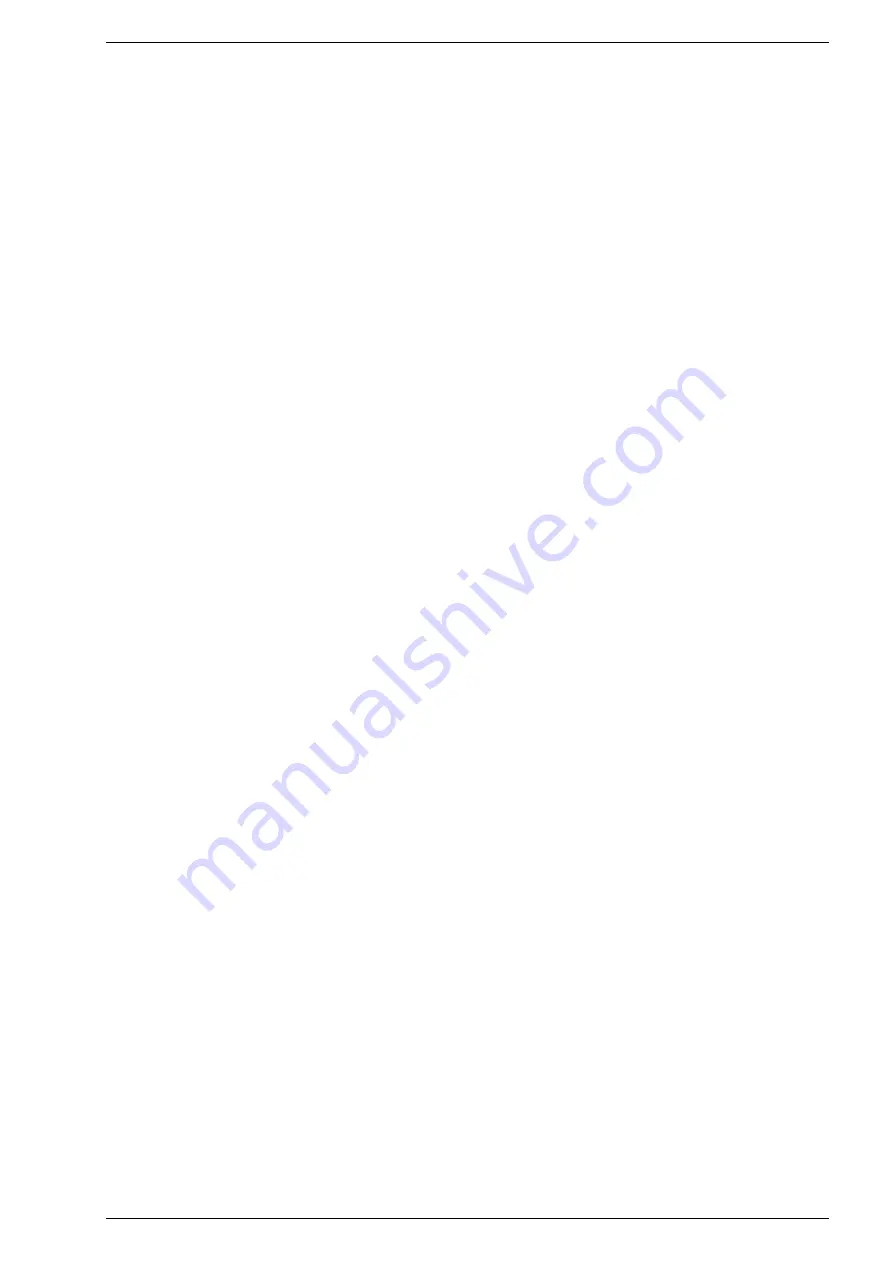
The boiler should be installed in a fixed
location and shall be carried out only by
specialized and qualified firms in com-
pliance with all national and local regu-
lations in force and following the
instructions contained in this manual.
In addition this appliance must be
installed in accordance with the Local
Gas Region regulations.
