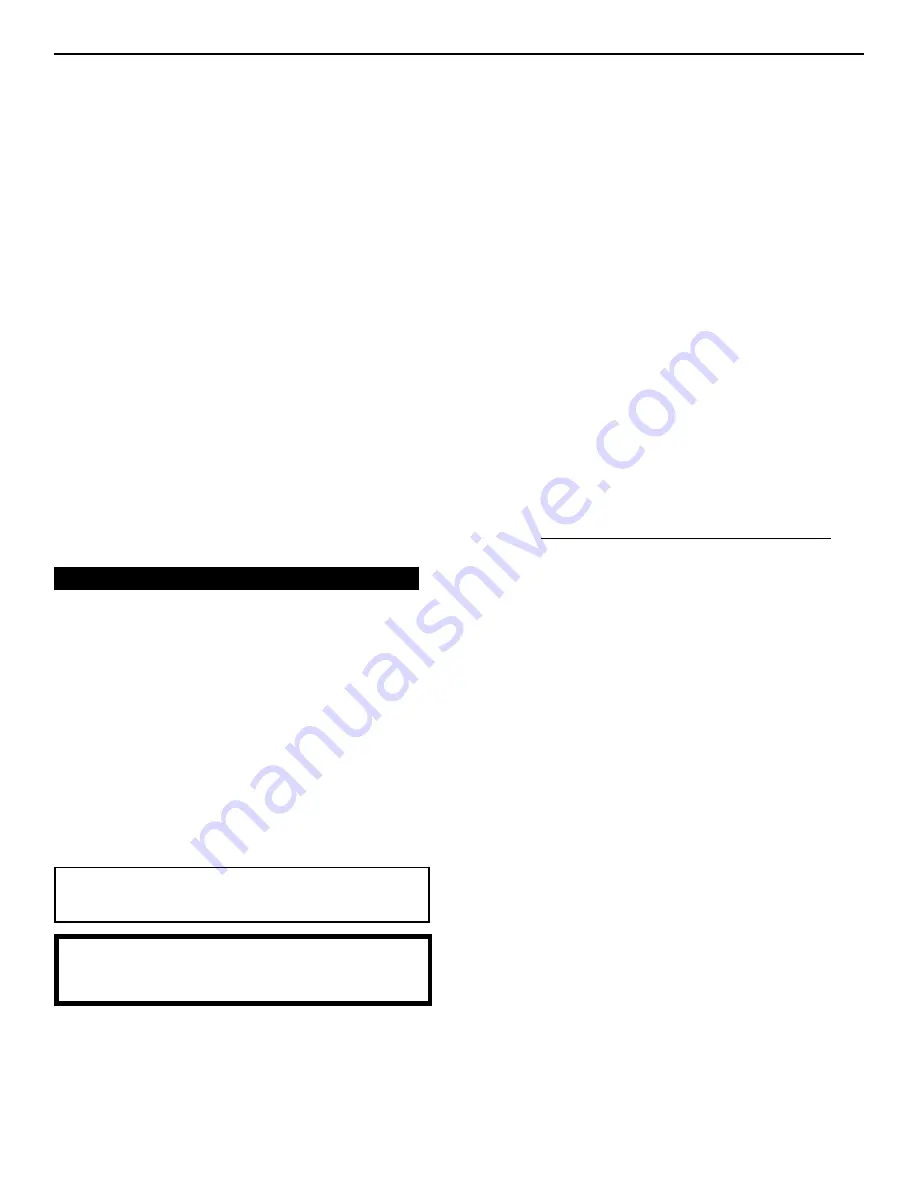
6
EUTECTIC EC-10 DV
CAUTION:
DO NOT USE GASOLINE, CRANKCASE
DRAININGS, OR ANY OIL CONTAINING GASOLINE.
OIL SUPPLY PIPING
Install the oil tank or tanks and piping from tank to burner. Follow local codes
and practices, NFPA No. 31, INSTALLATION OF OIL BURNING EQUIPMENT
and the instruction sheet attached to the oil burner pump. A one-pipe system
should be used for gravity fed fuel systems and for lift systems, where the
total lift is less than 8 ft. Where the total lift is greater than 8 ft., a two-pipe sys-
tem must be used. In some instances, local codes may require a two-pipe
system for below grade fuel oil tanks. Be sure to set-up the fuel oil pump for
the piping system used; follow the instructions attached to the pump. Be
sure to include a good quality, low pressure drop fuel oil filter in the supply
line from the tank. This is necessary, especially at low fuel oil flow rates
(small nozzle sizes), to prevent nozzle plugging.
