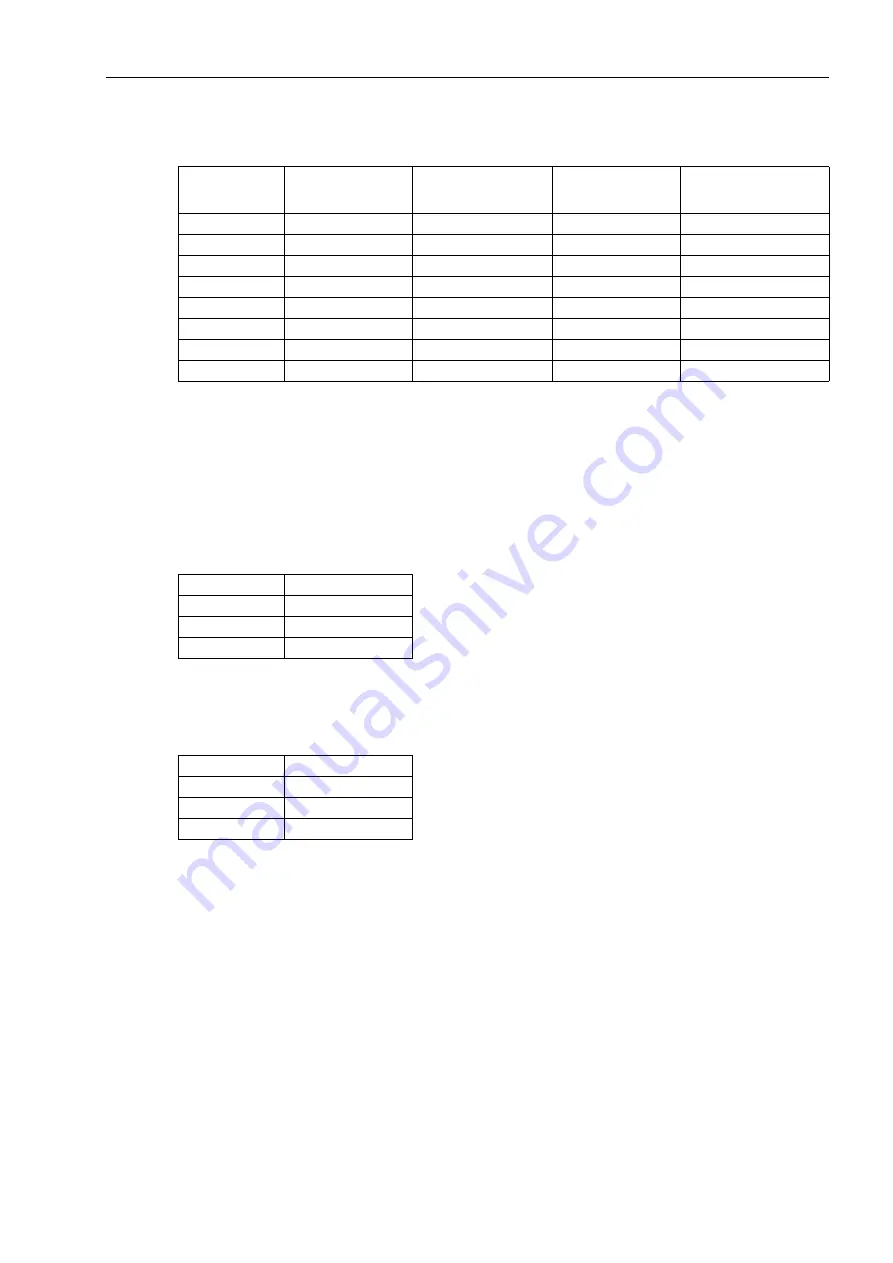
Mounting And Commissioning
3.1 Mounting And Connections
SIPROTEC, 7VU681, User Manual
C53000-G1176-C368-1, Release Date 07.2012
69
Table 3-9
Jumper setting of pickup voltages of binary inputs BI8 to BI15 on Input/Output module module
C- I/O-1 in the 7VU681
1)
Factory settings for devices with rated power supply voltages of 24 VDC to 125 VDC
2)
Factory settings for devices with power supply voltages of 110 VDC to 250 VDC and 115/230 VAC
3)
Use only with control voltages 220 to 250 VDC
Jumpers X71, X72 and X73 on the input/output module C-I/O-1 are used to set the bus address and must not
be changed. The following table lists the jumper presetting.
Mounting locations of modules are shown in Figures 3-2.
Table 3-10
Module address jumper setting of input/output module C-I/O-1 for 7VU681
Jumpers X71, X72 and X73 on the input/output board C-I/O-10 are used to set the bus address and must not
be changed. The following Table lists the jumper presettings.
Table 3-11
Jumper settings of PCB Address of the input/output board C-I/O-10
Binary inputs
Jumper
17 VDC Threshold
73 VDC Threshold
154 VDC Threshold
BI8
X21/X22
L
M
H
BI9
X23/X24
L
M
H
BI10
X25/X26
L
M
H
BI11
X27/X28
L
M
H
BI12
X29/X30
L
M
H
BI13
X31/X32
L
M
H
BI14
X33/X34
L
M
H
BI15
X35/X36
L
M
H
Jumper
Presetting
X71
2-3(L)
X72
2-3(L)
X73
1-2(H)
Jumper
Presetting
X71
2-3(L)
X72
2-3(L)
X73
1-2(H)
Summary of Contents for SIPROTEC 7VU681
Page 8: ...Preface SIPROTEC 7VU681 User Manual C53000 G1176 C368 1 Release Date 07 2012 8 ...
Page 12: ...Contents SIPROTEC 7VU681 User Manual C53000 G1176 C368 1 Release Date 07 2012 12 ...
Page 100: ...Literature SIPROTEC 7VU683 User Manual C53000 G1176 C368 1 Release Date 07 2012 100 ...
Page 112: ...Index SIPROTEC 7VU681 User Manual C53000 G1176 C368 1 Release Date 07 2012 112 ...