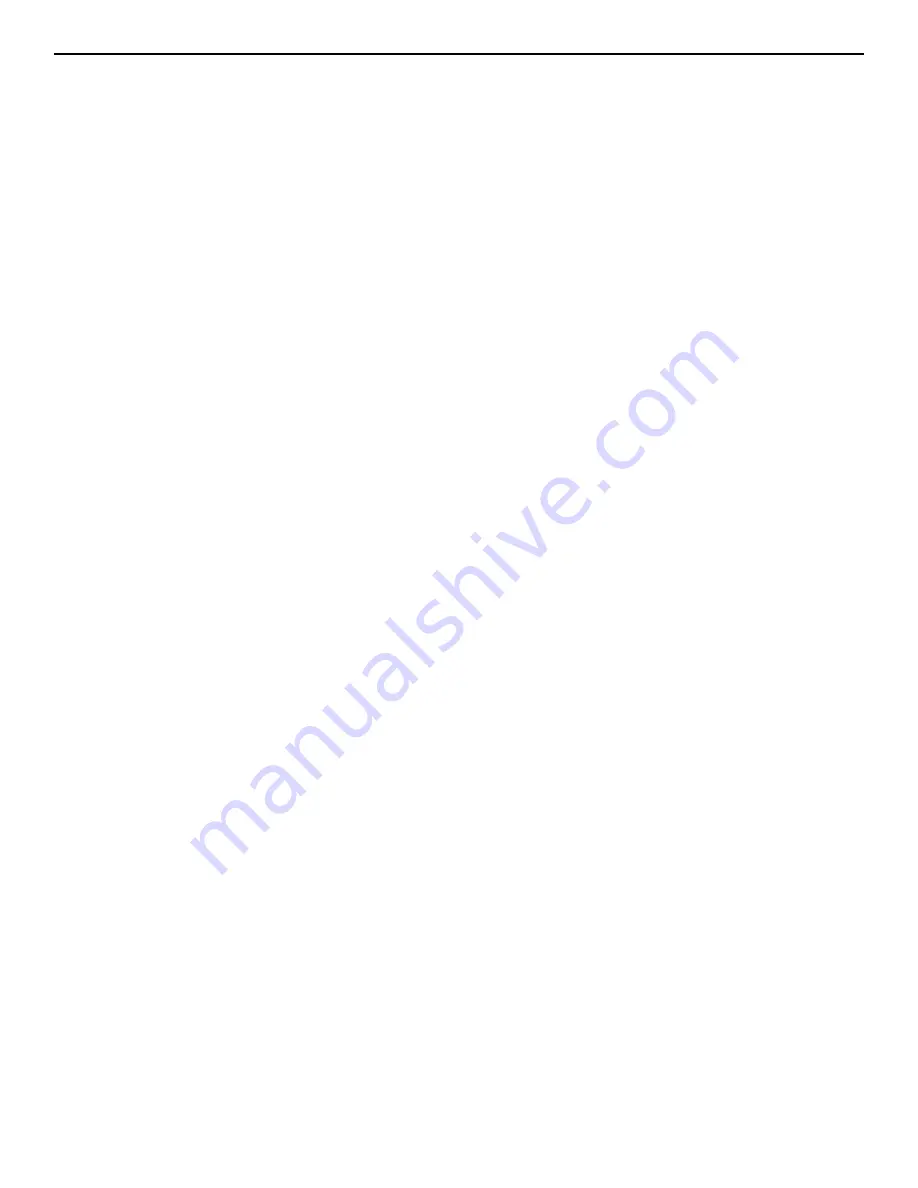
EUTECTIC EC-10 DV
12
CARE AND MAINTENANCE
I. EXTENDED SHUTDOWN, CLEANING OR REMOVAL OF
BOILER FROM SERVICE.
DANGER: Use CAUTION when handling chemicals and
draining hot water from a boiler. Scalding water and/or
chemicals can cause permanent injury to the skin, eyes and
respiratory system.
A.
Shut down burner by disconnecting all electrical power
to the burner by turning OFF the BURNER
EMERGENCY SWITCH of this boiler. After shutting
down burner, while the boiler is still hot [82°C to 93°C
(180°F to 200°F)], drain water from the bottom of the
boiler until it runs clear.
B.
Provide corrosion protection conditioning to the boiler
water in the heating system. There are a number of
commercial heating system preparations available from
your distributor. Follow the preparation manufacturer’s
instructions.
II CLEANING OF BOILER
1. To clean the fireside boiler surfaces, first shut down burner
by disconnecting all electrical power to the burner by
turning OFF the OIL BURNER EMERGENCY SWITCH of this
boiler in order to perform the following in (a) through (h)
below.
a.
Remove the flue pipe from the boiler flue collar clean
thoroughly.
b.