2.1
CONNECTING UP SYSTEM
The system must be connected up
using rigid pipe connections such as to
avoid any stresses being exerted on
the appliance. The connections should
be easy to disconnect using pipe
unions with orientable connections.
You are recommended to install suita-
ble shutoff valves on the system flow
and return pipes.
In order to achieve a good water
distribution inside the cast-iron body,
the system flow and return pipes
should be connected to the same side
of the boiler.
The boiler comes supplied standard
with the attachments on the right-hand
side, with the possibility of them being
transferred to the left-hand side by
moving the flanges provided with col-
lars and the corresponding water
distributors (models
“RS 6-7”
are
without a water distributor). The ther-
mal jump between the system flow and
return pipes should not exceed 20°C.
For this purpose, it is advisable to
install a mixer valve with correspon-
ding anti-condensation pump.
CAUTION: The system circulation
pump or pumps must go into action at
the time of boiler ignition. For this pur-
pose, you are recommended to use an
automatic system of precedence.
The gas connection must be made
using
seamless
steel
tubes
(Mannesmann type), galvanized and
with threaded joints provided with
gaskets, excluding three-piece connec-
tions, except for initial and end con-
nections.
Where the piping has to pass through
walls, a suitable insulating sleeve must
be provided. When sizing gas piping,
from the meter to the boiler, take into
account both the volume flow rates
(consumption) in m
3
/h and the relative
density of the gas in question.
The sections of the piping making up
the system must be such as to gua-
rantee a supply of gas sufficient to
cover the maximum demand, limiting
pressure loss between the gas meter
and any apparatus being used to not
greater than:
– 1.0 mbar for family II gases (natu-
ral gas)
–2.0 mbar for family III gases (butane
or propane).
An adhesive data plate is stuck on the
inside of the outer casing; it contains all
the technical data identifying the boiler
and the type of gas for which the boiler
is arranged.
2.1.1
Filter on gas pipe
To prevent malfunctioning of the valve,
or in certain cases even cutting out of
the safety devices with which the valve
is equipped, install an adequate gas fil-
ter on the boiler gas pipe inlet.
50
2
INSTALLATION
1.4
SHIPMENT
The
“RS”
heating units are supplied in
three separate packagings, as follows:
PACKAGE 1
Cast-iron body resting on a pallet com-
plete with:
–2 flanges with 2” collars for system
flow and return;
–1 blind flange;
–1 flange with 3/4” attachment for
drain cock;
–2 doors for combustion chamber,
each provided with inspection door
made of cast iron;
–2 sheaths for thermostats and
thermometer;
–1 water distributor located in boiler
return manifold, supplied in two dif-
ferent lengths:
L = 406 mm for models
“RS 8÷10”
;
L = 851 mm for models
“RS 11÷14”
.
Models
“RS 6-7”
are without a
water distributor.
PACKAGE 2
Wooden case including:
–smoke chamber to be assembled;
– cardboard box containing outer casing;
–main burners (quantity correspon-
ding to number of sections of body,
less one);
–manifold for burners, complete with
blind flange and flange with connec-
ting pipe;
–plastic bag containing:
• 13 M5 x 8 screws for fastening
burners to manifold ;
• 32 12E x 1/2” self-tapping screws
to join together the various parts
of the smoke chamber and the
outer casing;
• 4 M8 x 30 screws with plate, plain
washer and M8 nut for fastening
smoke chamber to boiler body;
• 3 M12 x 25 screws with M12 nuts
for fastening flange with connec-
ting pipe to burner manifold;
• 1 3/4” drain cock complete with plug.
PACKAGE 3
Cardboard box containing:
–gas unit consisting of:
• main gas valve provided with coil
assembly;
• gas pressure switch;
• pressure intake;
• second gas solenoid valve;
–electric control board consisting of:
• control equipment: BRAHMA SM
191.1 programmer;
• two-stage regulating thermostat;
• manual resetting safety thermostat;
• thermometer;
• gas pressure warning light;
• ignition and sensing electrodes;
• main switch with built-in light.
Summary of Contents for RS 10
Page 1: ...RS IT ES GB PT...