WIRING THE BOILER
• The wiring diagrams for the burner and boiler may be found on pages 6-7.
• 24 volt control wiring should be approved Safety Circuit wire, protected
as needed.
• Power supply wiring to the burner must be 14 gauge or heavier, as
required, and should have a properly fused disconnect switch. 120 volt
wiring to pumps and safety controls must also be 14 gauge or heavier.
Wire must be enclosed in approved conduit.
• All wiring must be installed in compliance with the National Electric
Code, or any local or insurance codes having jurisdiction.
Wiring to the boiler must come through an emergency power
isolation switch with a clearly marked red switch plate. This
switch should be located so that it is apparent to the home-
owner when entering the basement or other boiler area. The
homeowner should be made familiar with operating the toggle
to provide or stop the power to the boiler.
PRECAUTIONS BEFORE STARTING OIL BURNER
Make a positive check of A through I before starting burner:
A. Boiler and system are full of water. All air is vented from system.
See below.
B. All wiring is completed. See pages 7-8.
C. Oil supply is connected to the burner; nozzle is installed correctly; oil
valve is open at tank.
D. All combustible materials are cleared away.
E. All vent piping is properly installed and sealed.
F. Burner settings are adjusted as per pages 9 & 10 and as shown on
boiler jacket label.
G. Main cast iron door on which burner is mounted is bolted shut and
fiberglass rope seal is making good contact.
H. Make sure boiler has correct quantity of baffles (see top of pag 3).
I.
Make sure vent pipe, vent terminal and air supply pipe are properly
installed and clear of obstruction.
Note: Neither overfire nor flue draft should exceed
8.9mm (0.35") WC during burner operation
THE FLUE IS UNDER POSITIVE PRESSURE DURING
OPERATION. ALL VENTING MUST BE SEALED AND
CHECKED ON A REGULAR INTERVAL.
OPERATING INSTRUCTIONS
CLEANING AND FILLING A NEW WATER BOILER
I. BEFORE FILLING WATER BOILER
A.
Check burner to be certain it is ready for firing. DO NOT FIRE
into an empty boiler.
B.
Be prepared to heat raw water to at least 82°C (180°F) as soon as it is
introduced into the boiler. This procedure will remove dissolved,
corrosive gases.
C. Provide drain line, with valve, from boiler. Use a bottom tapping.
Line and drain must be suitable for handling caustic solution.
II. CLEANING WATER BOILER SYSTEM
A.
Use a commercial cleaning solution, such as
Rhomar Hydro-Solv
9100 Cleaner
as directed in product instructions.
B.
Use a commercial treatment solution, such as
Rhomar Pro-Tek 922
Treatment
as directed in product instructions.
III. FILLING AND VENTING THE WATER BOILER
A.
Refill the system with fresh water.
B.
Bring water temperature to at least 82°C (180°F) promptly.
C. Circulate water through entire system.
D. Vent the system, including the radiation.
E. The boiler is now ready to be put into service or on standby.
F.
If brand-name air-control devices are used, venting instructions
furnished with the devices should be followed.
IV. SAFETY CHECK FOR CONTROL SYSTEM
High limit control test: Set thermostat high enough for boiler water
temperature to reach high limit control setting. When this temperature is
reached, the high limit switch should open, and the burner should shut off
automatically. If the high limit does not operate to shut off the burner, the
high limit or the wiring is faulty. Repair or replace immediately.
START-UP
(COMBUSTION TEST INSTRUMENTS MUST
BE USED)
THIS BOILER IS A POSITIVE PRESSURE BOILER
.
A. Make sure the boiler is installed and wired properly and is full
of water.
B. The observation port cover is mounted on the hinged burner
mounting door. NEVER touch the port cover or any surrounding
surfaces with hands. They may be HOT. Use tools. Loosen the
screw and swing cover to be able to insert probe through slot,
when necessary. See the burner instructions for bleeding air, etc.
C. Take a smoke reading soon after starting burner. If smoke is not
zero or trace, open air to clear smoke and let burner fire.
D. DO NOT ATTEMPT TO SET FIRE BY EYE. A smoke gun and a
combustion analyzer must be used. Adjust the air to get approxi-
mately 12% CO
2
with a zero or trace smoke. Then check and
record draft and flue temperature.
E. Make sure that the observation port cover is closed tight, the
burner is secure. Turn burner on and off at least 3 times to
check ignition.