Inspect the entire vent connector back to the chimney
and clean if necessary.
c.
Inspect the chimney for soot, debris and other unsafe
conditions of the chimney and take the necessary
action.
d.
Remove the boiler jacket front panel to open burner
door as follows:
1. Lift the window.
2. Unscrew the two front panel side attachment screws.
3. Unclip the front panel from the clips and notches
near the top, and pull it towards you.
4. Remove the front panel from the notches in the
bottom of the side panels.
e.
The burner mounting door must be fully open to clean
the flue passages and the combustion chamber. If the
oil line is not flexible enough it should be disconnected
from the burner during the cleaning process. The
flexible electric conduit connected from the junction
box on the boiler to the burner via a plastic connector
must be disconnected from the burner by grasping the
plastic half of the connector closest to the flexible
conduit and gently pulling it in the direction of the
conduit until it is disconnected. Remove all four 13 mm
hex head screws on the sides of the swinging door.
You will need a 13 mm open end or box wrench. Open
the door to completely expose the combustion
chamber for thorough cleaning and for inspection of
main cast iron burner door insulation and burner door
fiberglass sealing rope .If combustion chamber parts
above are badly deteriorated then replace with original
factory parts available at your distributor.
f.
Use the flue brush to clean the flue passages and
combustion chamber.
Remove cast iron baffle plates for cleaning [2 baffle
plates in ECDV-13 to 0 baffle plates in ECDV14, 15 &
16]. A wire brush may be used to remove any carbon
accumulation that may have developed in the
combustion chamber. Vacuum the loose soot and
debris from the boiler. Clean and replace baffle plates.
Inspect the burner combustion head. Clean if
necessary and make sure all the adjustments are
correct (See burner data pages for the burner
installed). Replace oil nozzle with the new one and re-
adjust electrodes. To insure proper burner operation
ONLY THE NOZZLES SPECIFIED IN THIS MANUAL OR
ON THE BURNER LABEL SHOULD BE USED FOR
REPLACEMENT.
g.
Close main cast-iron burner door (door on which
burner is mounted). Make sure that the entire seal
(fiberglass rope) is making good contact with the boiler
casting when replacing the four 13 mm hex head
screws and tightening.
h.
Replace boiler jacket front panel.
2. If boiler room is damp, provide ventilation.
CAUTION:
ALWAYS KEEP THE OIL SUPPLY VALVE SHUT OFF
IF THE BURNER IS SHUT DOWN FOR AN EXTENDED PERI-
OD OF TIME
II. PROVIDING PROTECTION FOR FREEZING
Anti-freeze is sometimes used in hydronic heating systems
to protect against freeze-up in the event of power failure, or
safety control shutdown when the building is unoccupied. It
should be recognized that unless the building is kept above
freezing temperature by some means, the plumbing system
is not protected.
PROPYLENE GLYCOL is used in the quick-freeze food
industry; it is practically non-toxic. Its use may be permitted
when indirect water heaters are used. When anti-freeze must
be used, inhibited propylene glycol is recommended. Useful
information on the characteristics, mixing propor tions, etc. of
glycol in heating systems is given in Technical Topics No.
2A, available from the Hydronics Division of GAMA, 35
Russo Place, Berkeley Heights, NJ 07922. Consult glycol
manufacturers for sources of propylene glycol.
DO NOT USE ETHYLENE GLYCOL BECAUSE IT IS TOXIC.
III. OIL BURNER
All service to the oil burner, oil filter, oil strainer, etc., should
be performed by a professionally trained service person.
Inspect and clean annually and following any period of
improper operation. Recheck and adjust settings as
specified for burner model and nozzle size.
Set burner air using test instruments to obtain recommend -
ed CO2 and draft without smoke. See the Burner Data page
in this manual that corresponds to the burner installed.
IV. GENERAL MAINTENANCE
These operations are recommended to be performed at
regular intervals:
A.
BOILER HEATING SURFACES: clean off all coatings
found. Reseal covers.
B.
BOILER CONTROLS: check settings, correct
functioning.
C.
PIPING: check piping and accessories for leaks.
D.
STUB VENT and BREECHING: check for obstructions
and leaks.
E.
COMBUSTION AIR TO BURNER: check for continued
POSITIVE supply of air as required. Air needs are
greatest in coldest weather. Refer to AIR SUPPLY,
page 3.
F.
WATER SYSTEM: check
1.
System to be full of water and pressure to remain
stable (between 83 kPa and 172 kPa [12 psi and
25 psi]).
2.
Air-control system: noise and air binding in
radiation should not occur.
3.
Water lines: slightest leaks should be corrected.
G.
BOILER ROOM AIR SUPPLY: air vents should be open
and free of obstruction.