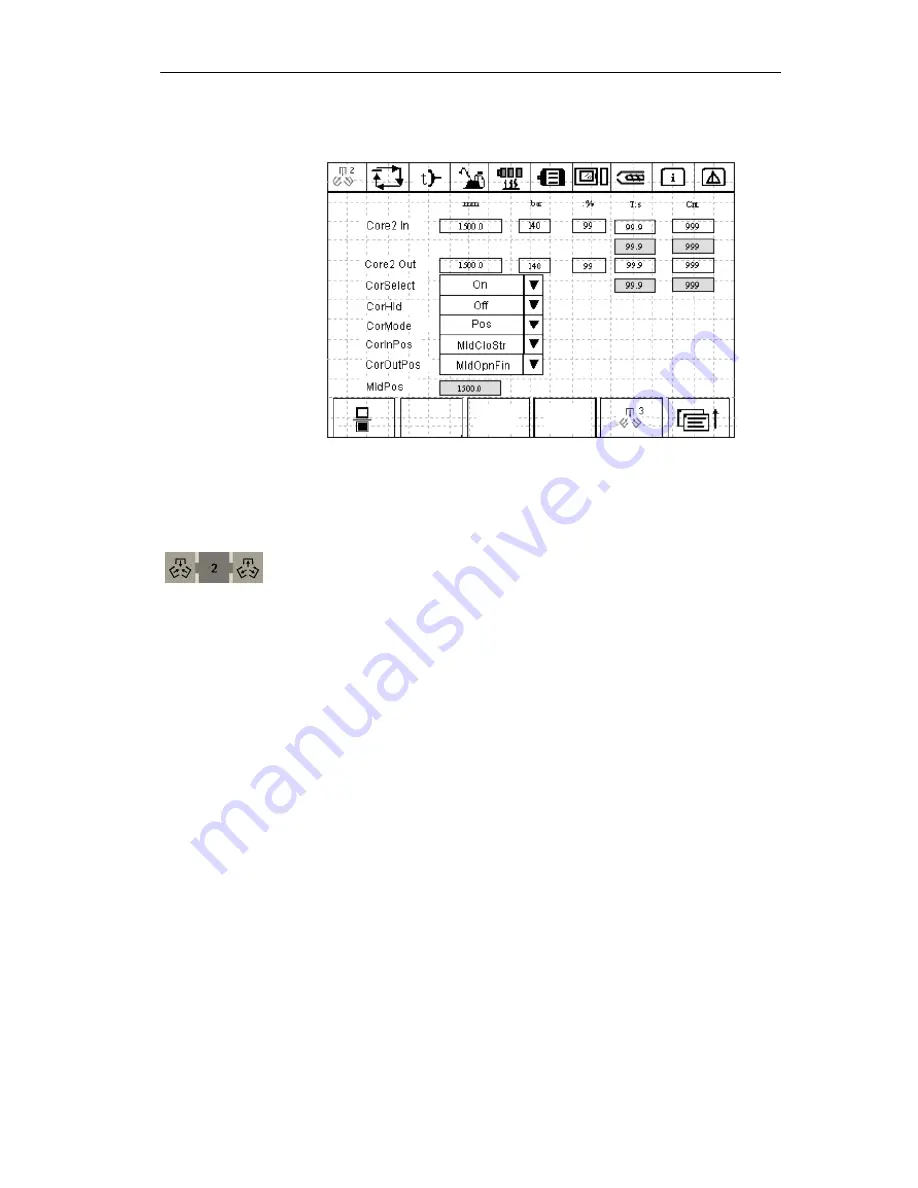
SIJECT OP15B Screens
SIJECT 15/16 Operation Manual June, 2003
3-50
3.2.7 Core 2 screen
Fig 3-38
Core 2 in/out --- screen 1
Operating sequences
Press the Core 2 key to enter Core 2 screen. See Fig 3-38.
The screen displays the core 2 in/out status, and the related parameters
can be set here, including the position, pressure, flow, time and counter.
The core operation can be controlled by position, by time, or by counter.
Core 2 in
-
set the pressure and flow for core 2 in. If it is by position,
then position value should be set. If it is by time, then the time should be
set as a parameter and the actual time will be displayed. If it is be
counter, then the counter should be set and the actual counting value will
be displayed.
Core 2 out
-
set the pressure and flow for core 2 out. If it is by position,
then position value should be set. If it is by time, then the time should be
set as a parameter and the actual time will be displayed. If it is be
counter, then the counter should be set and the actual counting value will
be displayed.
Core 2 selection (CorSelect)
-
select or deselect core 2 in/out.
Core 2 mode (CorMode)
-
select position mode, time mode or counter
mode.
Core in position (CorInPos)
-
set the position to do core in. The core
in can be at the start of mold close, during mold close, or at the end of
mold close.
Core out position (CorOutPos)
-
set the position to do core out. The
core out can be at the start of mold close, during mold close, or at the
end of mold close.