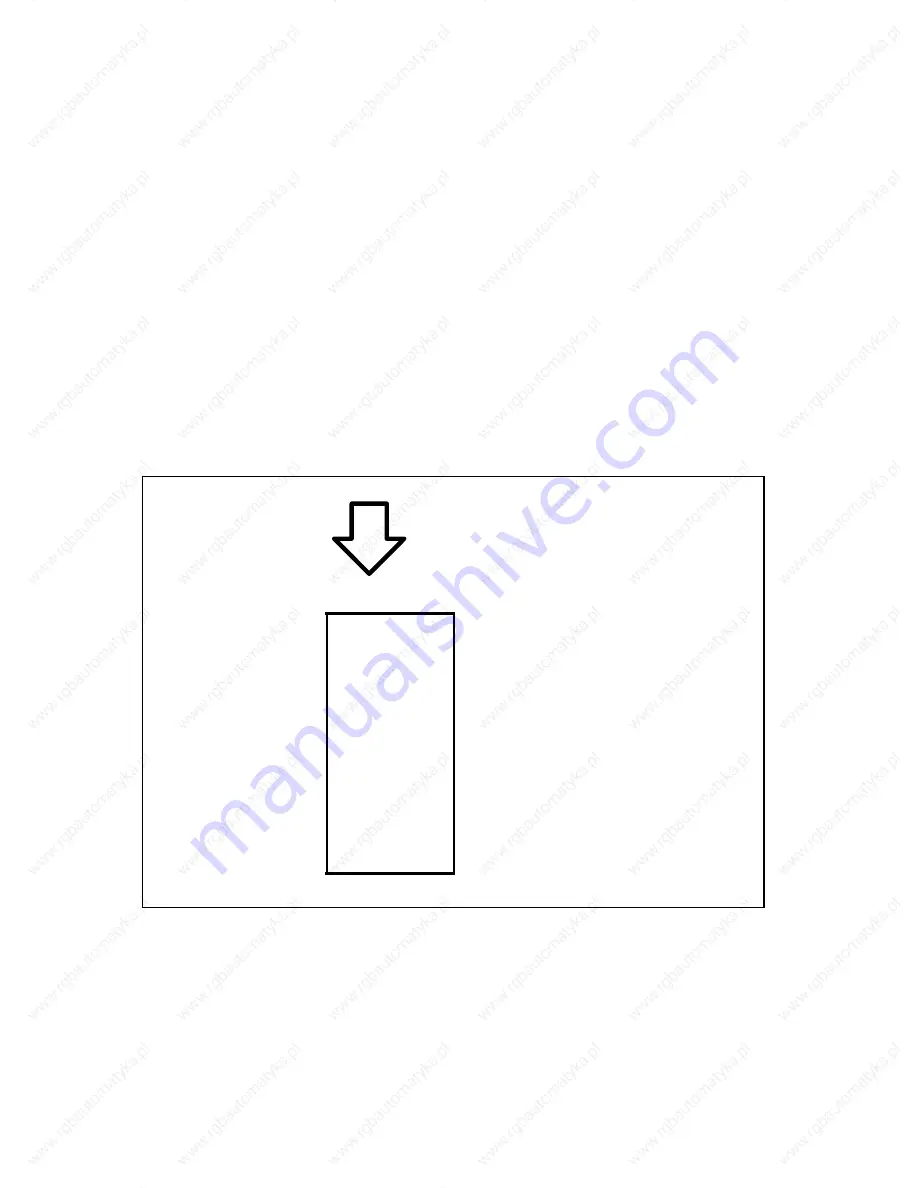
05.91
11 Data Transfer PLC/NC/COM (DB 36)
11.2.1 Structure and signal path
Speed of data transfer
The PLC operating system can transfer a value to the NC or read an NC value every 20 ms. If
two PLCs are installed, a value is transferred alternately from PLC I and PLC II, so that value
transfer takes place only every 40 ms per PLC.
Example:
Transfer of 6 values to the NC (with 1 PLC):
a) With a PLC cycle time of 50 ms, a new job cannot be executed until after 4 PLC cycle
times = 200 ms at the earliest.
b) With a PLC cycle time of 250 ms, a new job can be executed after 1 PLC cycle time =
250 ms.
If the function blocks are incorrectly parameterized (e.g. data source in the PLC unknown), the
PLC branches into the stop loop. The number of the interface byte and an error ID are stored
in accu 2 of the interrupt stack.
Examples of parameterization of FB 61
The figure below shows the parameterization of FB 61 for reading the "machine-oriented
actual axis value" of the 3rd axis (data type ACPM). The actual value is to be stored in DB 150
in data words 10, 11 and 12.
Example:
Reading actual axis value with FB 61
FB 61 NCD-READ
a a a a a a a a a a a a a a
a a a a a a a a a a a a a a
a a a a a a a a a a a a a a
a a a a a a a a a a a a a a
a a a a a a a a a a a a a a
a a a a a a a a a a a a a a
a a a a a a a a a a a a a a
a a a a a a a
a a a a a a a
a a a a a a a
a a a a a a a
a a a a a a a
a a a a a a a
a a a a a a a
a a a a a a a
PLC
M150.0
–
LESE
16
–
NSBY
1 –
ANZ
AC –
DTY1
PM –
DTY2
–
DTY3
3 –
WER 1
0 –
WER 2
0 –
WER 3
B0 –
ZFPN
150 –
DBZI
10 –
DWZI
DB –
TYZI
Function:
Actual value of axis 3 is transfer-
red in DB 150 into DW 10, 11 and
12
(BCD number without decimal
point)
© Siemens AG 1991 All Rights Reserved 6ZB5 410-0HE02
11–7
SINUMERIK 880 (PJ)