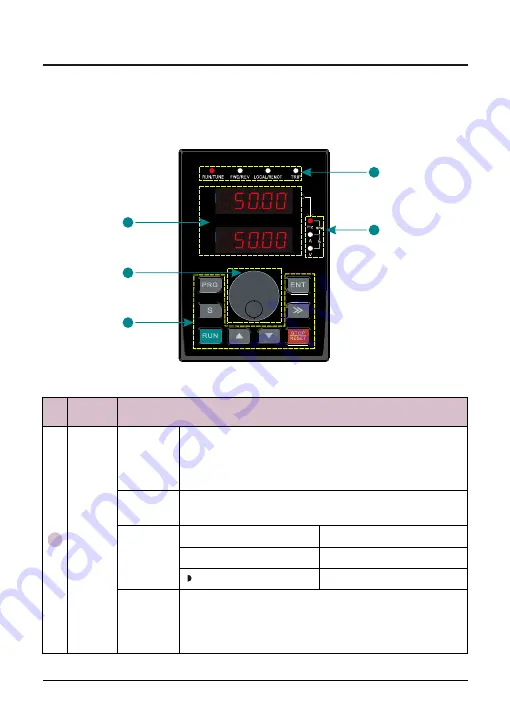
16
Chapter 3 Operation And Display
3.1 Introduction of the keypad
The keypad is used to control SD95H series AC drive, read the state data and
adjust parameters.
Figure 3-1 Keypad diagram
1
2
4
5
3
Name
No.
Status
indicator
Instructions
LED off means that the AC drive is in the stopping state;
LED blinking means the AC drive is in the parameter
autotuning state;
LED on means the AC drive is in the running state.
RUN/TUNE
OFF means the AC drive is in the forward rotation state
ON means the AC drive is in the reverse rotation state.
FWD/REV
LOCAL/
REMOT
Operation
panel
control
Terminal
control
Communication
control
○
LOCAL/REMOT: OFF
●
LOCAL/REMOT: PN
○
LOCAL/REMOT: Flash
TRIP
LED for faults
LED on when the AC drive is in the fault state;
LED off in normal state
LED blinking means the AC drive is in the pre-alarm state.
1