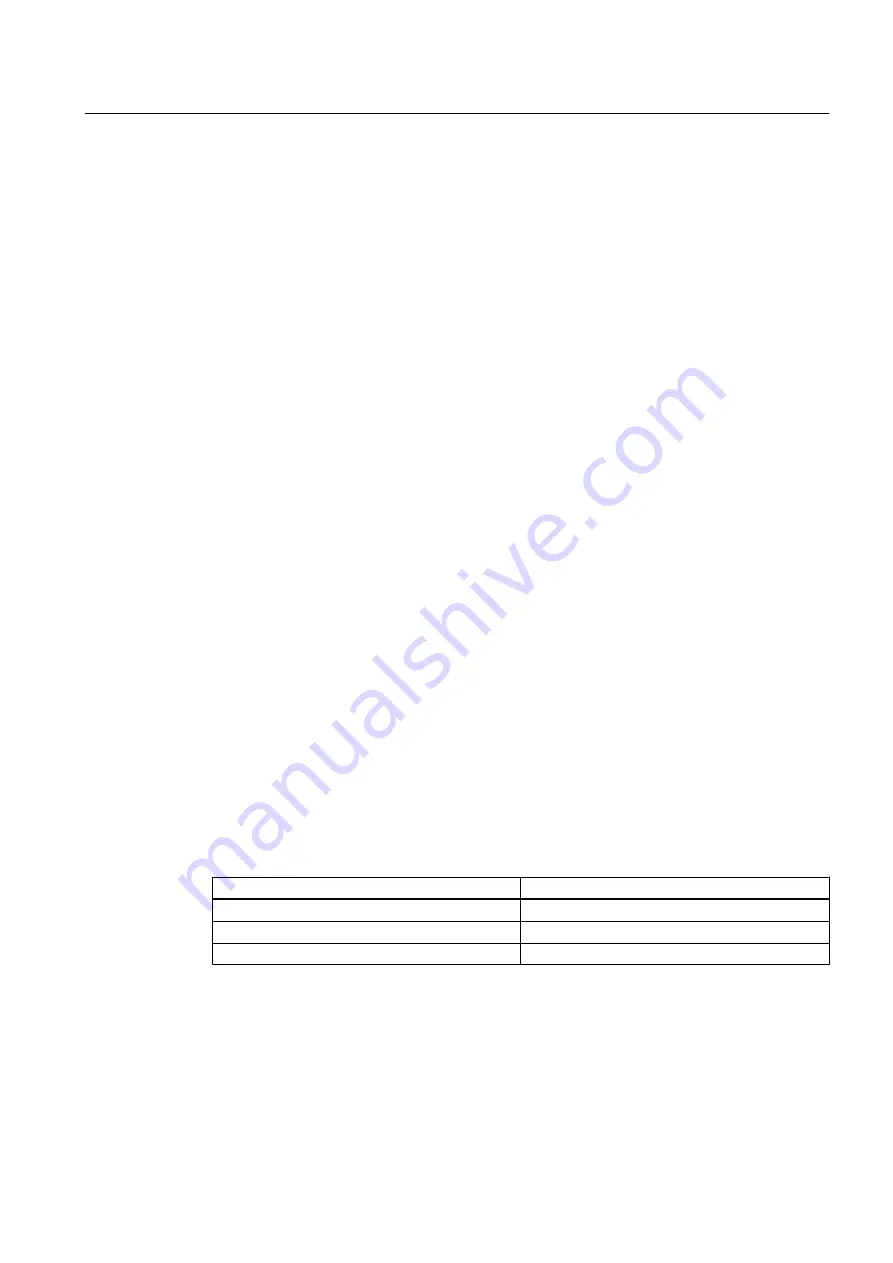
4.9
Torsional loading of the drive train due to faults in the electrical supply
In the event of faults in the electrical connection, such as line switching operations with a
residual field or short circuit at the terminals, excessive air gap torques can occur. These
excessive air gap torques can lead to additional mechanical torsional loads on the shaft
assembly.
If the configuration does not correctly recognize the mechanical torsional loadings of the shaft
assembly, this can lead to serious damage to the machine. This can result in death, serious
injury or material damage.
● When planning the system, make due allowance for the maximum air gap torques that can
occur. This data can be found in the "Electrical data".
The system planner is responsible for the entire drive train.
4.10
Switching high-voltage motors
If vacuum circuit breakers and vacuum contactors are used, then what are known as multiple
restrikes can occur when the machine is switched off. This depends on various factors, such
as:
● Arc-extinguishing principle of the switch
● Machine size
● Length of the power supply cable
● System capacitance, etc.
A surge suppressor to ground is installed in the switchgear between the circuit breaker and
the cable termination for each of the three conductors. The level of protection for the machine
windings is sufficient when the limiter is correctly selected (machine rated voltage / response
voltage).
Example
This current limit corresponds to the following upper power limits, depending on the relationship
between the starting current I
A
and rated current I
N
and on the voltage dip (up to approximately
20%) while the machine is starting up:
Table 4-1
Power limits
Rated voltage V
N
Power limit
3 kV
750 kW
6 kV
1500 kW
10 kV
2500 kW
See also
Prior to commissioning (Page 69)
Preparations for use
4.9 Torsional loading of the drive train due to faults in the electrical supply
SIMOTICS HV C 1NB1402-2AA84-4CA0-Z
Operating Instructions 06/2018
25
Summary of Contents for 1NB1402-2AA84-4CA0-Z
Page 2: ...26 06 2018 15 34 V3 00 ...
Page 10: ...Table of contents SIMOTICS HV C 1NB1402 2AA84 4CA0 Z 10 Operating Instructions 06 2018 ...
Page 22: ...Description SIMOTICS HV C 1NB1402 2AA84 4CA0 Z 22 Operating Instructions 06 2018 ...
Page 84: ...Operation 8 9 Faults SIMOTICS HV C 1NB1402 2AA84 4CA0 Z 84 Operating Instructions 06 2018 ...
Page 112: ...Service and Support SIMOTICS HV C 1NB1402 2AA84 4CA0 Z 112 Operating Instructions 06 2018 ...
Page 117: ...117 ...
Page 118: ...118 ...
Page 119: ...119 ...
Page 120: ...120 ...
Page 121: ...121 ...
Page 122: ...122 ...
Page 123: ...123 ...
Page 124: ...124 ...
Page 125: ...125 ...
Page 126: ...126 ...
Page 127: ...127 ...
Page 128: ...128 ...
Page 129: ...129 ...
Page 130: ...130 ...
Page 133: ...133 ...
Page 148: ...148 ...
Page 150: ...Additional documents SIMOTICS HV C 1NB1402 2AA84 4CA0 Z 150 Operating Instructions 06 2018 ...
Page 154: ...Index SIMOTICS HV C 1NB1402 2AA84 4CA0 Z 154 Operating Instructions 06 2018 ...
Page 155: ...AF Einbauerklärung Loher LDX U157 AJ EC Declaration of Conformity U161 ...