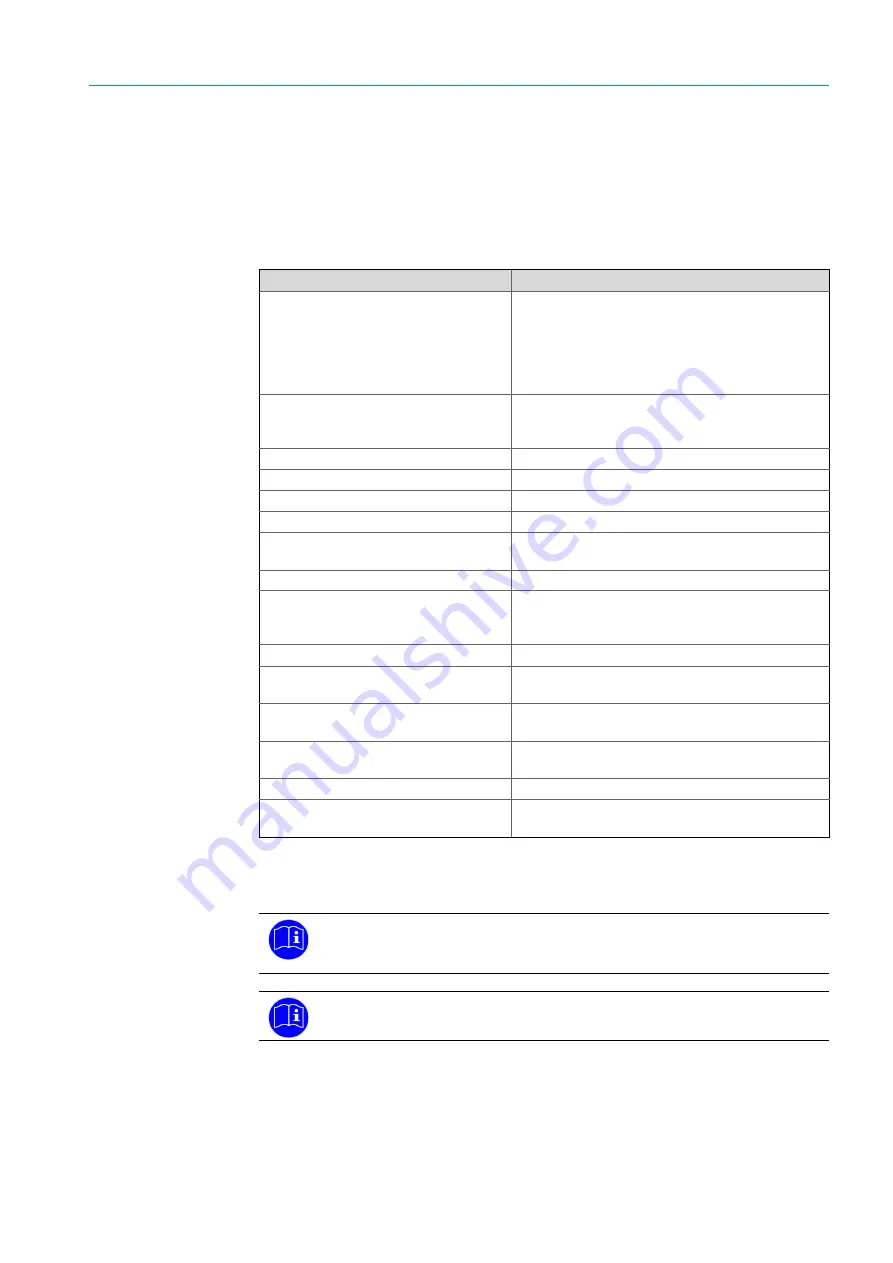
35
8019897/V2-0/2017-12| SICK
O P E R A T I N G I N S T R U C T I O N S | PowerCEMS100
Subject to change without notice
COMMISSIONING
6
6.9
Restarting after longer shutdown
▸
Contact SICK Customer Service to clarify individual precautionary measures required for
a restart after a longer shutdown (several weeks).
▸
Ensure the following as preparatory work for clarification:
– Check the system and system components are ready for operation,
see following Table.
System component to be checked
Check for:
Lines/hoses
– Condensate residues
– Blockage
– Contamination
– Cracks
– Porous or brittle material
– Tight and correct seat
Filter
[1]
– Condensate residues
– Contamination
– Ready for operation
Humidifier container
[2]
– Ready for operation
Sample gas pump
– Ready for operation
Water trap
[3]
– Condensate residues
Analyzers
– Ready for operation
NO
x
converter (option)
– Ready for operation
– Cartridge
Gas cooler
– Ready for operation
Span gases
– Use-by date
– Remaining reserves
– Pressures
System cabinet climate control
– Ready for operation
Gas monitor / Gas measurement
computer
– Ready for operation
Condensate collector
(with level switch)
– Ready for operation
– Fill level
Sample gas outlet, sample gas recircu-
lation
– Blockages
Sampling probe
– Ready for operation
External components and signal
generators
– Ready for operation
[1] Possibly replace filter elements/inserts
[2] Fill, if necessary
[3] Replace the water trap when condensate is present
System components to be checked prior to commissioning
In addition to this list, also observe the information and conditions for particular
system components in Sections “Commissioning” and “Maintenance” in these
Operating Instructions.
Refer to the Operating Instructions for the individual system components for
further details and information.