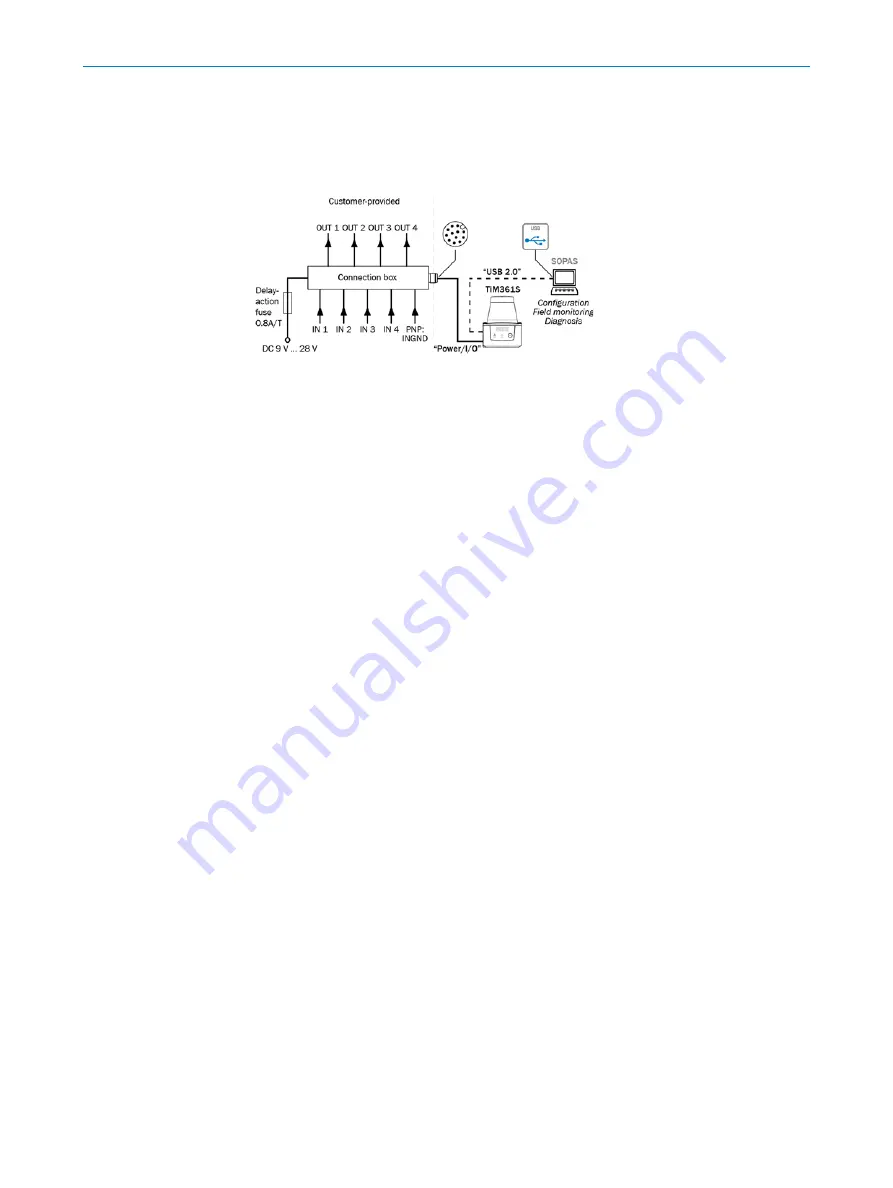
5
COMMISSIONING AND CONFIGURATION
18
SAFETY-RELATED 2D LIDAR SENSOR | TIM361S
8022483/108R/2018-07-09 | SICK
Subject to change without notice
5
Commissioning and configuration
Electrical block diagram for commissioning:
TiM361S-2134101
5.1
Notes on the electrical installation
Requirements for the IP 65/IP 67 enclosure rating: the black rubber plate (USB
female connector) must be flush-mounted on the housing.
Protect the TiM361S against moisture and dust when the cover to the USB female
connector is open.
Electrical connections between the sensor and other devices may only be made or
separated in a voltage-free state. Otherwise, the devices may be damaged.
Wire cross-sections in the supply cable from the customer’s power system should
be chosen in accordance with the applicable standards.
All electrical circuits connected to the sensor must be configured as SELV or PELV
circuits (SELV = Safety Extra Low Voltage, PELV = Protective Extra Low Voltage).
The supply voltage of the TiM361S must be secured accordingly.
Only switch on the supply voltage to the sensor when the connection tasks have
been completed and the wiring has been thoroughly checked.
5.2
Prerequisites for safe electrical operation
The sensor is designed and tested for electrical safety in accordance with
IEC 61010-1:2010-06.
It is connected to the peripheral devices (voltage supply, control, actuators) via
shielded cables. The cable shield – for the supply cable, for example – rests against
the metal housing of the TiM361S. The device can either be grounded through the
cable shield or through both fastening latches.
If the peripheral devices have metal housings and if the cable shields also lie on their
housings, it is assumed that all devices involved in the installation have the same
ground potential.
This is achieved by complying with the following conditions, among others:
Mounting the devices on conductive metal surfaces
Correct grounding of the devices/metal surfaces in the system
Low-impedance and current-carrying equipotential bonding between areas with
different ground potentials, if necessary.
If these conditions are not met, e.g., on devices in a widely distributed system over
several buildings, potential equalization currents may, due to different ground
potentials, flow along the cable shields between the devices and create hazards or
malfunctions.