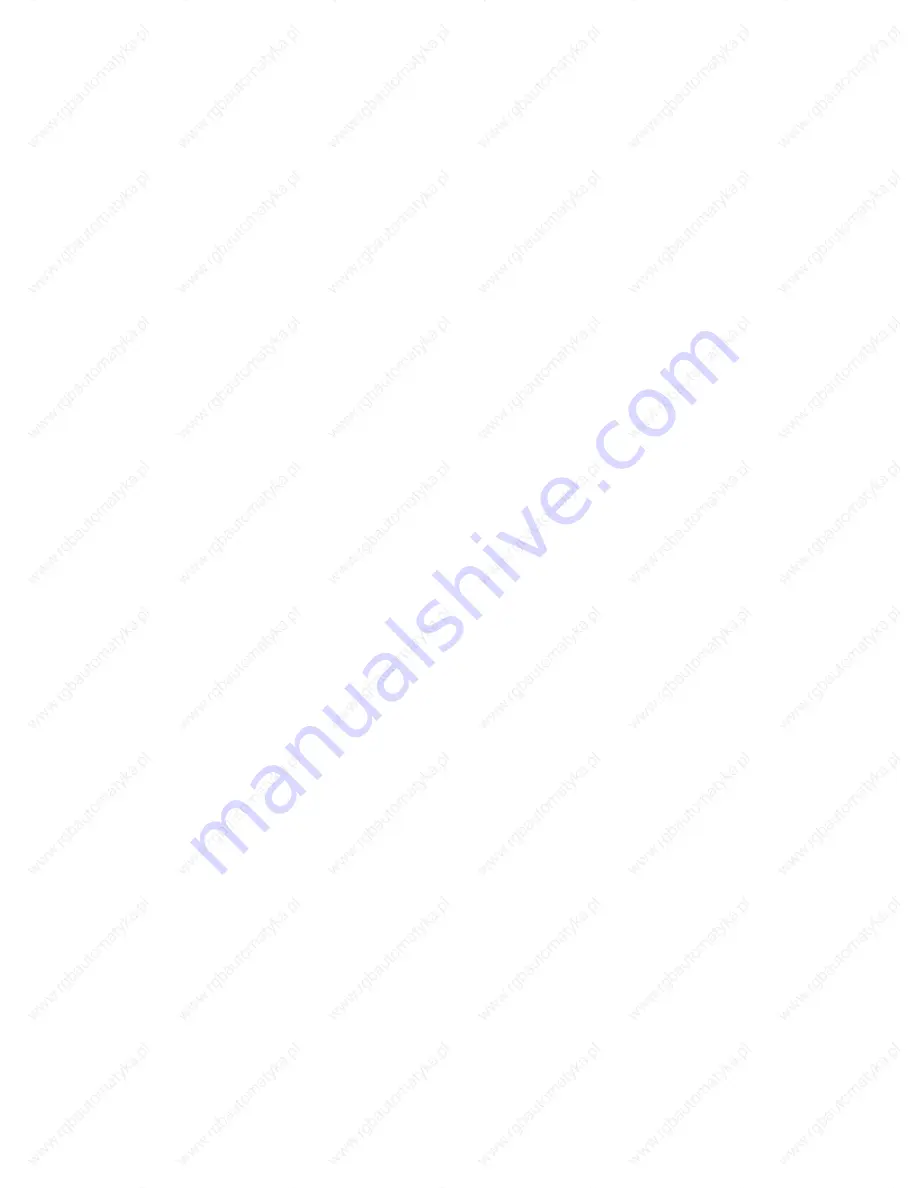
8 Spindle/PLC Interface (DB 31)
01.93
8.2 Signals from spindle
a a a a a a a a a a a a a a a a a a a a a a a a a a a a a a a a a a a a a a a a a a a a a a a a a a a a a a a a a a a a a a a a a a a a a a a a a a a a a a a a a a a a a a a a a a a a a a a a a a a a a a a a a a a a a a a a a
a a a a a a a a a a a a a a a a a a a a a a a a a a a a a a a a a a a a a a a a a a a a a a a a a a a a a a a a a a a a a a a a a a a a a a a a a a a a a a a a a a a a a a a a a a a a a a a a a a a a a a a a a a a a a a a a a
a a a a a a a a a a a a a a a a a a a a a a a a a a a a a a a a a a a a a a a a a a a a a a a a a a a a a a a a a a a a a a a a a a a a a a a a a a a a a a a a a a a a a a a a a a a a a a a a a a a a a a a a a a a a a a a a a
a a a a a a a a a a a a a a a a a a a a a a a a a a a a a a a a a a a a a a a a a a a a a a a a a a a a a a a a a a a a a a a a a a a a a a a a a a a a a a a a a a a a a a a a a a a a a a a a a a a a a a a a a a a a a a a a a
a a a a a a a a a a a a a a a a a a a a a a a a a a a a a a a a a a a a a a a a a a a a a a a a a a a a a a a a a a a a a a a a a a a a a a a a a a a a a a a a a a a a a a a a a a a a a a a a a a a a a a a a a a a a a a a a a
a a a a a a a a a a a a a a a a a a a a a a a a a a a a a a a a a a a a a a a a a a a a a a a a a a a a a a a a a a a a a a a a a a a a a a a a a a a a a a a a a a a a a a a a a a a a a a a a a a a a a a a a a a a a a a a a a
a a a a a a a a a a a a a a a a a a a a a a a a a a a a a a a a a a a a a a a a a a a a a a a a a a a a a a a a a a a a a a a a a a a a a a a a a a a a a a a a a a a a a a a a a a a a a a a a a a a a a a a a a a a a a a a a a
a a a a a a a a a a a a a a a a a a a a a a a a a a a a a a a a a a a a a a a a a a a a a a a a a a a a a a a a a a a a a a a a a a a a a a a a a a a a a a a a a a a a a a a a a a a a a a a a a a a a a a a a a a a a a a a a a
a a a a a a a a a a a a a a a a a a a a a a a a a a a a a a a a a a a a a a a a a a a a a a a a a a a a a a a a a a a a a a a a a a a a a a a a a a a a a a a a a a a a a a a a a a a a a a a a a a a a a a a a a a a a a a a a a
CHANGE GEAR
DW K, bit 7
1 signal:
Request to PLC to change to new set gear stage.
0 signal:
No gear stage change requested.
Notes:
•
The signal is output if the programmed S value is outside the speed range of the current
actual gear stage and a new set gear stage could be determined.
The speed ranges are determined by:
– MD 403* to MD 410*
"Maximum speed" for each gear stage
– MD 411* to MD 418*
"Minimum speed" for each gear stage
•
Once the gear change has been made the signal has to be reset by the PLC user program
and the new actual gear stage has to be entered in the interface.
•
The speed ranges are checked only if a new S value has been specified. The PLC user
program can therefore also acknowledge the gear stage change (reset CHANGE GEAR
interface signal) without having changed the gear stage if required.
•
MD 521*, bit 5 "New S value after PLC acknowledgement" determines whether the spindle
is to assume the set speed until the gear stage change has been acknowledged.
•
If the gear stage change is triggered directly by the NC part program (M 41 ... M 48,
decoding by PLC user program), the CHANGE GEAR interface signal cannot be evaluated
until the LAST INFORMATION interface signal is also present.
•
The signal also has to be reset and the new actual gear stage entered in the interface if
the gear stage is selected by M 41 ... M 48.
•
The change limits are allowed to overlap.
•
CHANGE GEAR is output only if the "Signals from/to spindle" PLC MD (PLC I: MD 6012,
PLC II: MD 6112) is set and the relevant PLC is declared in NC MD 5038.
•
If dual PLCs are used and the "trace spindle signals" function is activated
(PLC I MD 6014, PLC II MD 6114), the PLC user program must reset the signal "CHANGE
GEAR" in both PLCs.
8
–
10
©
Siemens AG 1991 All Rights Reserved 6ZB5 410-0HE02
SINUMERIK 880 (PJ)